Tech: Inside Giant's Taiwan bike factory, part one
All-access tour inside the world's largest bicycle manufacturer
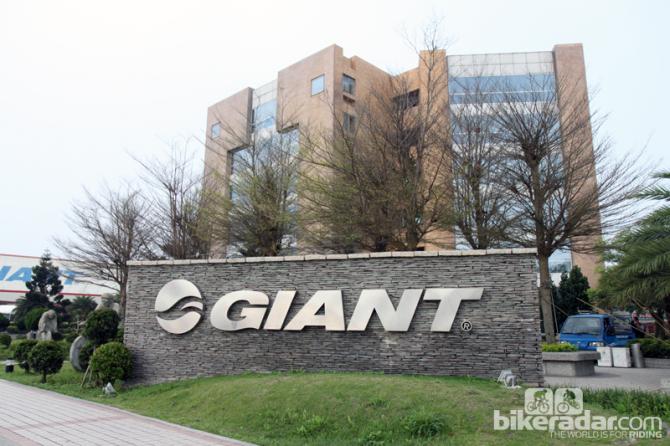
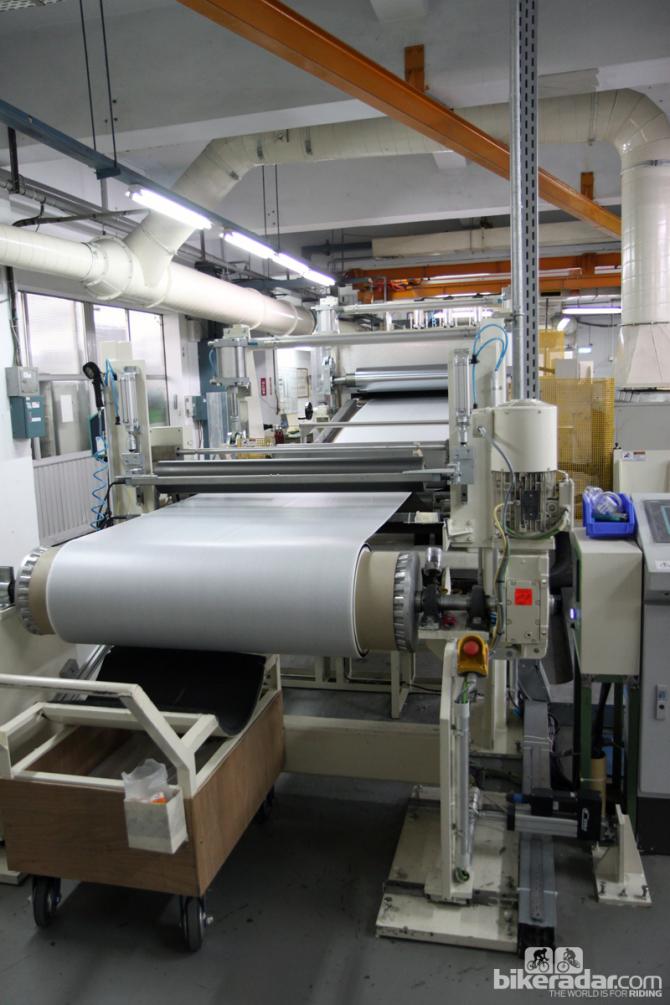
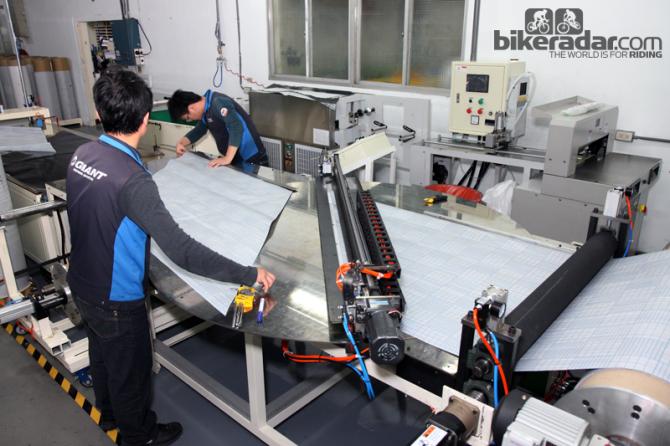
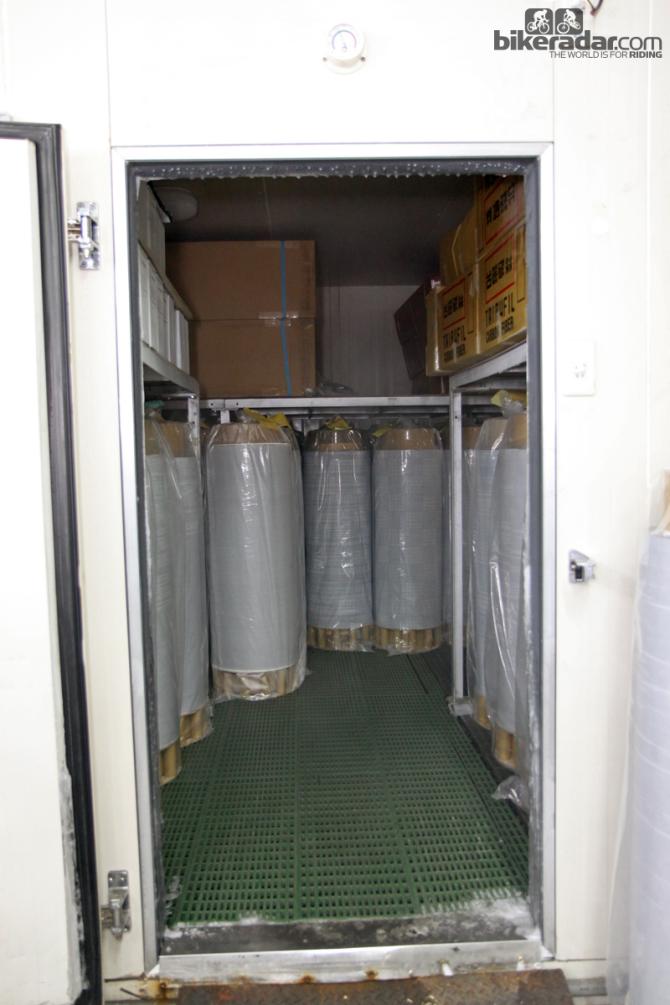
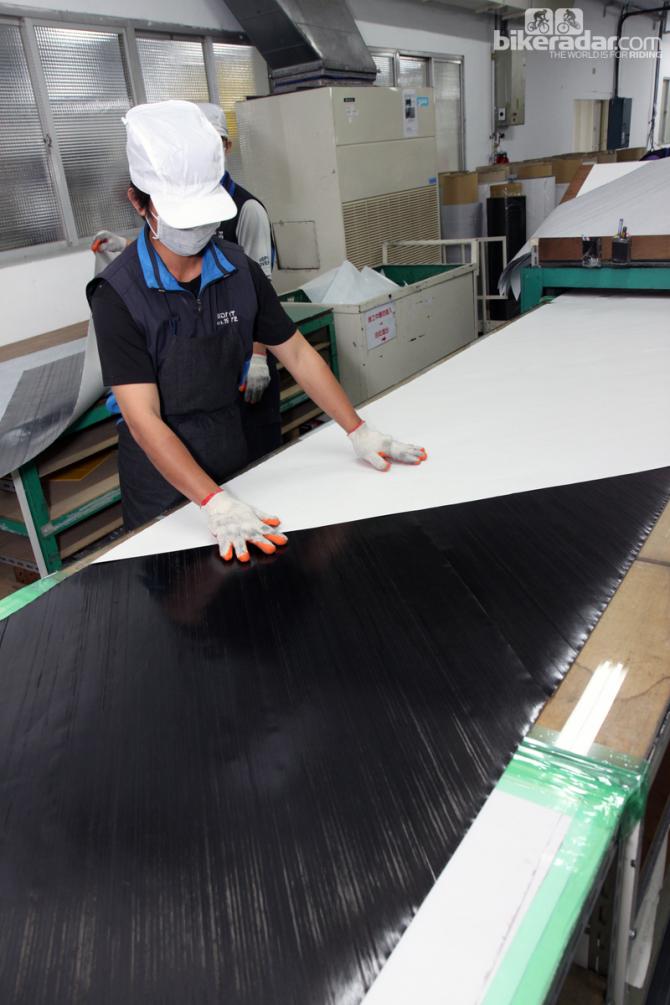
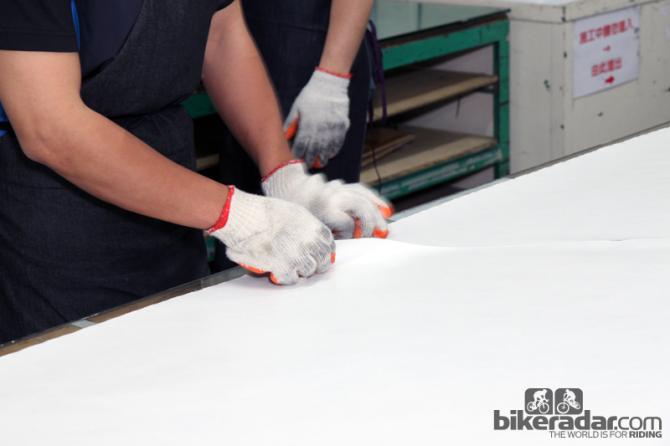
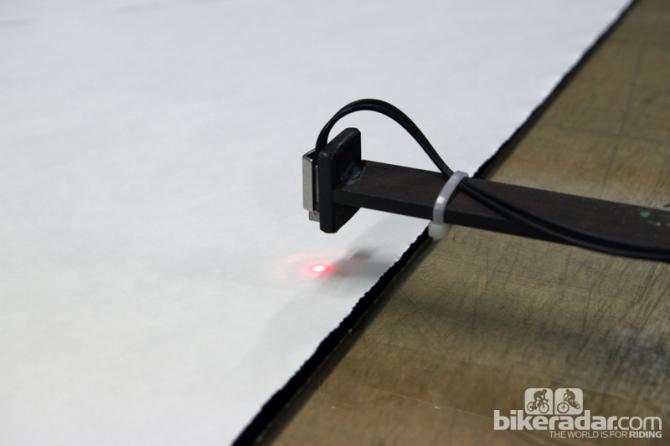
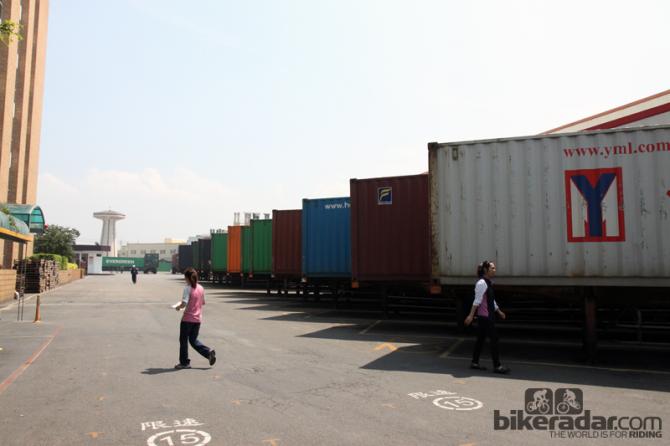
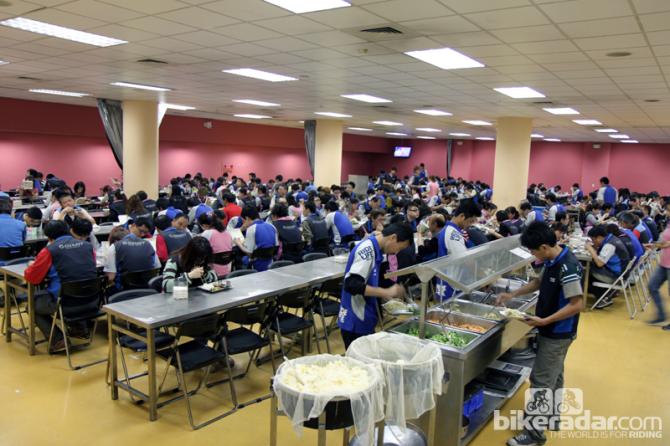
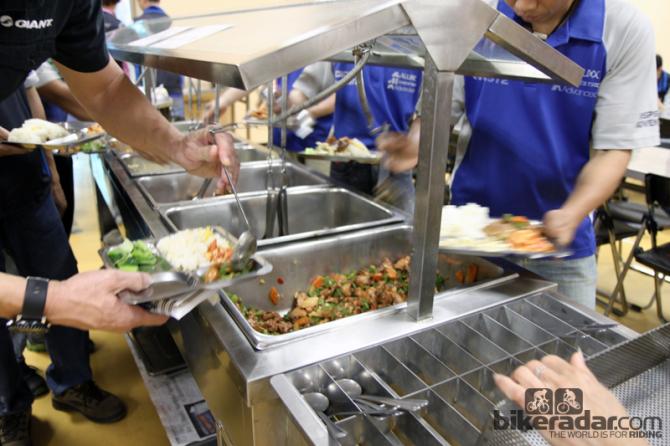
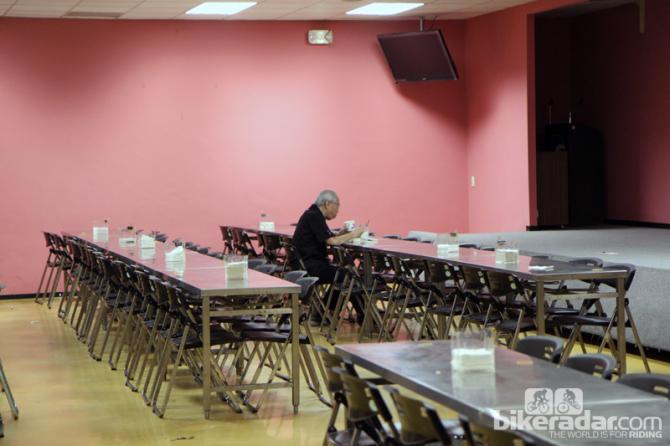
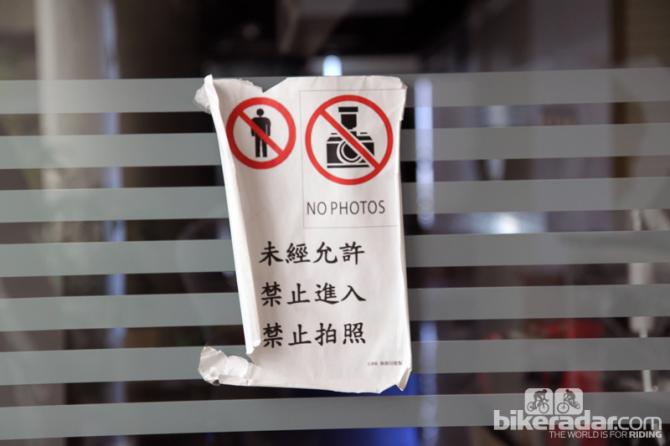
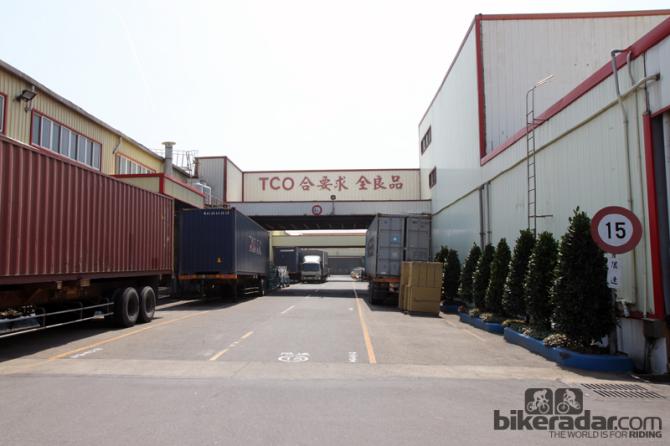

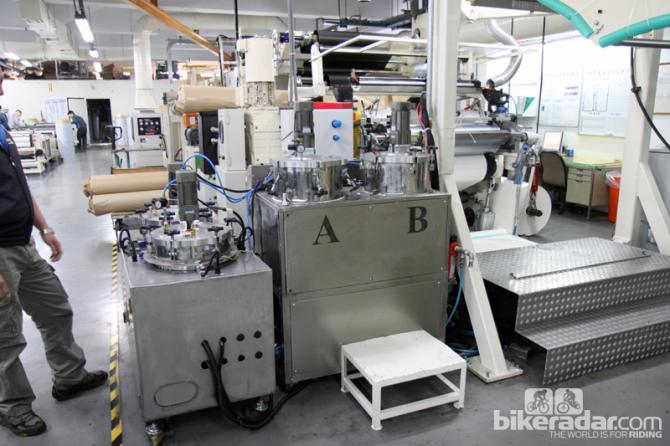
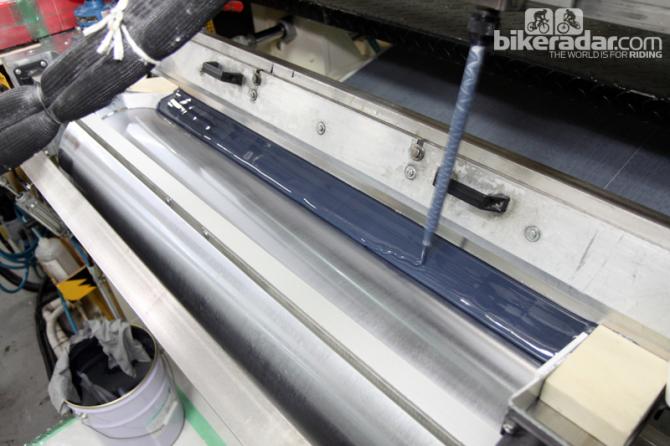


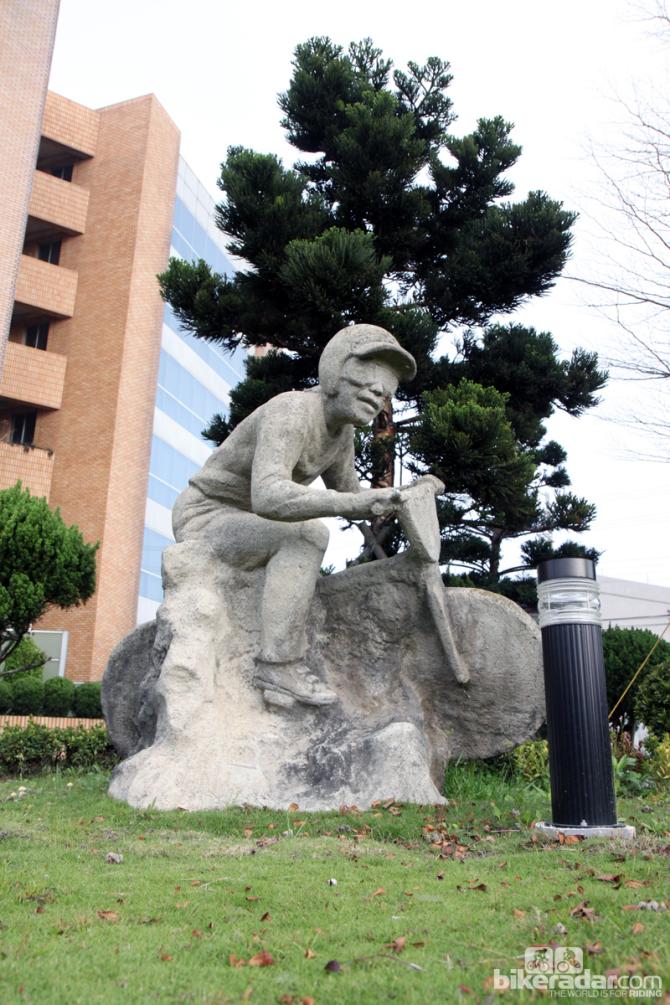
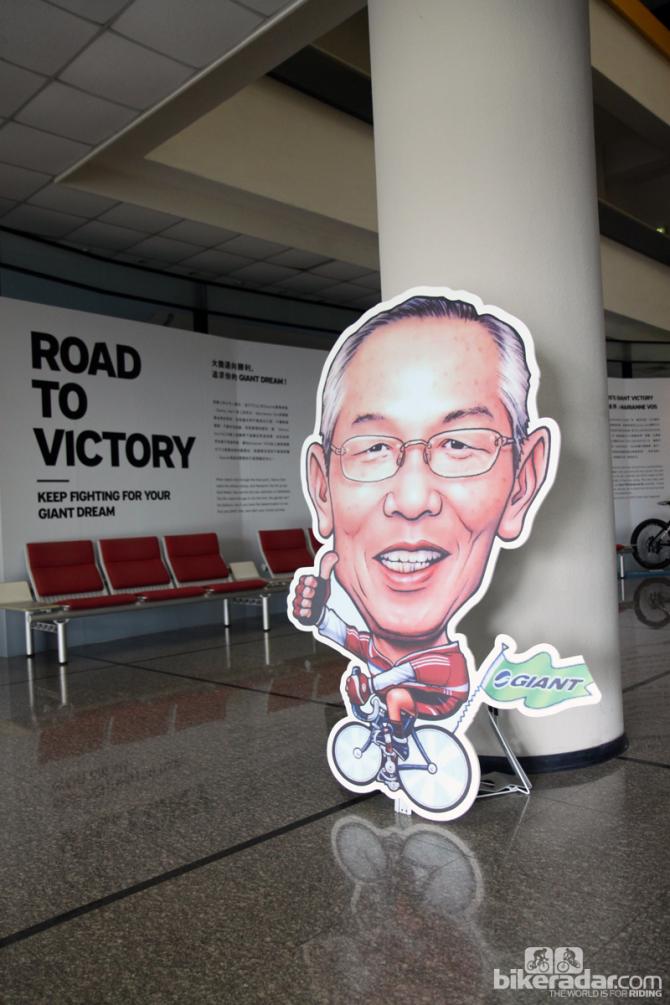
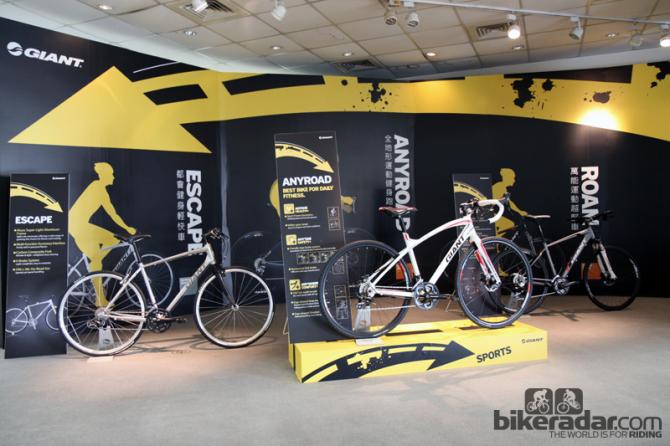
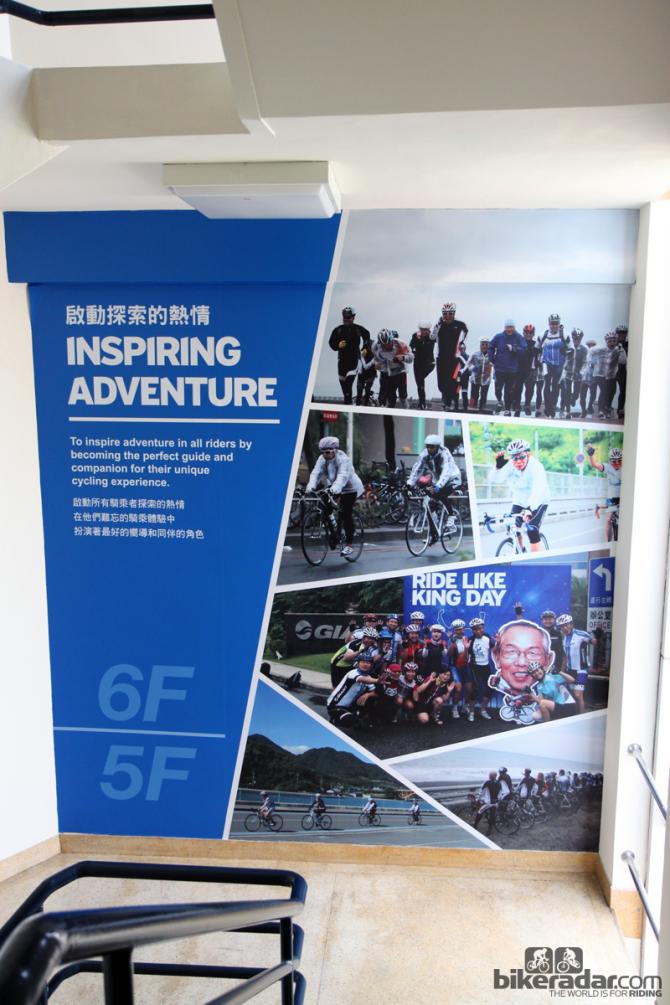
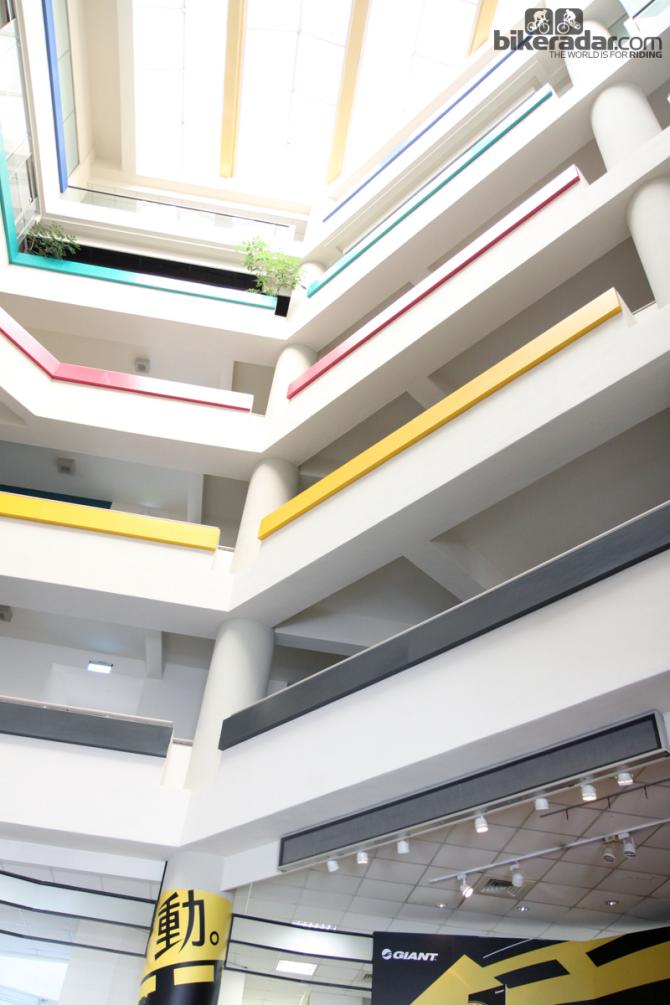
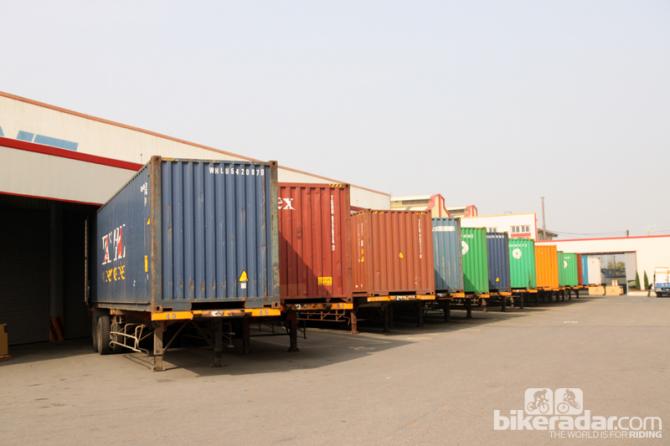

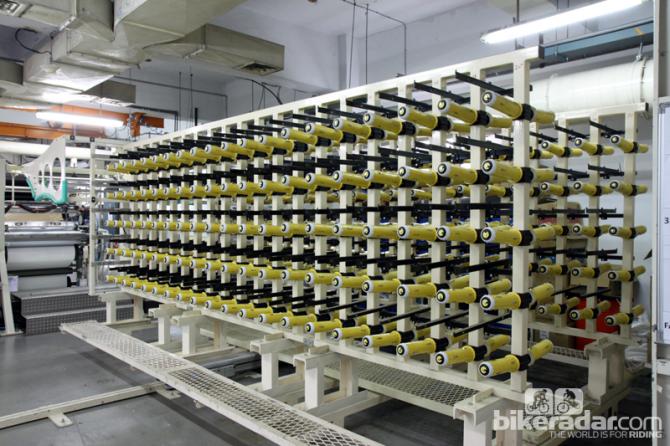
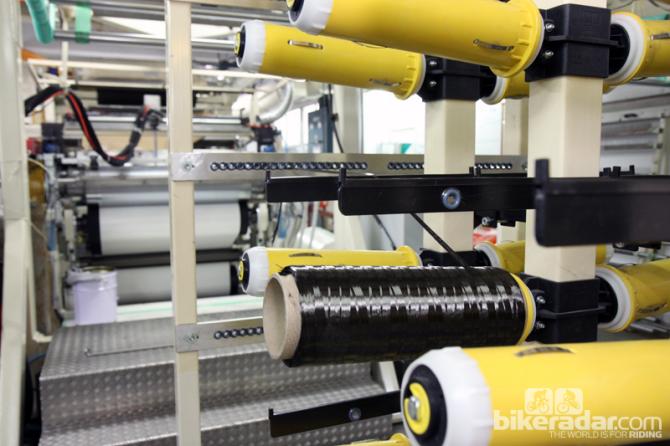
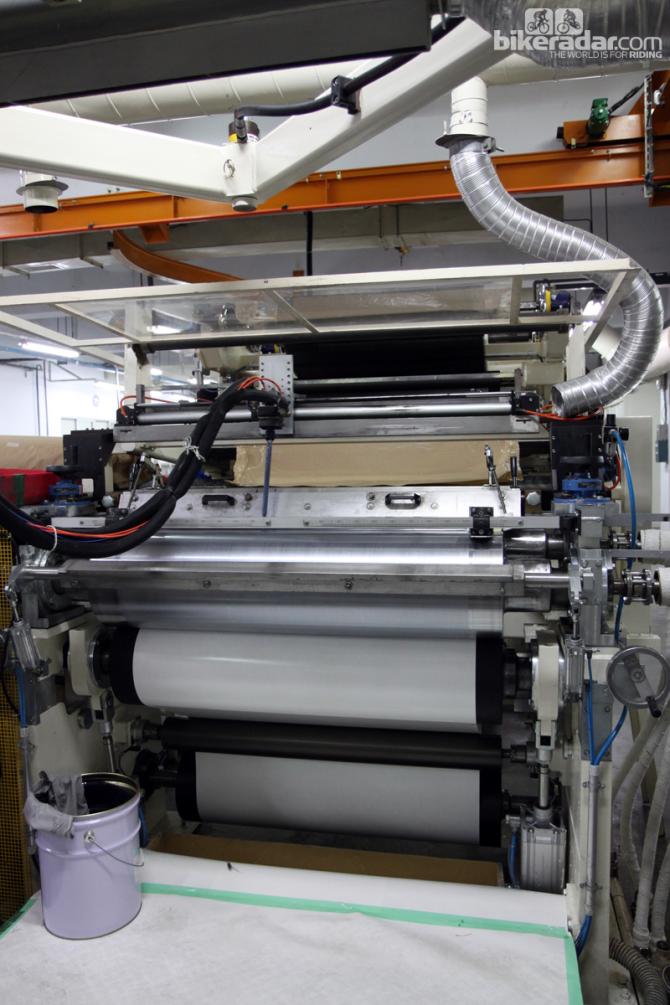
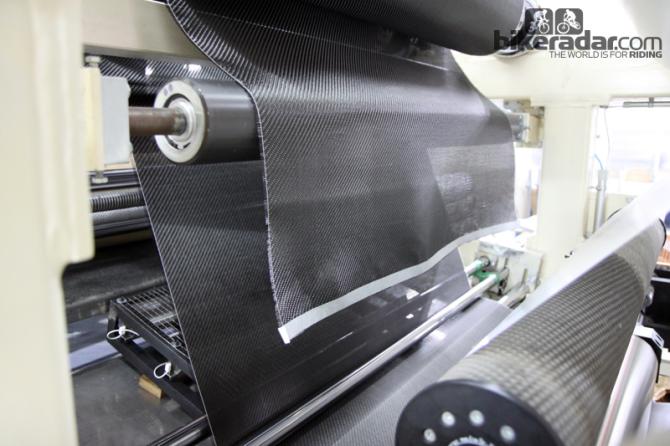
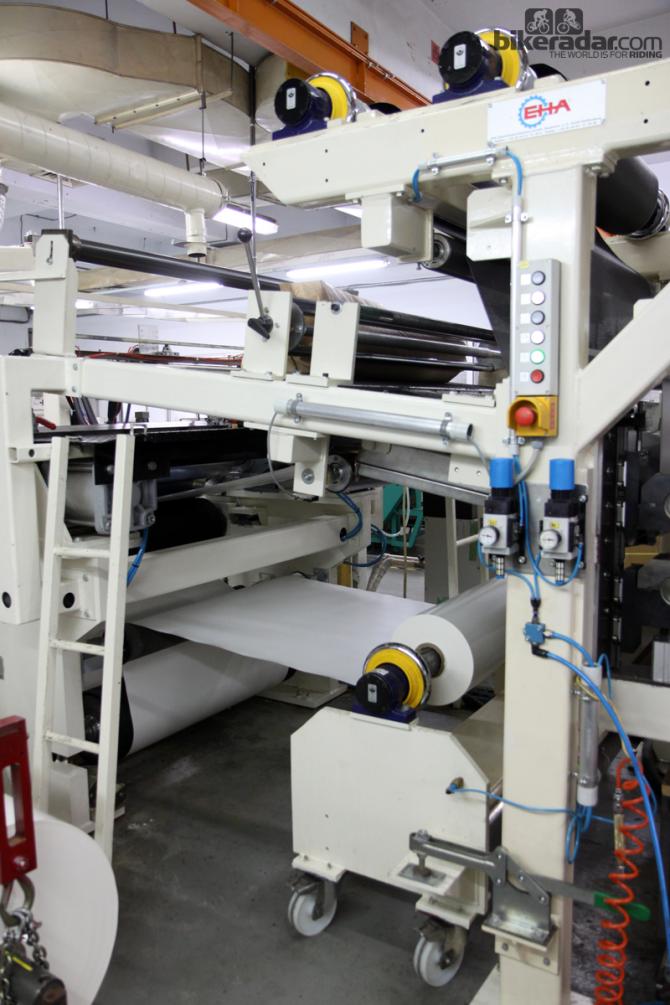
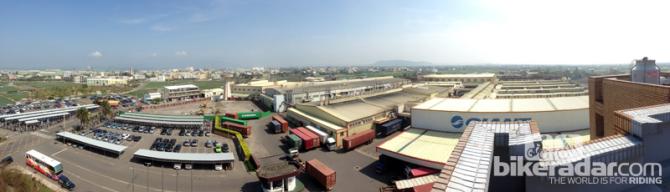
This article first appeared on BikeRadar.
Giant Bicycles truly lives up to its namesake as the undeniable 800lb gorilla of the bicycle industry. In 2012, the company generated US$1.8 billion (billion!) in annual revenue globally, both under its own label and as a builder for other brands. All of its carbon fiber and premium aluminum frames are manufactured in a sprawling facility in Taichung, Taiwan and BikeRadar brings you an in-depth, all-access pass inside.
Founded in 1972 by current company chairman King Liu, Giant first started as a contract manufacturer and things weren't looking too rosy from the outset. That year, Giant produced just 3,800 bicycles. That's all changed now, however, thanks to a hard-earned reputation for consistently delivering high build quality at reasonable prices – first in steel for Schwinn back in its heyday, then aluminum and now carbon fiber.
Today, Giant now builds more than 6.3 million bikes worldwide annually – a number equivalent to roughly half of all adult bikes sold in the United States each year.
One of the biggest keys to Giant's financial success has been its long-standing decision to integrate as many parts of the manufacturing process under its own roof. According to Giant CEO Tony Lo, this not only helps to ensure quality but it also decreases long-term costs – after all, fewer outside steps means fewer markups along the way and fewer questions about whether something was done correctly.
For example, Giant doesn't just weld its own aluminum frames; it also smelts its own alloys and forms its own aluminum tubing. And for carbon frames, Giant likewise isn't merely content to take delivery of pre-preg carbon fiber sheets that were manufactured by a third party. Save for creating the fibers themselves, Giant is unique among large manufacturers in that it controls the entire process every step of the way afterward.
For part one of this four-part series, we'll take a look at how the manufacturing juggernaut turns that raw fiber into usable materials.
Get The Leadout Newsletter
The latest race content, interviews, features, reviews and expert buying guides, direct to your inbox!
From Fiber To Fabric
Carbon fiber arrives at the Giant factory in surprisingly small spools. Multiple types of fibers are used, too, varying in characteristics like modulus (or stiffness) and tow (how many fibers are bundled together per strip).
From here, the fibers are fed into what's best described as a huge, industrial loom that lays them out in even layers. Giant makes all of its unidirectional fabrics in-house but woven cloth – the mostly cosmetic layer that many people imagine when they think of carbon fiber – is purchased pre-made. Either way, all of that carbon fiber starts out dry and has to be impregnated with resin. Exactly how that happens has up until now been an extremely closely guarded secret but we were given exclusive access to view the process ourselves – and more importantly, document it.
Giant stores its custom two-part epoxy resins in separate containers that are combined only when needed in a special mixing applicator. The carbon fiber sheets are sandwiched in between enormous stainless steel rollers (picture a newspaper printing press) and that mixing applicator then applies the blended resins to one side of the sheet in a back-and-forth pattern. As the sheet is squeezed through, the rollers not only force the resin in between the fibers but they also guarantee a uniform distribution throughout the sheet.
Just after the sheet passes through the rollers, backing paper is applied to both sides to keep the sheet from sticking to anything and then it's all rolled up on giant tubes.
This process only works for woven and unidirectional sheets, however. Bicycle frames also require layered orientations, too, and these have to be made in an additional step.
Workers then remove the backing paper from one side of the sheet and overlap the layers by hand. When all is said and done, what's left is a two-layered pre-preg sheet with fibres that are now angled relative to each other – and it all still fits on the same roll as before to facilitate storage.
From there, it's off to the freezer where the pre-preg materials are stored until they're needed.
In part two of this series, we'll show you how this carbon fiber is transformed into complete frames. Trust us – you won't want to miss it.