The £16,000 Specialized McLaren S-Works Tarmac revealed
Only 250 cutting-edge carbon fibre bikes will be produced
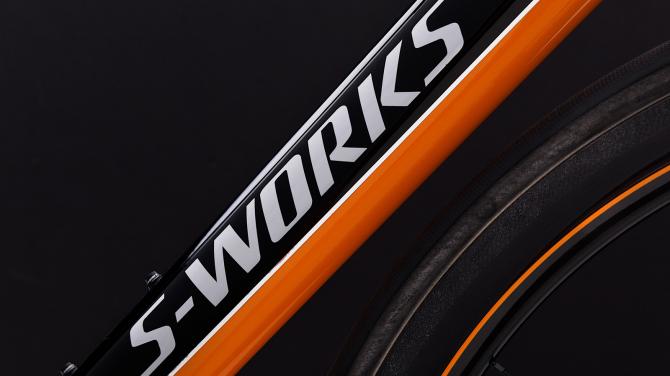
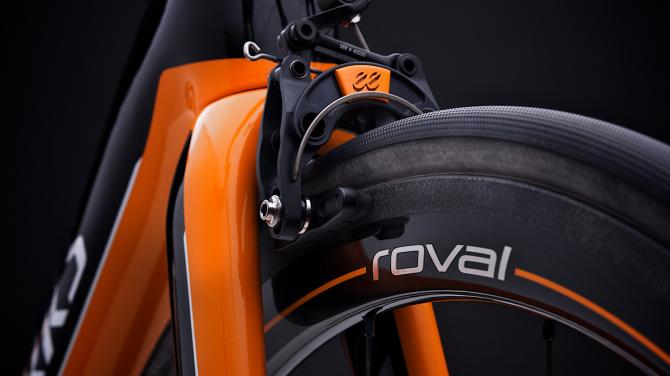
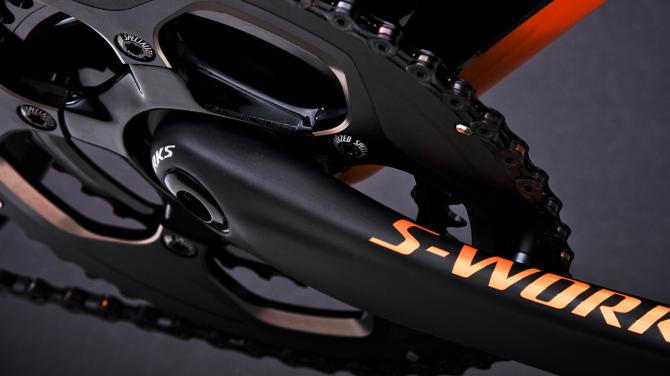
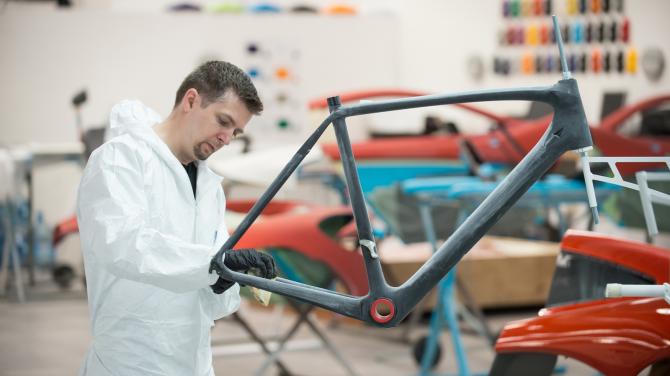
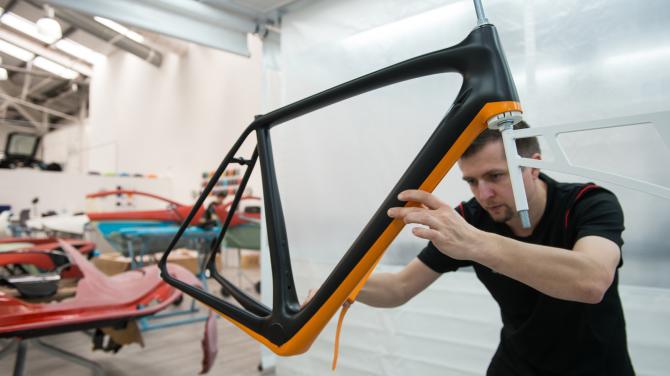
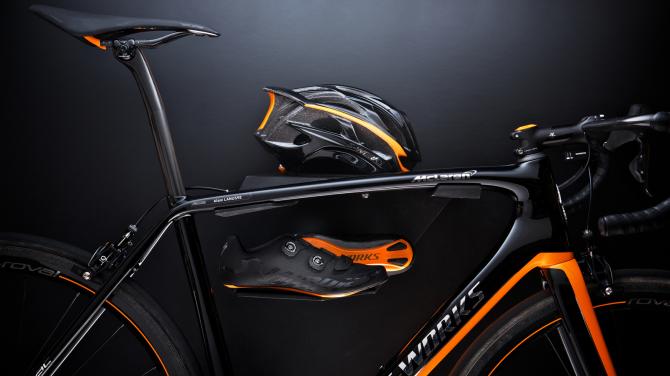
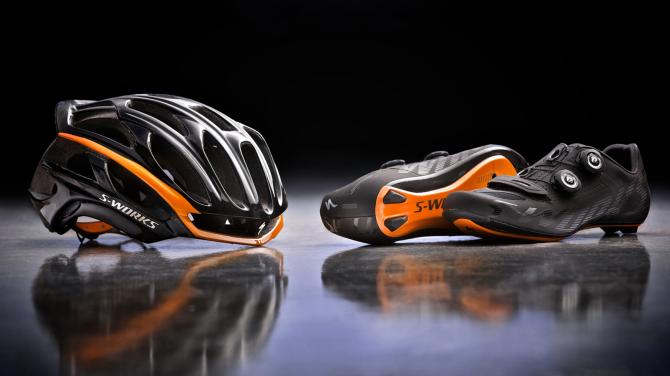
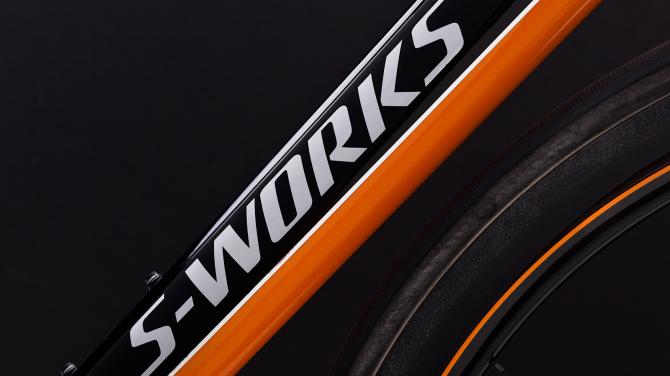
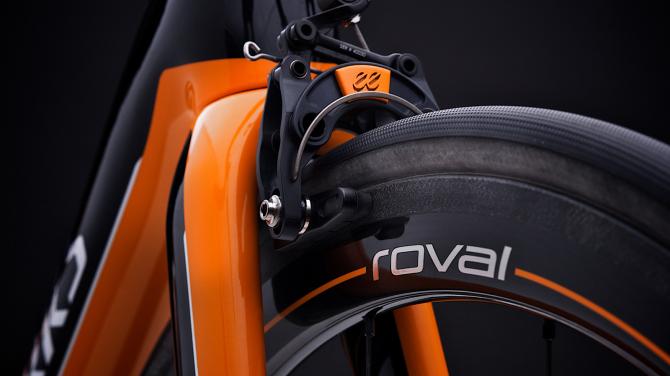
This article first appeared on Bikeradar.
Specialized has revealed the latest fruit of its partnership with McLaren – this £16,000 / US$20,000 McLaren S-Works Tarmac. It’s extremely limited – just 250 will be available worldwide.
This eye-wateringly expensive bike represents the pinnacle of carbon fibre bike design, and has been created as a result of the high-tech research methods employed by McLaren. These include a data cutting-edge simulator and data acquisition processes that allow them to design, drive and test before a piece of carbon has even been placed in a mould.
The McLaren S-Works Tarmac is based on the latest S-Works Tarmac. As soon as that bike was finished, it was presented to McLaren’s Applied Technolgies Ltd unit, where Joe Marsh, composite design engineer at McLaren, took it further into the cutting edge of carbon fibre design.
The frame’s carbon construction has been optimised using the software that McLaren developed its their F1, Super, and Hypercar designs, and that’s led to a weight reduction of between 9 and 11 percent depending on frame size.
Joe said: “Our design benchmark, the new S-Works Tarmac, was already a very, very efficient structure to start with and in some ways this was a much tougher challenge than the Venge we worked on.
“The McLaren uses 300 percent more high-modulus fibres in its construction, reducing material and therefore weight. We've also used more than 500 unique carbon-fibre ply shapes in the construction –that’s 300 more than the standard S-Works'.
Get The Leadout Newsletter
The latest race content, interviews, features, reviews and expert buying guides, direct to your inbox!
And it’s not just the frame that’s had the McLaren treatment – the Roval wheels used on the bike have been refined too. The tubular carbon rim has been reworked, to drop 30g from its overall weight, while the hubs are fitted with full ceramic speed bearings to reduce friction loss. The new wing-shaped aerofly bar has also dropped 30g, thanks to McLaren’s input.
The finish is also very special. All of the frames and forks are painted in McLaren’s paint shop in the heart of the Woking technology centre, by the same team that paints the €1,000,000 P1 Hypercar finish.
The piano black and orange Tarmac looks impressive just at first glance, but get up close you’ll notice a very fine metallic tint buried within both the 'Tarmac' black and classic McLaren ‘papaya' orange.
Size matters
From its research, the R&D team quickly realised that not every rider’s needs are the same. The Tarmac is available in six sizes from a 48 to a 61cmm and the data showed two key discoveries. Firstly, that the forces enacted on the bike were vastly different, and secondly, the way the bike handled under smaller riders was different to how it handled under a taller rider.
The previous Tarmac underneath a small light rider was found to be overly stiff, making the handling through corners prone to bouncing across the road surface and understeering, costing the rider valuable pace. At the other end of the scale it was found that under a larger rider, the bike wasn't quite structurally stiff enough, making the handling more biased to oversteering.
This has led to a radical change in the way the frames are designed throughout the size range. The most obvious change is in the diameter of the down tube – the smallest bike has a 45mm diameter tube section and the largest size gains an extra 20mm, making for a massive 65mm diameter tube.
This rider-first fit features on the standard Tarmac range, not just S-Works, and we'd expect these design parameters to be rolled out across the whole of Specialized's performance bike ranges.
Construction
The biggest challenge facing Specialized with McLaren’s take on the Tarmac is actually producing it – Specialized has created a separate production line to build this highly-limited run to the exacting standards required. Only the most highly-skilled technicians will work on it.
The line is in a temperature controlled environment and frame moulds and part-finished sections are vacuum stored, both processes that McLaren uses in the production of its vehicles.
So how do you get one?
Of the 250 being made, just 10 are expected to come to the UK. Getting the bike isn't as straight-forward as visiting your local Spesh dealer – first you have to register interest and reserve a bike at the Specialized website. Then you'll then be contacted by Specialized to schedule a Body Geometry fit session, as the bike also comes with a unique Mclaren S-Works Prevail helmet and custom-fitted S-Works McLaren shoes.
The fit data is combined within the bespoke order form and the bike will be built after you’ve paid hefty deposit. The bike is delivered with shoes, helmet, and a display rack bearing the rider’s name and the edition number. A plate bearing the same details is bonded onto the top tube of the bike too.
Specialized told us interest is already high, with many enquires coming from existing McLaren Venge owners. The webpage opens today and runs until 31 July.
As a showcase for where the Specialized/McLaren relationship is heading, the Tarmac is a bold statement. The data-acquisition technology will change how Specialized creates its future bike ranges, but the biggest challenge they face is how to implement lessons learned from cutting-edge projects like this one into mass-produced ranges.
If they can do it, it'll change bike design forever and might just give Specialized the edge over their competition.