Sea Otter 2011: Praxis
New brand offers stunning Turn crank prototype and forged chainrings
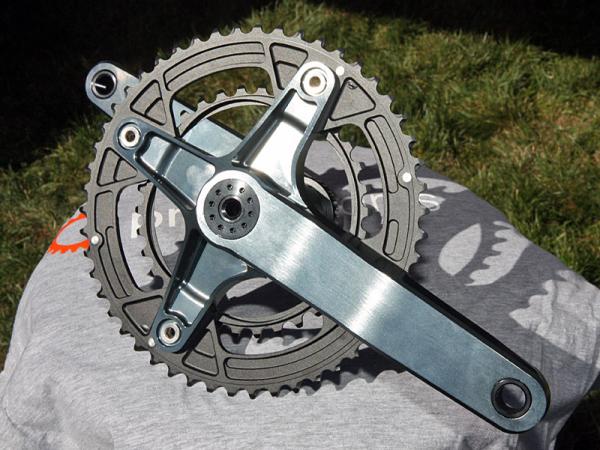
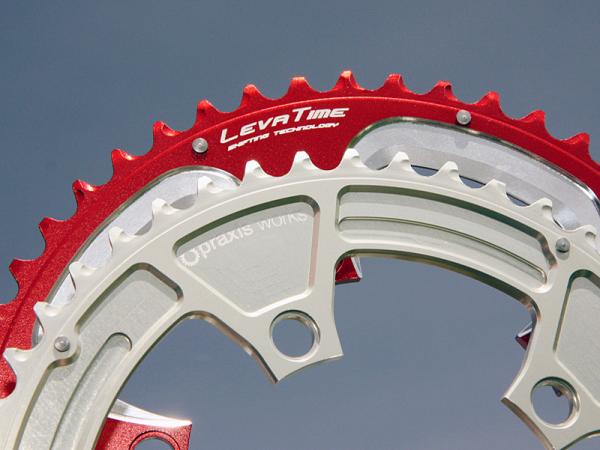
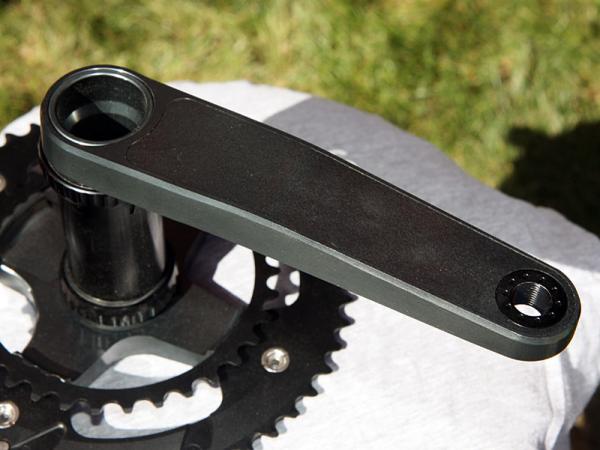
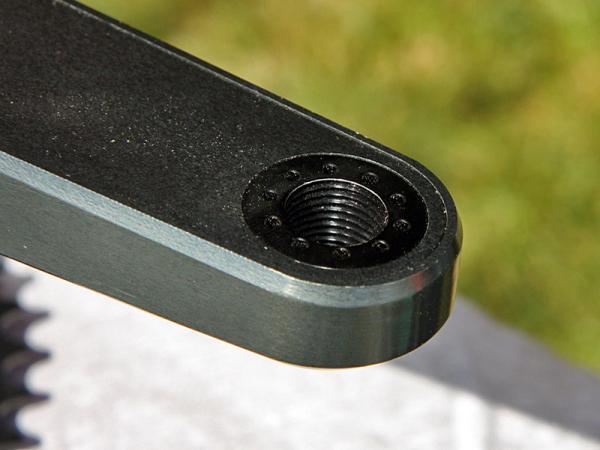
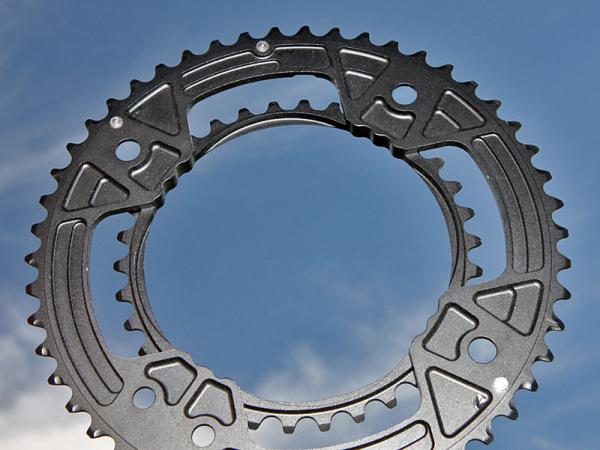
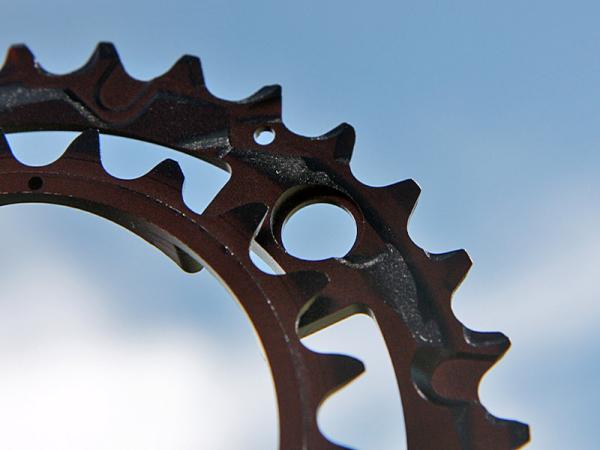
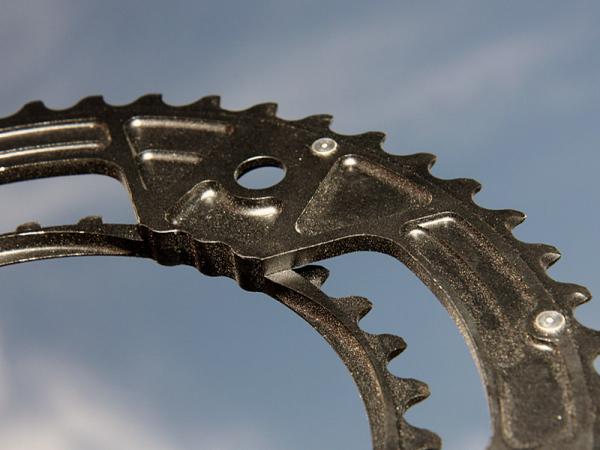
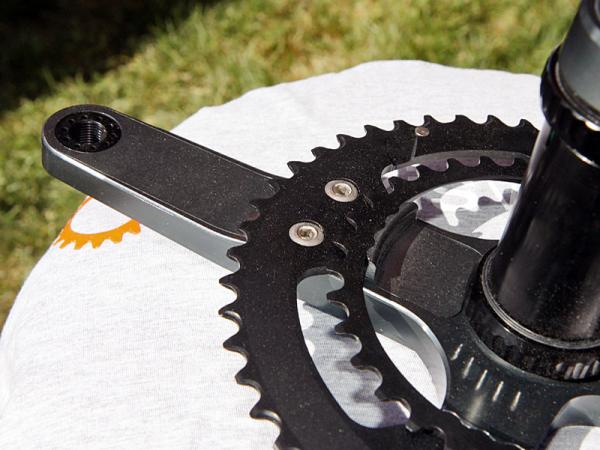
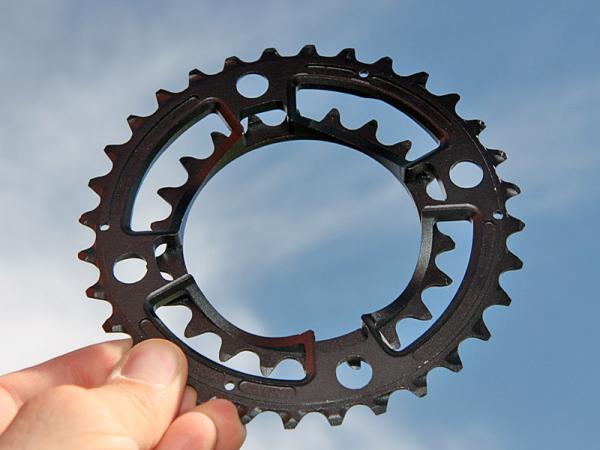
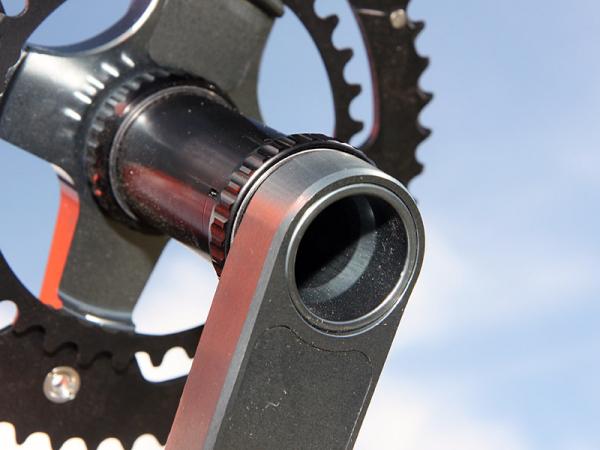
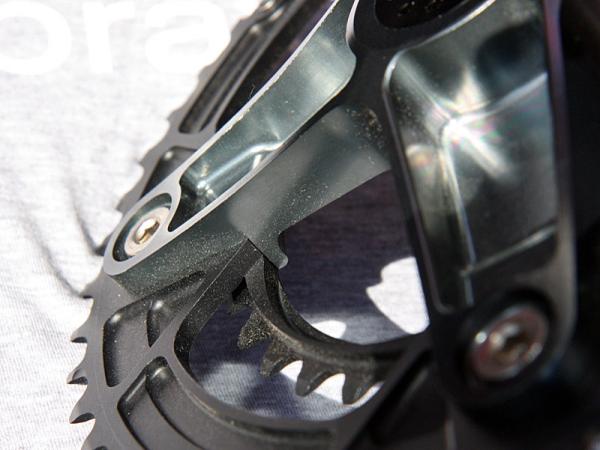
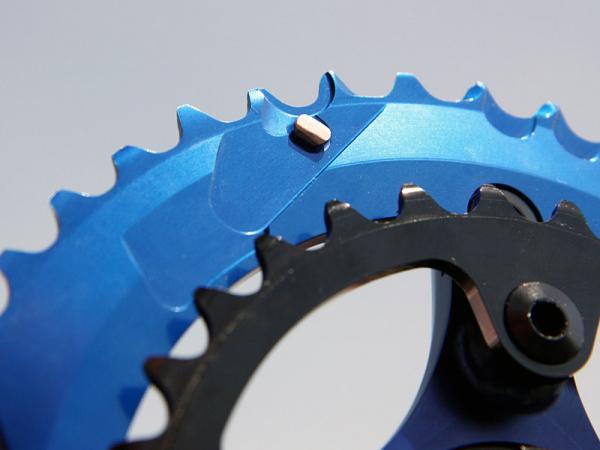
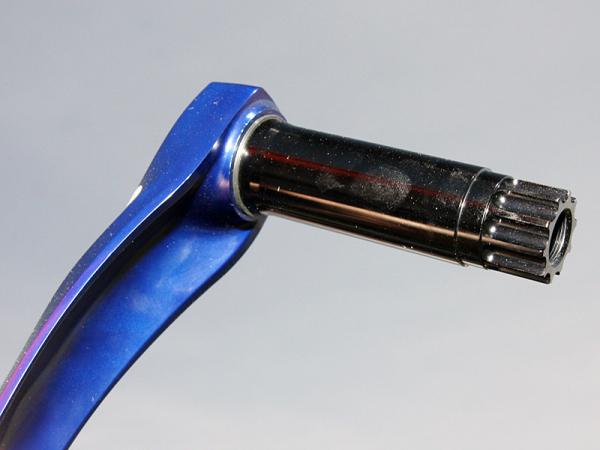
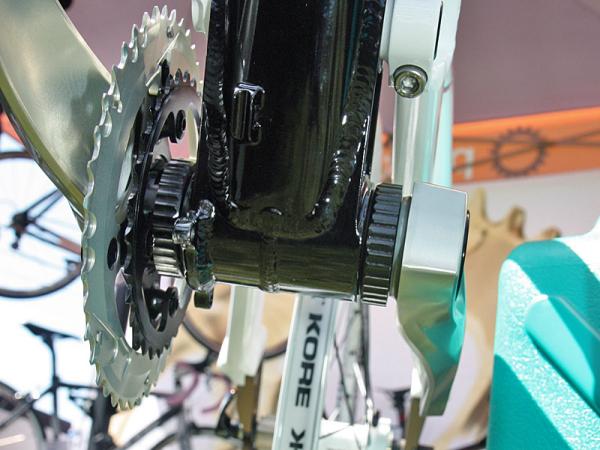
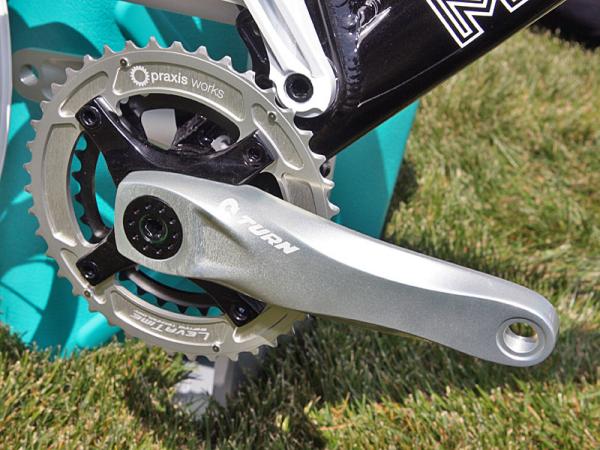
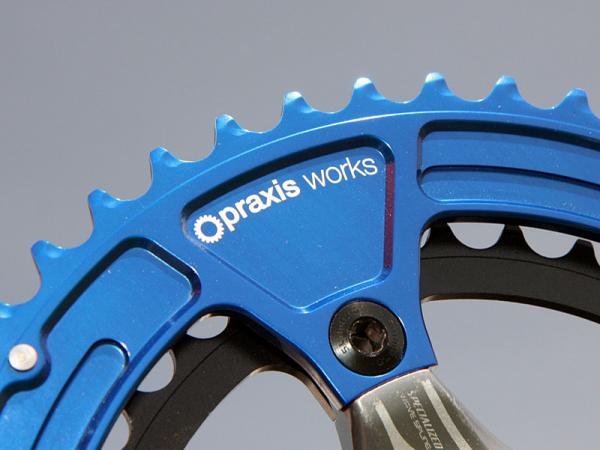
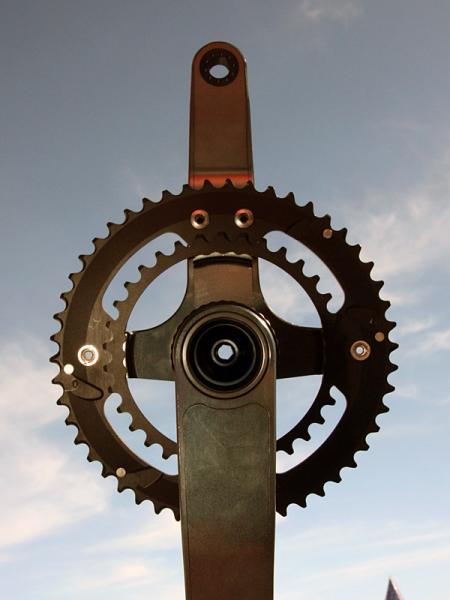
Haven't heard of Praxis yet? Industry insiders are already well acquainted with the behind-the-scenes forging capabilities of the company's Dragon Technology sister company but the company has recently decided to finally emerge from the shadows and head into the aftermarket. Chances are you'll see its chainrings in stores shortly, especially given the hole in the market left by the sudden departure of Race Face.
Unlike many other aftermarket chainrings that are either stamped or machined, though, Praxis chainrings are fully forged from 7050-T6 alloys in machining only used for the chainring bolt holes, the inner ramps, and some weight-saving relief work. Just like Shimano rings, the teeth are exclusively formed using a giant hydraulic press so the shaping of each tooth is much more complex than machined ones for better shifting and the materials themselves are more resistant to wear, too.
Praxis says its "Liquid Ano" process produces especially deep colors. It's also noticeably slicker than usual, too. Photo: James Huang
Praxis director of marketing and sales Adam Haverstock also stresses that each Praxis ring's stainless steel shift pins, inner ramps, and individual tooth scallops are designed for specific chainring combinations.
Praxis will also offer its rings in optional "Liquid Ano" finishes, which differ from standard hard or color anodizing finishes in their visibly more lustrous hues and noticeably slicker surface finish.
Forging requires much higher up-front tooling costs than machining - each and every ring requires its own dies - but Haverstock says the performance advantage is worth it in the long run. We'll find out soon enough for ourselves, as we already have test rings in process. For now, stock offerings include standard and compact road plus both 2x10 and 3x10 mountain bike rings.
More than just chainrings - cranks, too
The latest race content, interviews, features, reviews and expert buying guides, direct to your inbox!
We'll have to wait a while longer for the company's stunning Turn all-aluminum forged-and-machined road crank, though, which was still in prototype form at Sea Otter but finished enough to get an idea of what it'll offer when it ultimately hits the market (hopefully) around this time next year.
Praxis provided a sneak peek at this prototype design for a super high-performance road crank. The forged-and-machined arms are fully hollow and the forged and machined chainrings are a single unit. Photo: James Huang
Praxis and Turn principal David Earle - whose resume includes stints as engineering director at Santa Cruz, senior design engineer at Specialized, and engineering manager at Bontrager - says stiffness and lightweight were the primary goals here and the work-in-progress certainly looks the part. The arms are massive rectangular structures, each spider arm utilizes a ridiculously stout C-section profile, the proprietary chainrings are formed as a single unit, and the entire thing rotates on Praxis's enormous 35mm-diameter M35 bottom bracket spindle with external bearings, which plugs into standard BB30 and PressFit 30 shells.
Praxis uses a giant 35mm spindle for its prototype Turn road crank design. Photo: James Huang
Those inflated dimensions are obvious approaches to achieving high stiffness figures but Earle says that joint testing done in cooperation with EECycleworks' Craig Edwards revealed another surprising source of flex under high loads: conventional chainring bolts.
"The ring actually spins around that point, which actually allows rings to flop over," Earle said. "So if you can minimize the amount of spinning it does around that bolt, it makes the ring stiffer."
Earle has also opted for a proprietary one-piece double chainring, which again, is primarily forged with machining used only for secondary finish work. Combining the rings in one unit gave Earle more contact surface area to play with, too, so he added splines on the inner edges which interlock with the spider, thus firmly cementing each contact point in place and allowing no degrees of freedom, even when chainring deflection is taken into account.
Praxis plan to use a one-piece double chainring setup like this for their upcoming Turn road crank. Photo: James Huang
"Other than that, it's just making things big and hollow - the crankarm's big, the crankarm's hollow, the spindle is 35mm, bearings are outboard, and that's really about it," he said. "The crank is absolutely amazing. Six months ago, before I rode this crank, if anyone said, "This crank is super stiff", I would have been like, "You can't tell the difference." And we'd done a lot of testing that kind of proved that. But within three pedal strokes of riding this crank, I was like, holy shit, this is amazing."
Earle also claims that extensive testing of the company's M35 bottom bracket with other cranks has revealed no weaknesses but when his own Turn crank is inserted, the bottom bracket becomes the failure point in the industry-standard CEN test.
"All of the stress concentration totally changes because the crank isn't flexing."
Earle says it'll probably be a year before the crank is ready to sell and while he was alright with BikeRadar shooting photos of the prototype (Praxis had turned us down the day before), he did want to stress that this wasn't the final product. Earle says the finished crank will likely have bolted and bonded-on carbon fiber crankarm covers instead of the aluminum ones currently in use and the overall aesthetic will be a little more refined. The basic concept will carry through, though.
"There's only so much you can do with a hollow, square shape."
While weight wasn't necessarily the primary goal, the new crank is certainly still going to be pretty light. And there's no estimated price yet but it's a veritable certainty that it'll be very expensive.
"I would hope that we could break 700g for the whole crankset but that'd be a pretty trick setup," Earle said. "It won't be cheap."
Praxis's new Turn all-mountain crank uses a C-shaped cold forged aluminum arm and giant 35mm-diameter spindle that fits in a standard BB30 or PressFit 30 shell. Photo: James Huang
Praxis already has its burly Turn forged all-mountain crankset in production, however, and Mountain Cycle is already including it as original equipment. The giant C-shaped arms are attached to a two-ring spider - fitted with Praxis rings, of course - and it all spins on the company's M35 bottom bracket. Haverstock says aftermarket versions will be available soon.
This article originally appeared on BikeRadar.