Talking Dutch: Koga Miyata factory visit
While in Holland for the Rotterdam Six, Ben Atkins paid a visit to Dutch cycle builders Koga-Miyata...
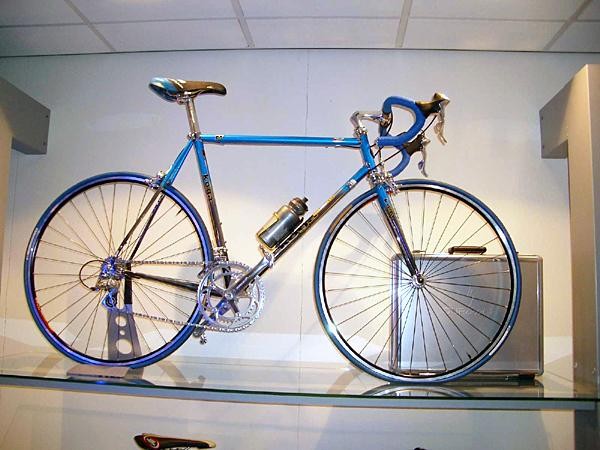
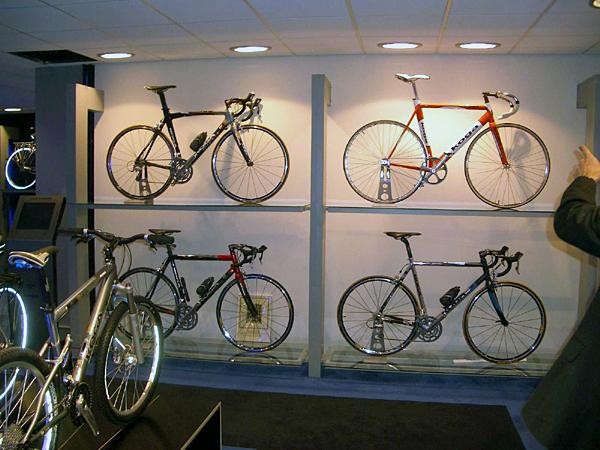
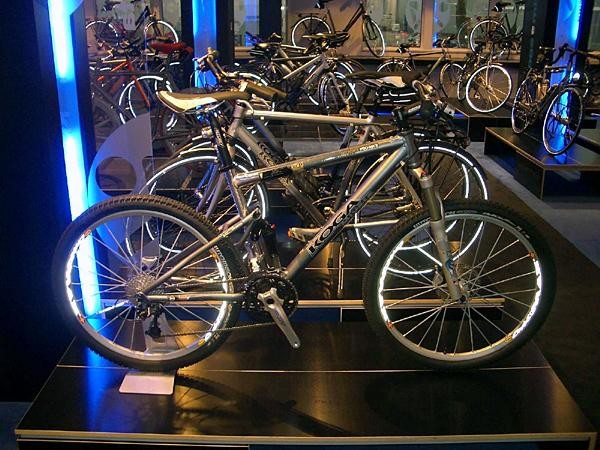
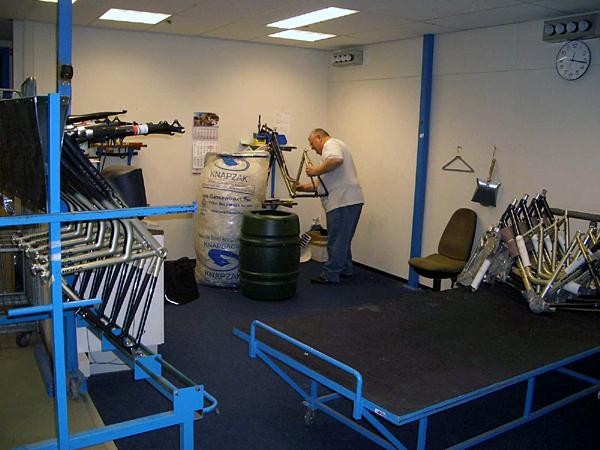
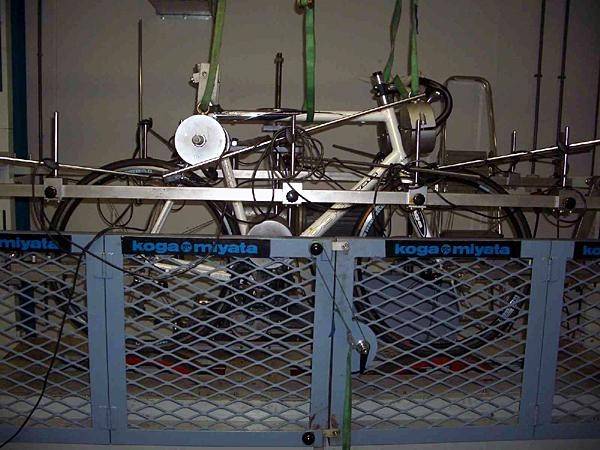
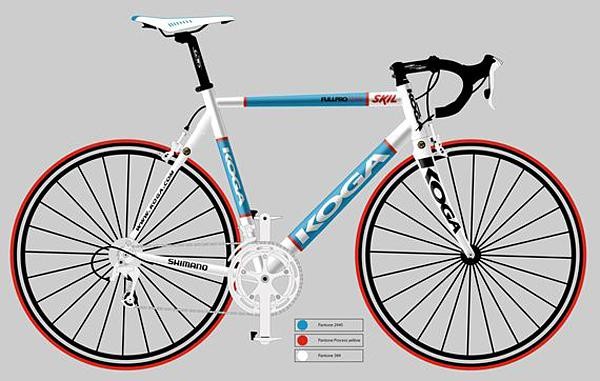
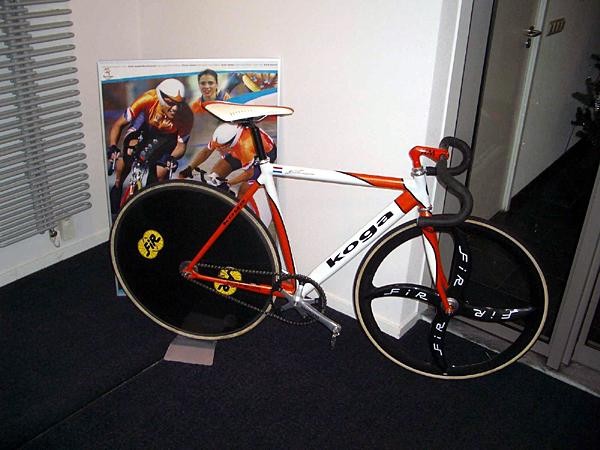
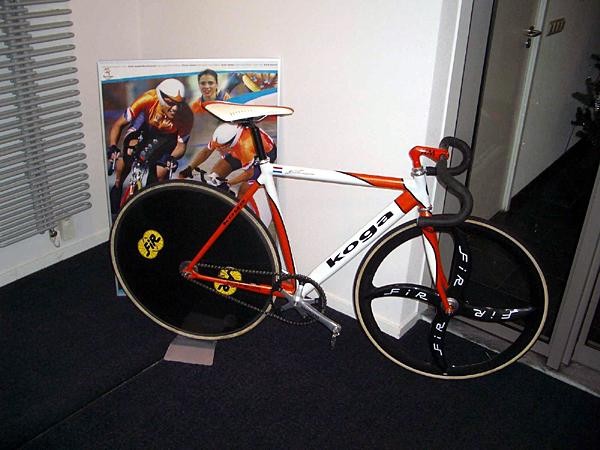
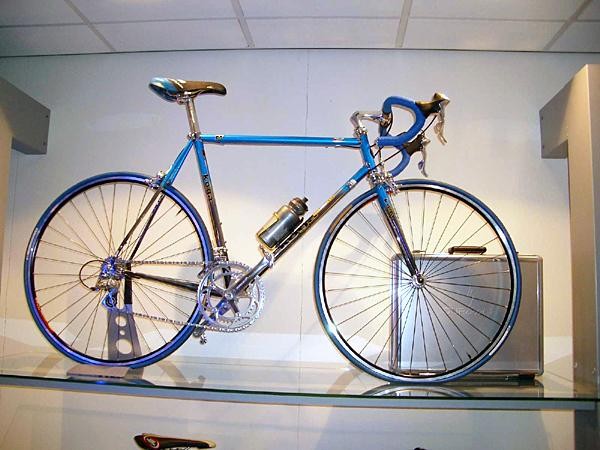
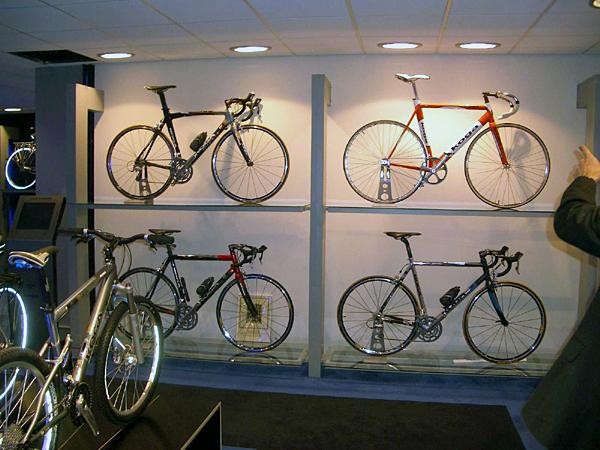
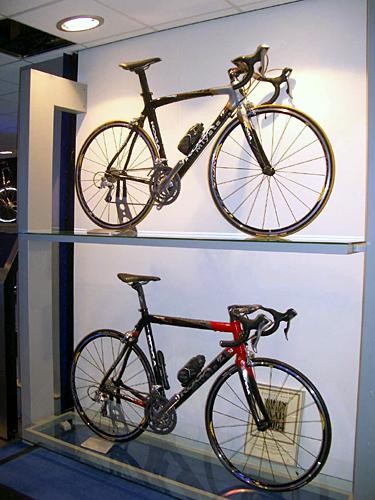
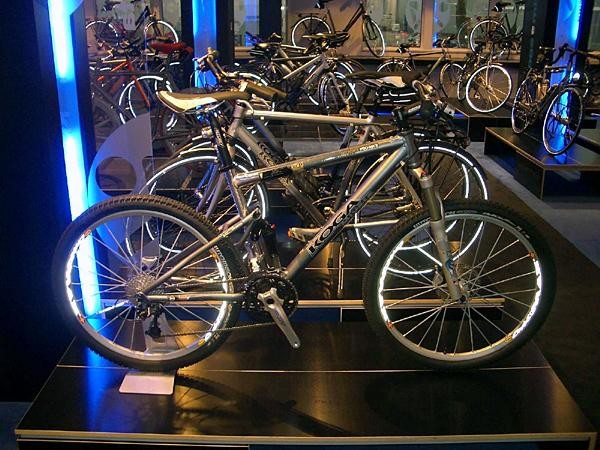
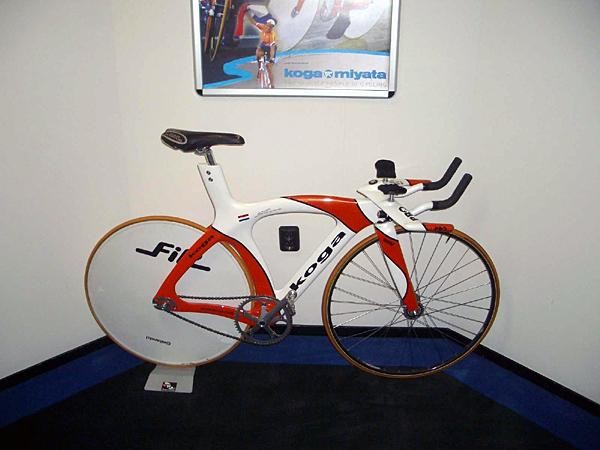
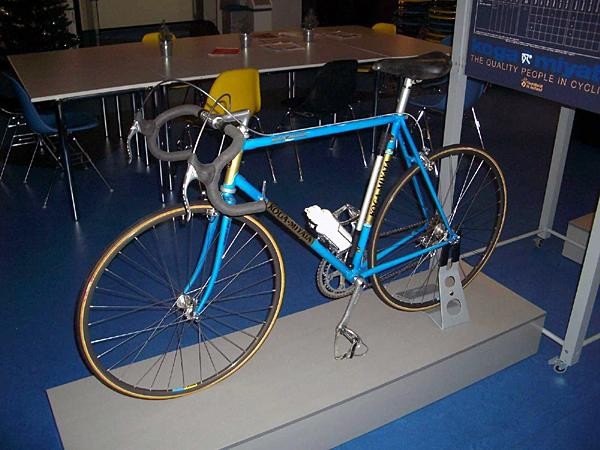
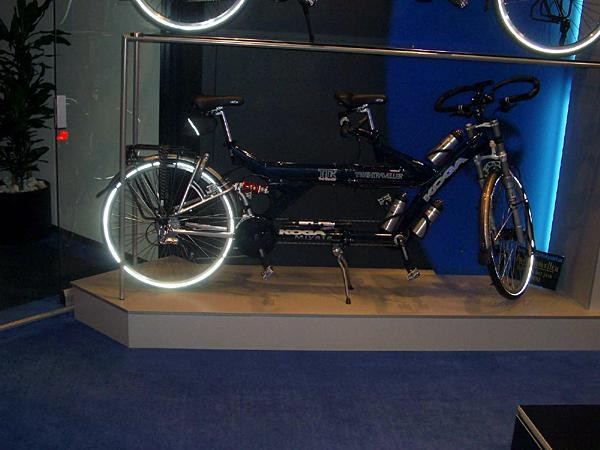
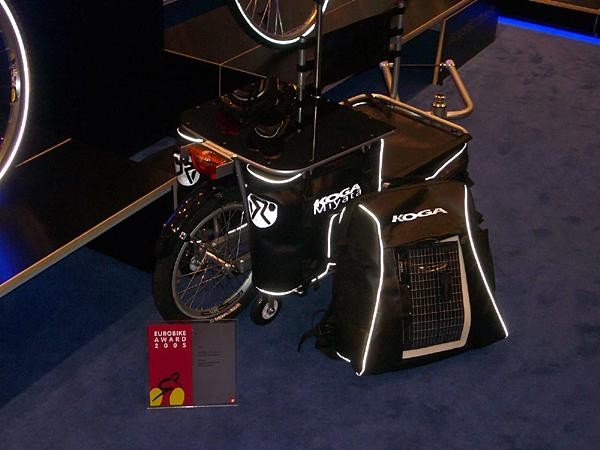
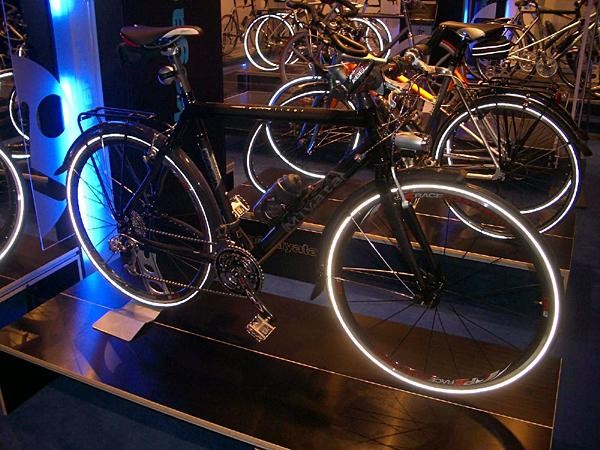
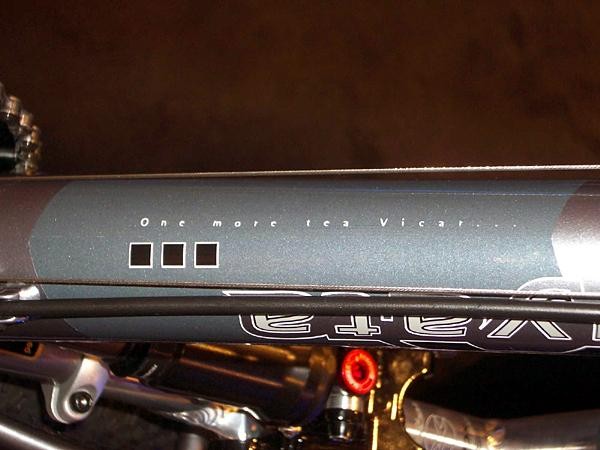
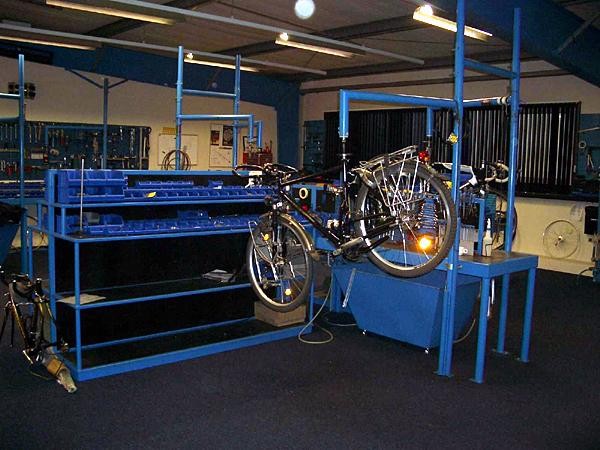
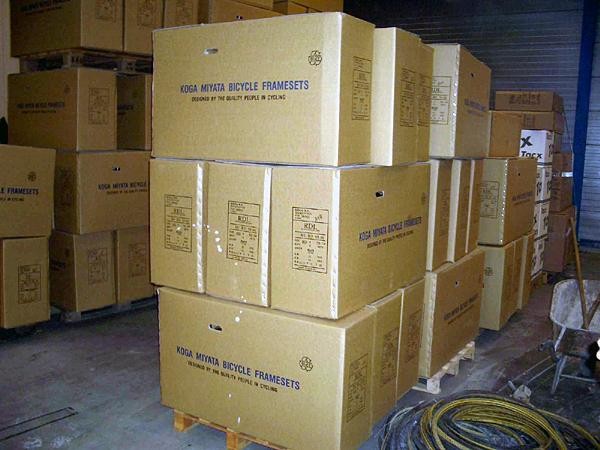
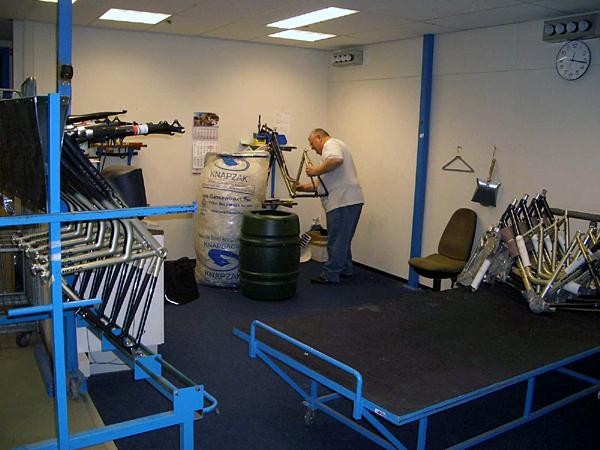
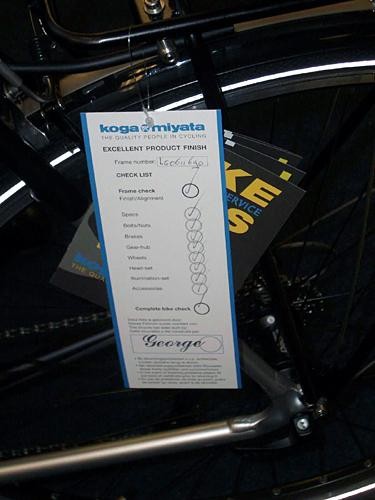
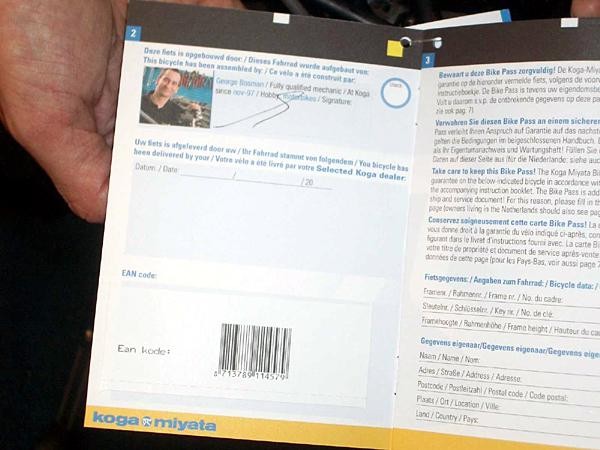
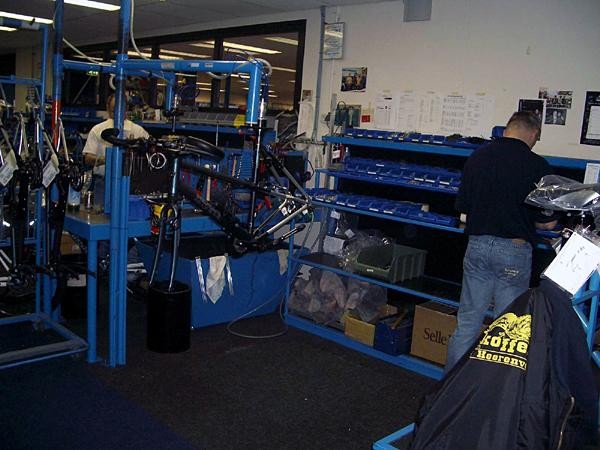
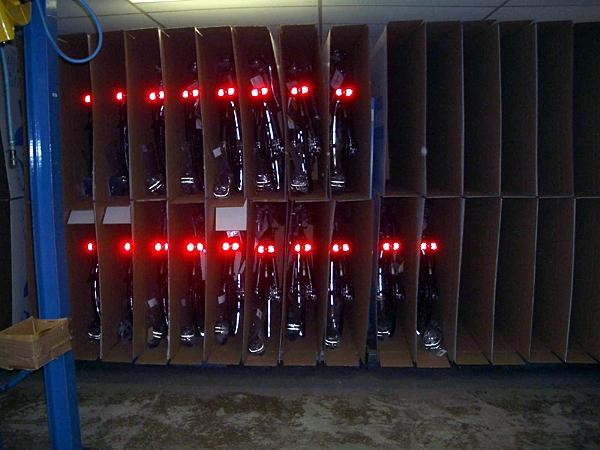
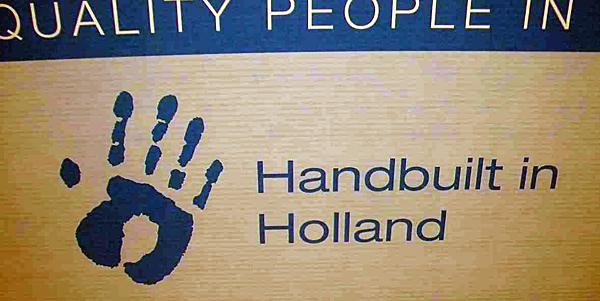
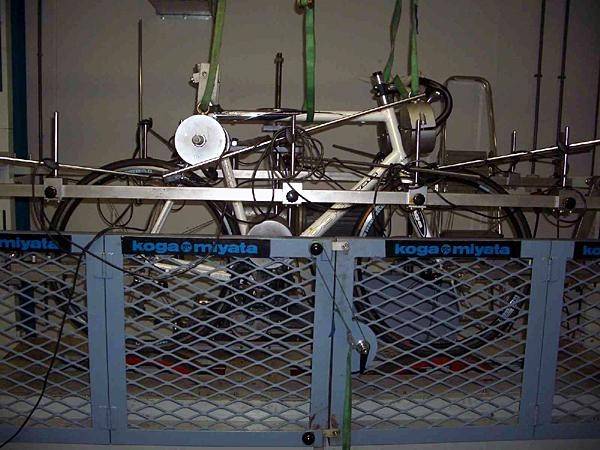
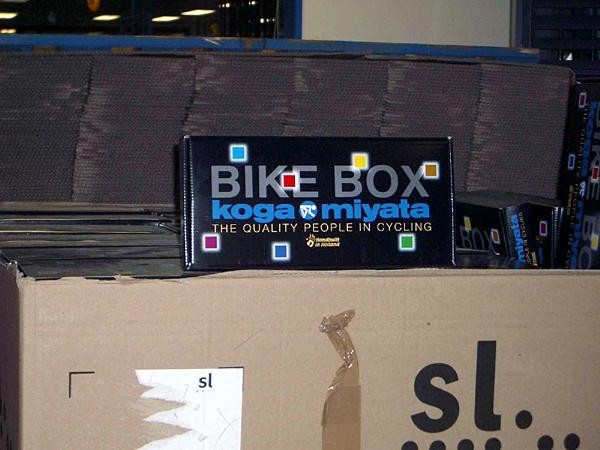
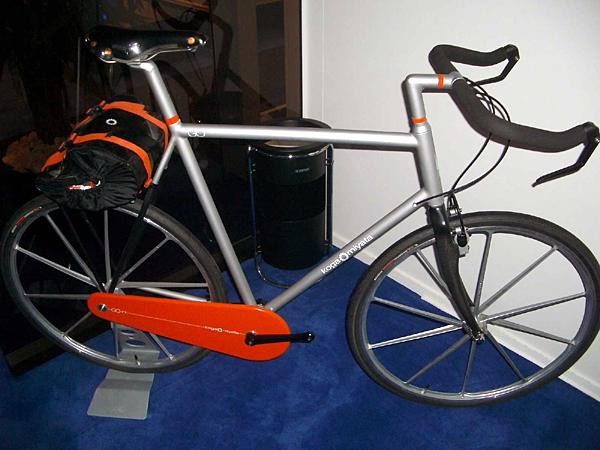
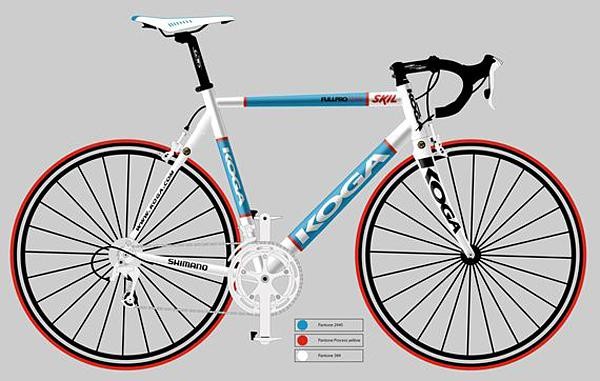
Tech feature - January 13, 2006
While in Holland for the Rotterdam Six, Ben Atkins paid a visit to Dutch cycle builders Koga-Miyata at Heerenveen, in the north-eastern region of Fresia, to talk about their plans for 2006.
The biggest news from a sporting perspective has been the announcement that Koga-Miyata will be the bike sponsor for the new Skil-Shimano team for the coming season. This will be Koga's first entry into the top echelon of the men's sport (albeit the European Continental Tour) since their sponsorship of Peter Van Petegem's Farm Frites team of 1999. Koga are also proud to remain the bike sponsor of the Dutch women's AA-drink team, featuring Kate and Natalie Bates and Sara Carrigan.
Unfortunately, neither the Skil-Shimano or AA Drink team frames had been delivered for me to see, but I was able to have a good tour of the factory and see the mechanics in action, in the preparation of bikes the Koga way.
The first thing you are reminded of on entering the front door of Koga-Miyata, is their long association with recently retired Dutch legend Leontien Zijlaard Van Moorsel. One of her track bikes with Koga-Miyata livery adorns the entrance complete with a huge poster featuring her Sydney triumphs. Leontien is still heavily involved with Koga and Dutch cycling - her husband Michael Zijlaard manages the AA-Drink team, as well as being one of those responsible for the revival of the Rotterdam Six.
The Koga showroom features almost their entire range of road, mountain, trekking and city bikes. The FullPro road range of Monocoque, Carbolite and Scandium offer a number of choices to elite riders (and those of us wannabes) depending on the terrain. The Monocoque with its aero tubing is aimed at either time trialling or fast road courses; the Carbolite is aimed squarely at climbers; and the Scandium at those looking for light weight and also stiffness. The FullPro Track, in its unmistakeable orange and white Dutch KNWU livery, is made from a mixture of scandium and aluminium tubes, and when built up with Dura-Ace track components and titanium rims, it looks - to use a horrible cliché - fast standing still!
Koga make bikes for all occasions and are incredibly proud of their trekking bikes, which are tested on all terrains, all over the world. By far the wildest of these is the TwinTraveller, a folding, full-suspension tandem! The folding part is not just a gimmick, but deliberately there to make things easier when travelling, transporting and storing the tandem. There is even a nice convenient mechanism for storing the connecting chain when folding; as with all things Koga, attention to detail is evident everywhere.
Get The Leadout Newsletter
The latest race content, interviews, features, reviews and expert buying guides, direct to your inbox!
One of my favourite things to be found in the Koga showroom is the "Chela" trailer. Tibetan for Disciple, the Chela will follow you everywhere (geddit?), and was reputedly designed by Koga R&D man Mark Dorlandt while he was riding across Australia with another brand of trailer - as he rode he listed the faults of his trailer, and listed what he'd like to see in it. The result of this design in the field was the Chela, complete with built in collapsible chair and tabletop, and removable day-sack featuring a solar panel for charging your GPS or phone.
The corridors of Koga have more reminders of racing success, including the track bike that Leontien Zijlaard Van Moorsel rode to gold in the 3000m individual pursuit at the Sydney 2000 Olympics (branded Koga-Miyata but made by Bike Technologies in Melbourne, Australia), and in the canteen, the revolutionarily-light bike ridden to victory at Alpe d'Huez by Peter Winnen in 1981. Unfortunately, the research and development departments are off limits to all but a few Koga staff - and certainly to any inquisitive journalists! - as they have some pretty secret projects in the pipeline, including what they describe as something special for the Dutch trackies in Beijing...
Downstairs on the ground floor is where the action is; the first place I was shown was the mechanics' school. All Koga mechanics have to undergo a two-year training course here before they're qualified to build bikes. The course not only teaches assembly and maintenance but also such things as the different characteristics of frame materials and different types of components. Koga were unable to find a recognisable qualification so they created their own.
Koga don't make their frames in Holland - they are made in Taiwan by a subsidiary of the Japanese Miyata company. This has always been the case, and is apparently not due to cost, the company claims, as they have been doing things this way ever since the days when it was more expensive to do so. Frames are delivered in huge consignments, boxed together - but well padded to prevent damage and scratching - and stored in the warehouse until they are ready to be assembled.
The mechanics were working on a batch of city bikes during my visit - it would have been nice to see some race bikes being built, but all Koga bikes are built in the same meticulous way. The working area is all carpeted to keep the room warm and comfortable for the workforce, as well as to prevent damage in case any parts are dropped. Each frame is carefully checked for scratches, damages and imperfections, as well as being measured to check that it conforms to the proper geometry before any assembly takes place. If a frame doesn't meet the required standard, it is returned to the factory in Taiwan.
Once assembled, each bike is given a certificate featuring the picture and signature of the mechanic who built it before being checked over by a supervisor. Koga do this because they feel that when you buy a Koga (warning - another cliché coming!), you are joining their 'family'. Their after-sales support lasts as long as the bike, one of the reasons that they don't come cheap! Once the supervisor gives the all clear, it is boxed and ready to be sent to a dealer. All the dealer has to do is straighten the bars and fit the pedals and it's ready to roll.
The last thing to see before leaving the factory was the "torture chamber", the test rig where frames are put through their paces and flex and stress is measured. The bike on the rig when I called by was doing 200km of simulated cobbles - a must for any Skil-Shimano or AA-Drink bike if success the northern classics is to be achieved this year.