‘The human element will not be eliminated anytime soon’ - Dimitris Katsanis on 3D printing, AI, and the future of carbon fibre
Will the world's first completely 3D printed road frameset help usher in a new era of frame manufacturing?
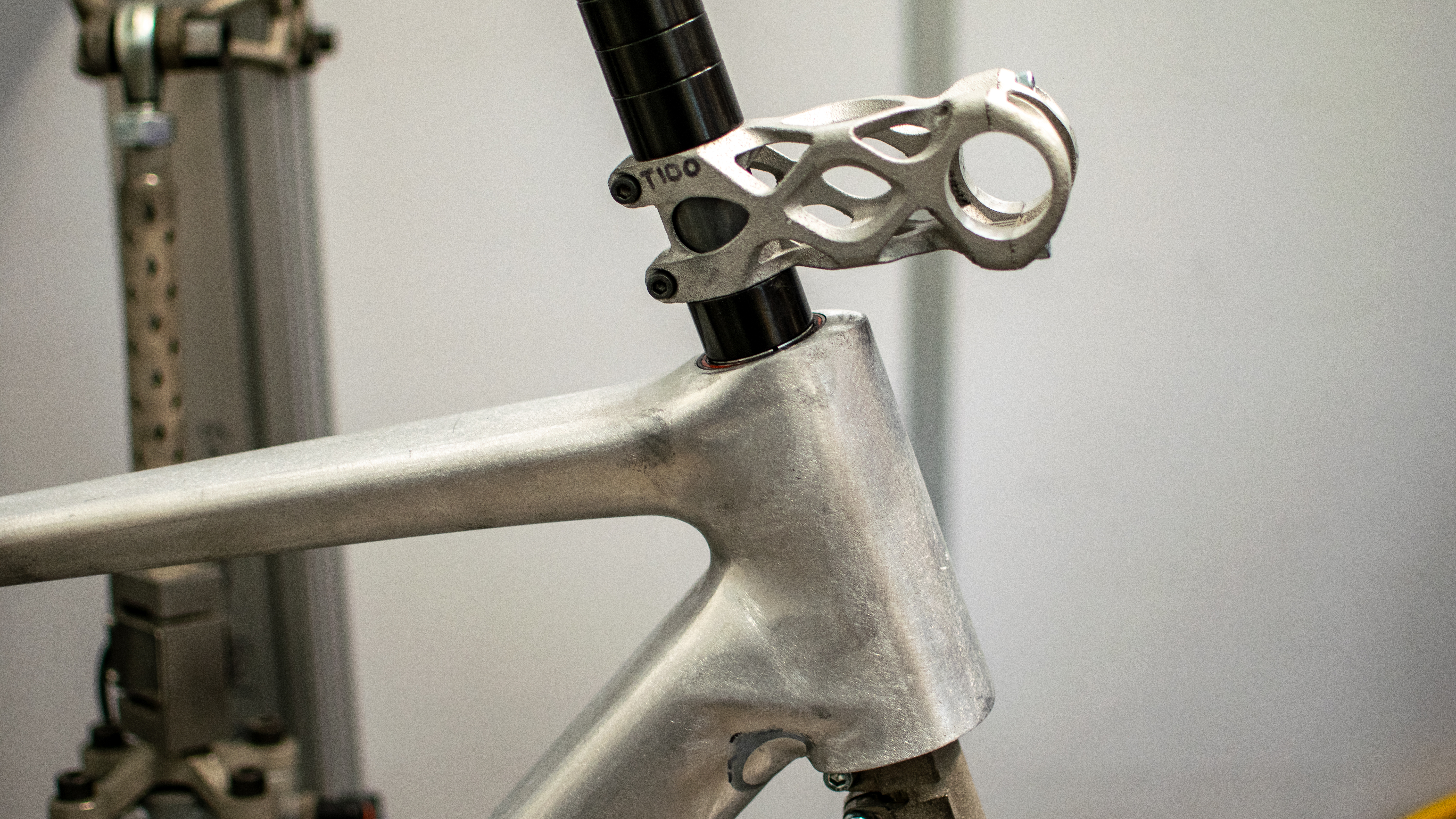
“Do you ever see a bike racing on its own? No.” Dimitris Katsanis, with the faintest flicker of a grin, is explaining the need for an aerodynamic ‘total system’ when it comes to going fast on a bike.
Frame, components, the rider, along with plenty of other things, need to work in harmony together to achieve an effective aerodynamic total system. In short, anyone can have a fast bike, but it’s getting everything lined up together that’s the trick, so that when the rider races the bike, things stay fast.
Katsanis is a designer, engineer, and composites expert who sits in a unique position within the cycling world. His work and designs have been used to win over 100 Olympic and World Championship medals, on both the track and road. Katsanis admits that once that 100 mark was broken, he stopped keeping track.
Hailing from Greece, Katsanis has lived in the UK for over thirty years. Some success on the track riding for the Greek national squad came, but he moved to the UK in 1993 to study composite engineering at Plymouth University.
In the last thirty years or so, bike design and technology have changed dramatically. In that time, the sport has transitioned from using welded steel frames to aluminium, magnesium, aluminium and carbon, to carbon fibre and 3D printed metal, which is where Katsanis is now focusing his efforts. Throw in all the aerodynamic and component advances, and things are different beyond recognition.
Katsanis has witnessed all of that change and been at the forefront of design for the last thirty-odd years. At first, producing his own Metron carbon frames around the turn of the millennium, before going on to work with UK Sport, designing the Great Britain UK Sports Institute (UKSI) track bikes and being a member of the famous GB ‘Secret Squirrel’ testing group.
He’s consulted for the UCI, and worked on countless design projects for some of the sport's biggest names, been involved with projects like Bradley Wiggins' and Filippo Ganna's respective World Hour Record bikes, and plenty of projects for Team Sky and Ineos Grenadiers on the road.
Get The Leadout Newsletter
The latest race content, interviews, features, reviews and expert buying guides, direct to your inbox!
That’s to say nothing of the numerous projects that are off the record. Katsanis' role has often been done behind the scenes, with his finished designs often bearing someone else's brand name.
He owns and runs his own business: Metron Additive Engineering, comprised of a small team which operates across a range of industries from automotive to medical. They design, manufacture and internally test all components in-house.
Sitting alongside Metron, however, is the Mythos brand, specialising in 3D printed cycling components. Cyclingnews visited the Metron premises in Derbyshire, UK, to chat with Katsanis about his storied career, what he thinks the future holds for bike manufacturing and technology and his latest project: a complete 3D printed frame.
Catching the world asleep
Katsanis' name crops up regularly when it comes to talk of British Cycling and its rise to complete track dominance over the past two decades. A great many world- and Olympic titles were won on the stealthy black UKSI track bikes that Katsanis helped to design.
He hands me an MK1 frame in his office. It doesn't look or feel dated. It's followed by a later road-going version, which was Bradley Wiggins' spare TT frame at the 2012 Olympics. Then comes an early iteration of the Hope and Lotus-manufactured track frame the squad uses today. There is an almost 25-year evolution of frame design to be observed that Katsanis is largely responsible for.
British Cycling first approached Katsanis in late 2001 to have a frame ready to use for the 2002 Commonwealth Games in Manchester, and then the Athens Olympic Games in 2004. Katsanis went away and created that MK1 UKSI frame, and they were successful immediately.
Katsanis tells me Chris Hoy knocked a quarter of a second off his flying 200 metre time the first time he rode it, a huge amount on the track.
In the Metron office's boardroom, I spot a framed photograph of a group of people sitting around a table in what looks like a hotel bar. Katsanis explains that it's most of the famous and now well-reported-on Great Britain team's 'secret squirrel club’. A group that included members of the Team GB setup, like Chris Boardman and Rob Hayles, aero expert Rob Lewis, as well as other key people from UK Sport.
The group tried to leave no stone unturned in an attempt to maximise equipment and clothing gains for the GB track squad during this time.
Everything from frames, wheels, components, helmets, and skinsuits were all designed and then tested in the wind tunnel repeatedly, a special group of riders and equipment that was ahead of the game, resulting in Team GB in Katsanis' words: "catching the rest of the world asleep" at the 2008 Beijing Olympics. Team GB was supremely dominant on the track, claiming multiple gold medals, shattering world and Olympic records in the process.
Katsanis speaks at pace and with passion on a range of cycling and engineering subjects. It would be all too easy to spend hours going over his interesting anecdotes on the golden period at British Cycling.
Although his engineering and design knowledge is beyond question, he makes a fascinating point on the cyclical nature of things. Nations and teams will have their eras of dominance, this has always been the case. We only have to look at Team GB at its peak on the track or Team Sky's grand tour dominance.
Ideas and funding also come and go (sponsorship led to Team GB switching to Cervelo bikes in 2016). Sometimes the original thought or idea exists, but the passage of time itself and improved technology allow for existing ideas to be followed up on and developed, resulting in real improvements.
Katsanis can see the big picture for himself and explains that some ideas need revisiting and exploring to arrive at a breakthrough, even after they pass beyond living memory.
He produces a reprinted copy of a book on bicycle engineering from 1896 to demonstrate.
"This book is from 1896," he begins. "There is a graph in which somebody calculated the air resistance, the rolling resistance, and the friction from mechanical losses, and it's calculated by hand. They didn't have wind tunnels. And if you look at the graph, it is broadly correct. The physics hasn't changed.
"I managed to unearth an article from an American magazine from 1989. They had a graph on how friction goes up when the rear sprocket starts getting very small. The friction starts really shooting up from roughly 14 teeth and below. If you look at the graph on how the friction increases, you wouldn't use it. I cannot claim that I discovered that, but I rediscovered it, and we looked at it.
"A lot of the skinsuits that you see today have arms that feature some sort of intervention, either with dimples or with lines or something similar. We did the research, the basic research for this, in 2008 and 2012. Then everybody else thought 'there's something there'. Today, every high-level skin suit has some sort of intervention."
Katsanis explains he also learnt a lot during the secret squirrel period, and experimenting with his new ideas led to some big improvements.
"I read a lot of books, tried a few things in the wind tunnel. I was lucky enough that when I had the crazy idea, they allowed me to try the crazy idea. And I was lucky that some of the crazy ideas worked. Not all of the ideas, but most of them, somehow worked.
"It's knowledge, a bit of intuition and maybe a bit of luck, and not giving up."
What next for carbon fibre?
A large part of Katsanis' career has been spent with composites and working with carbon fibre. He embraced the material when the technology to work with it regarding bikes was in its ascendancy.
“In 1991 or '92, I thought 'the future is carbon fibre, I'm going to study that.' Carbon fibre in the early 90s was a relative unknown, very much like what 3D printing is today. In the early 90s, there were steel bikes and mainly aluminium bikes, then carbon started coming in. Then, from some point in the 2000s, carbon completely dominated."
Katsanis started to believe around 2012, after the London Olympics, that what could be done with carbon fibre was diminishing. His view is that there isn't a huge amount of room for improvement. Frame shapes are becoming more complex as aerodynamic designs are improved, but the way carbon frames are made doesn't lend itself as well to these more complex designs from a time, cost, and difficulty perspective.
"Can you implement new technology like aero and so on? Yes, but you're coming to the point that the next stage is individualisation, customisation, and interactions with the rider. And that currently cannot be done with carbon, not regarding the material itself, but the manufacturing techniques, like the moulding.
"When you start getting into complex shapes, carbon fibre is not the best material. If you want to have complex shapes, 3D printing can give you easier complex shapes. I do think that carbon fibre, it probably reached what you can do with the material not far from 10-15 years ago, and since then, it's variations of the same thing. That was my view after 2012.
"In my personal view, the future development is not making individual parts more aero. We read speculation on whether we have reached peak aero and so on. That's not far from the truth. You can only make the tubes in so much of an aerodynamic shape. And beyond that point, you get very diminishing returns. I think the future is in the interactions. One is customisation, because you have to remember that since carbon fibre became the dominant material, the dominant manufacturing process is making a mould to make a component in carbon, and that actually puts restrictions on the number of variations that you can have. On the frames, on the handlebars, on everything."
Katsanis has focused on 3D printing since around 2012, and believes that achieving a more aerodynamic total system, as well as being able to quickly tailor and manipulate frame and component shapes, is more easily done with 3D printing technology. This has led him to produce his own components as well as come up with a 3d-printed road frame. He's also 'crystal ball gazing' - in his words - regarding reacting to developments in AI design technology that will complement 3D printing well.
"That ability to adjust the bike to your size is pretty much lost with the carbon moulding techniques. This is why I think the next step is not so much making the frame more aero or the handlebars more aero, but on how you can make the body more aero, how you can put the body in a more aero position. And how you can have the different parts of the bike interacting with the rider's body."
3D printed frames and anticipating AI
Although 3D printing or additive manufacturing (other names are also used, but the two mean the same thing) became Katsanis's focus from 2012, the Metron 3D printing journey gathered pace in 2015 when the company designed the frame and fork and provided 3D-printed pursuit bars for Bradley Wiggins' World Hour Record bike.
A tight time schedule meant 3D printing a titanium handlebar was the only option. This kick-started things for the 3D printed bars that are widely used today and presumably boosted 3D printing's stock in the cycling world. One-piece 3D printed time trial handlebars can now also be made significantly lighter than a full carbon fibre alternative, sometimes by up to half a kilogram.
Handlebars have been a strength for the brand. Watch any track endurance race and you will see a number of prominent riders have adopted the Mythos TX-1.1 aero drop handlebar. This is a raw-finish Titanium (Ti6Al4V) 3D printed model available in a range of narrow widths. It provides riders with the ability to race holding onto small 'hoods' and maintain an aero position.
The world's first 3D-printed track frame and fork was created in 2022 for Filippo Ganna's hour record attempt by Metron and Pinarello, and was also used by Dan Bigham.
Now, Katsanis has developed what he believes to be the world's first totally 3D-printed road frame and fork, which has also passed the ISO4210 test. The frame is manufactured from Scalmalloy - a powdered material designed for additive manufacturing and titanium.
3D printed designs start on a computer, and a digital model is created for a job or specific component using programmes like Solidworks or Rhino, along with other 3D CAD (computer-aided design) software.
Things like stress analysis also need to be done to know how much material is needed for component strength in certain areas, which is especially important for something like a handlebar or stem. There was an infamous 3D printed handlebar failure for the Australian track team at the 2021 Tokyo Olympics, for example. This wasn't one of Metron's, but Katsanis explains the failure was due to an incorrect load spec rather than the technology itself.
The model is transferred to a 3D printing machine digital file, which then, in a nutshell, dictates the movements of the print nozzle as well as things like how fast material comes out. Katsanis provides an overall look at the 3D printing process.
"The 3D printing powder has a consistency like flour, so it's very fine. The machine will put down a thin layer of powder, then the beam, usually a laser beam or an electron beam, which will melt the material in the area where your component is.
"So if you were making a flat plate standing up, the machine will melt one line, the base plate will be moved down by whatever your layer thickness is. And then the machine will melt another line, another line, another line, and then you have the component starting to grow upwards in effect.
"[The thickness] is measured in microns, and one micron is 1000th of a millimetre. Usually, the thickness of the layer is anything between 30 and maybe 100 microns, depending on a number of factors. So [for each layer] it will go down by, let's say, the thickness of a piece of paper.
"The process takes hours, and depending on what you do, it may take days. So it's a relatively slow process. When you take the finished components out, depending on what you're making, you may have one component all in one piece, like the handlebars we make."
Katsanis explains it is possible to 3D print a complete frame, but due to the cost and size of the machines currently, it's an uneconomical prospect. It's better to print a frame in parts or sections, then bond it together.
The size of a job's base platform, the plate the component is printed on, dictates what you can make and in how many pieces.
"Most of the time, it's several pieces that you have to join together. We tend to bond things together using an epoxy adhesive, but you can also weld them together. We don't do any welding ourselves. We do frames that are usually a small number of pieces, like five pieces, and we join them together.
"Some machines allow you to print a complete frame and make it all in one piece. But it will be very uneconomical, because machines like this will cost millions. Therefore, it will make the component very expensive, and the machines are few and far between."
Metron has a few 3D printing machines, one of which is an Arcam machine from Sweden. Katsanis explains that the machines need looking after, the costs for one run into hundreds of thousands of pounds, and he cites the need for dependable support based in the UK to ensure operating efficiency. Same day part support recently helped to ensure a certain part could be manufactured for a big WorldTour team, for example.
"At the professional level, these machines are prima donnas in effect. They are not easy to run. They are very sensitive. You do something slightly different on the setup, and they don't like it. They do have a tendency to need frequent services. Things break down, and you need to change parts pretty quickly. You have the customer waiting. So we have to have a machine that has good service in the UK."
Why a 3D printed metal frame?
One part of the equation for Katsanis and the Mythos team is the ability to create a custom solution to meet the needs of all kinds of riders that could be informed by high-level bike fitting.
Katsanis believes a fully custom 3D printed frame could first be fine-tuned to meet the exact fit requirements of whatever a rider is doing, whether it's a climbing stage of the tour, a time trial, or ultra riding etc. The nature of 3D printing also means that, unlike the custom-made round tubed steel frames of 30 years ago, frames and 3D printed components like handlebars can be aerodynamically optimised for individual riders to achieve an effective overall aero system, beyond what is available from more off-the-shelf frames and products.
This is actually already the case with fully custom 3D-printed bars. Finally, more complex aero shapes can also be manufactured this way, which is a lot more difficult to do in carbon fibre.
"I think the future is being able to scan a rider very quickly and accurately, do the CFD quickly and accurately, and make a shape for the components, frame, forks, handlebars, maybe wheels, or whatever else it might be for that rider, and then manufacture it. Then 3D printing comes into it, because if you have all these individualised components, carbon fibre is not the way to go, because you need moulds."
A finished ISO-passing frame has been manufactured and has been extensively tested in-house, with a high-end but off-the-peg build coming in at 7.1kg with pedals. This is certainly competitive weight-wise compared to a carbon offering.
Mythos lists a rough frameset price of around £6,000, though the frame isn't available to order at this point.
There are certainly more expensive framesets out there, custom carbon fibre could easily be several thousand more. Mythos is also partnering with a few specialist bike fitters to develop the offering. One such partner is Lee Prescott, the President of the International Bike Fitting Institute (IBFI). Katsanis explains the total offering isn't wholly fleshed out, but the product is not too far from being finished.
"We already have some movement from manufacturers that are interested in what we're doing. There is at least one reputable brand that we are talking with. We developed the technology, but for the time being, we're not looking to put it on the market ourselves as a bicycle. We're looking for somebody who wants to adopt the technology, and we could end up being the developers.
"My ideal situation is we're going to come to an agreement with a reputable company, and we're going to be doing it for them. If this doesn't come, we may do it ourselves."
Aside from the design and development of the 3D printed Mythos frameset itself, Katsanis is anticipating and planning for the evolution of AI and algorithm-based design software that could usher in a new era of frame manufacturing. It appears there are signs and even existing technology to back this up. If so, additive manufacturing could be the right vehicle to bring a digital design to life much more quickly than it would take a carbon manufacturing process.
"In terms of designing a bike, it will come. The design work right now is based on experience regarding what the rules say, what you've done in the past, and what you have as an idea. So it is a bit of an iterative process, backwards and forwards. In theory, you can teach a machine to do this.
"I always had the joke of having a CAD system that you press the button that says, 'design me a bike', click the button, and it's done. It's not going to be exactly like that, but the early stages of this technology are there.
"We are talking with a group of people and they claim they have software that, with some teaching, can do it, you can have a picture that you take of somebody, and maybe a video, where the rider is riding the bike and so on. And the AI can extract the sizes, design a frame, do the stress analysis, segment it to put on the start plate of the printing machine, and the machine is going to print it, and it just needs assembly."
Katsanis admits he is trying to look at and be ready for a time several years into the future, where additive manufacturing can react to AI-generated frame designs. His team has already compared stems created by AI-influenced programmes against a human design, and the resulting parts achieved a similar final product, but in a different way.
"I think now I'm saying mass customisation via printing is the future. It will be interesting to see how right or wrong I will be. So in 10 years, we will know. I recognise that this is the direction that we have to go, because if we don't do it, frankly, somebody else will."
Katsanis has been developing and working on new and cutting-edge technology for most of his career. He's still aiming to be ahead of the curve and is not afraid of breaking new ground. The Mythos 3D printed frameset is very nearly ready. The next part of the project is how it comes to market and what that might look like.
"The AI will come in, but the human element will not be eliminated anytime soon.
"You have to have the human element of Scott Draw at UK Sport, picking the right people to develop things. You have to have the human element of Fausto Pinarello saying, 'Yes, I think that idea will work.' You have to have the human element of Lee Prescott saying, 'I can see this developing.'
"I don't think AI will come to that, at least not anytime soon. So I see the human element driving the innovation and pointing things in the right direction, that's really how humans develop."
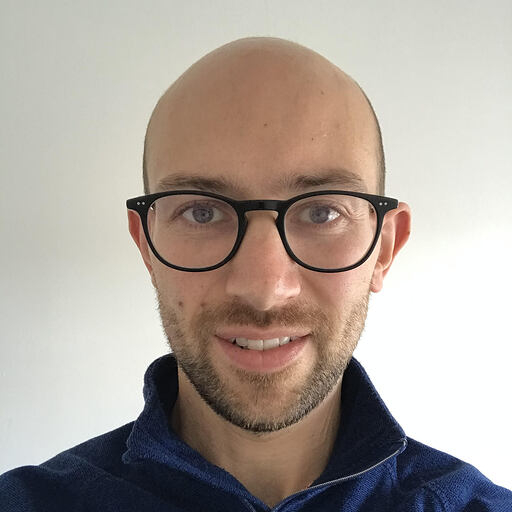
Tom joined the Cyclingnews team in late 2022 as a tech writer. Despite having a degree in English Literature he has spent his entire working life in the cycling industry in one form or another. He has over 10 years of experience as a qualified mechanic, with the last five years before joining Cyclingnews being spent running an independent workshop. This means he is just as happy tinkering away in the garage as he is out on the road bike, and he isn’t afraid to pull a bike apart or get hands-on with it when testing to really see what it’s made of.
He has ridden and raced bikes from an early age up to a national level on the road and track, and has ridden and competed in most disciplines. He has a keen eye for pro-team tech and enjoys spotting new or interesting components in the wild. During his time at Cyclingnews, Tom has already interviewed some of the sport's biggest names including Mathieu van der Poel, Tadej Pogačar and Alberto Contador. He's also covered various launches from brands such as Pinarello, Ridley, Specialized and more, tackled the Roubaix Challenge sportive aboard his own rim-brake Cannondale SuperSix Evo, tested over 20 aero helmets in the wind tunnel, and has created helpful in-depth buying advice relating to countless categories from torque wrenches to winter clothing.
You must confirm your public display name before commenting
Please logout and then login again, you will then be prompted to enter your display name.