Gallery: Sturdy Cycles' custom-made, titanium, 3D-printed time trial bike
The three-year project that just won best-in-show at the Bespoked handmade bike show
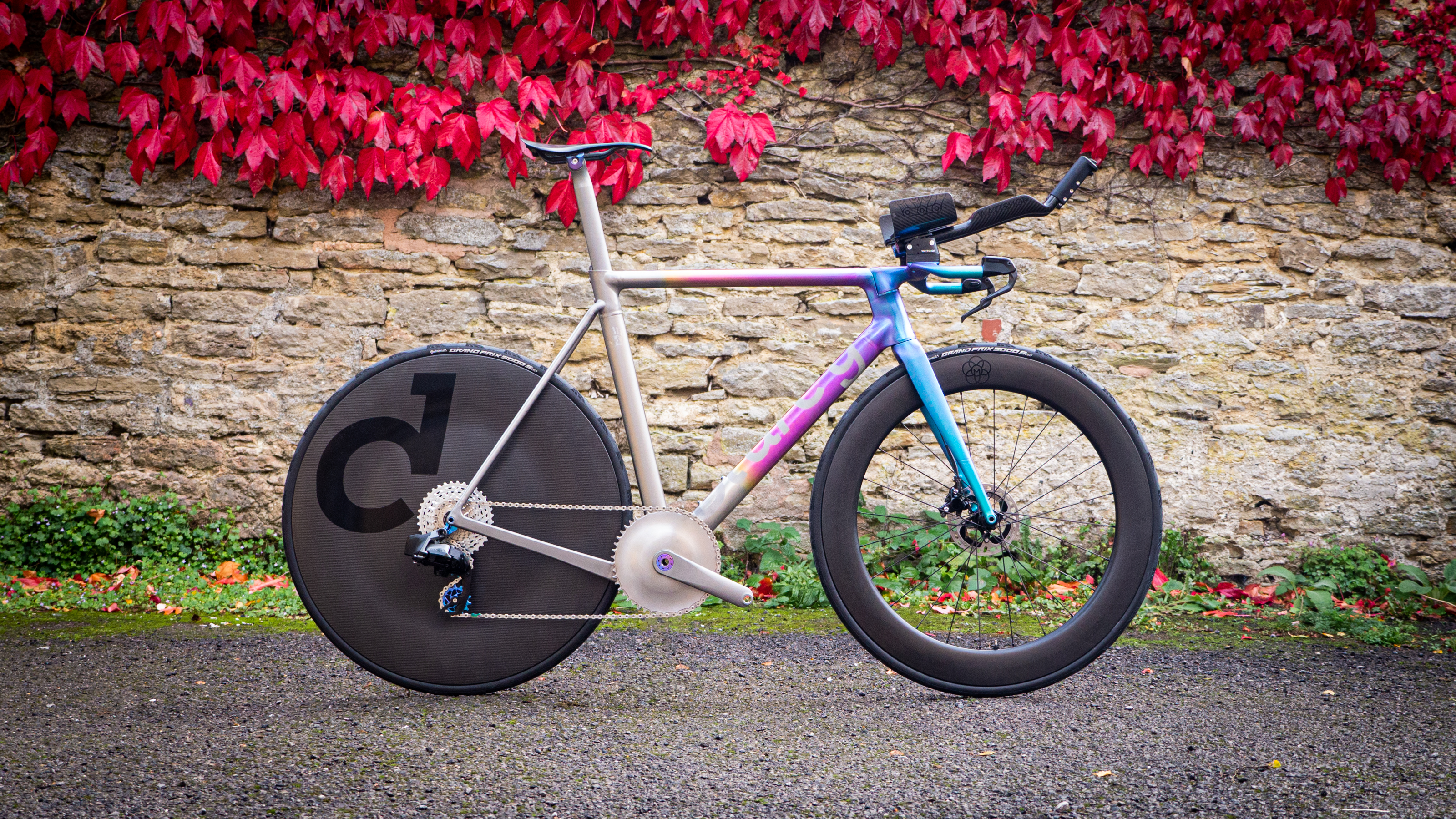
Tom Sturdy is a passionate cyclist with a background in aerospace engineering. Turning his hobby into a career he set up Sturdy Cycles, where he applies his skillset to the task of custom-building titanium bikes to order. His waiting list is months - sometimes years - long.
Based out of a small workshop in Frome, Somerset, Sturdy's latest creation is the product of three years of toil. It is called the Eimear, and it is a part-3D-printed time trial bike with ovalised titanium tubes, custom geometry, and dozens of custom-made titanium components, including a self-made chainset and base bar.
We got wind of Sturdy's latest project in the lead-up to Bespoked, the London-based show dedicated to handmade bikes, so paid the Sturdy workshop a visit the day before the show began. The Eimear subsequently won the award for Best In Show, proving we're not the only ones impressed by it.
All of the tubing of the frame has been optimised using CFD (Computational Fluid Dynamics) to find an aerodynamically efficient shape without losing stiffness and durability. Sturdy says he's yet to get it into the wind tunnel to find out exactly how fast it is, though. A complete bike, as shown, weighs in the region of 8kg.
Geometry-wise, the bike is built for Sturdy himself. He tells us it will be available for sale should anyone want to buy it, but that he used his own bike fit as the starting point so that if it weren't sold, he could use it for a few of his own local time trials. He explained the "huge risk" that a customer would have had to take, were they to commit to buying this first iteration of the bike.
Custom components
With regards to the components on the bike, it would probably be faster to list the ones that aren't made by Sturdy himself, such are their number. The chainset is his own, 3D printed with an aerodynamic titanium chainring set up as a single ring. This spins within his own bottom bracket, using angular contact bearings from California-based Enduro.
The seatpost is also his own, and clamps into place using a wedge that fills the void left behind the D-shape. The thru-axles, bottle cage mounting bolts, saddle clamp, derailleur hanger and pulley wheels are also his own, each standing out in their anodized blue-purple finish. Interestingly, besides the bottom bracket which uses a 10mm hex, all other adjustable parts are fitted with T25 Torx heads, because he "hates having to carry round a load of tools".
Get The Leadout Newsletter
The latest race content, interviews, features, reviews and expert buying guides, direct to your inbox!
The base bar is also made by Sturdy, and measures 36cm wide. Atop this, he's fitted a Wattshop Anemoi/Minimoi cockpit. Sturdy explained how he spent time trying to design his own cockpit system, and that given he valued adjustability, he didn't want something "like [Filippo] Ganna" whose cockpit is one-piece and fixed. In spending time designing the various spacers, he realised he was just creating something that Wattshop had already designed.
The wheels, meanwhile, are an unbranded set from a Chinese factory that Sturdy has had a long relationship with. The disc rear bears the 'd' Sturdy logo, while the 70mm front wheel bears the logo of his friend's new wheel brand, Manuka, which started up just a month or so ago.
It's all in the details
The longer you spend with the Eimear, the more you appreciate the attention to detail that's gone into making it. Whether it's the position and quality of the welding designed to reduce stresses, to the add-on components that make it pop, there are plenty of neat little surprises that have a knack for revealing themselves right at the moment you think you've finished taking photos.
For example, the end of each crank arm bears an imprint of the Sturdy logo, while the shape of a hand is etched into the down tube complete with an outline of the UK on its palm to denote that the bike was 'handmade in the UK'.
Elsewhere, there's a custom-printed ergonomic grip fitted to the end of each time trial extension, which is designed to house the wireless SRAM blips. Not fitted at the time of shooting, but added later were some grips to the base bar, which smoothed out the step down behind the SRAM hydraulic brake levers.
It's this attention to detail that keeps Sturdy busy and his customers returning. Ably assisted by Omar in the workshop, Sturdy explained that once frame parts and components were received, the build process could be complete in a matter of weeks. However, from the initial consultation - which typically happens online, since most of his customers are from abroad - to the final delivery could take six months (longer in recent years due to the pandemic), and "most of that time is the queue".
Scroll down to enjoy more photos of the Sturdy Eimear.
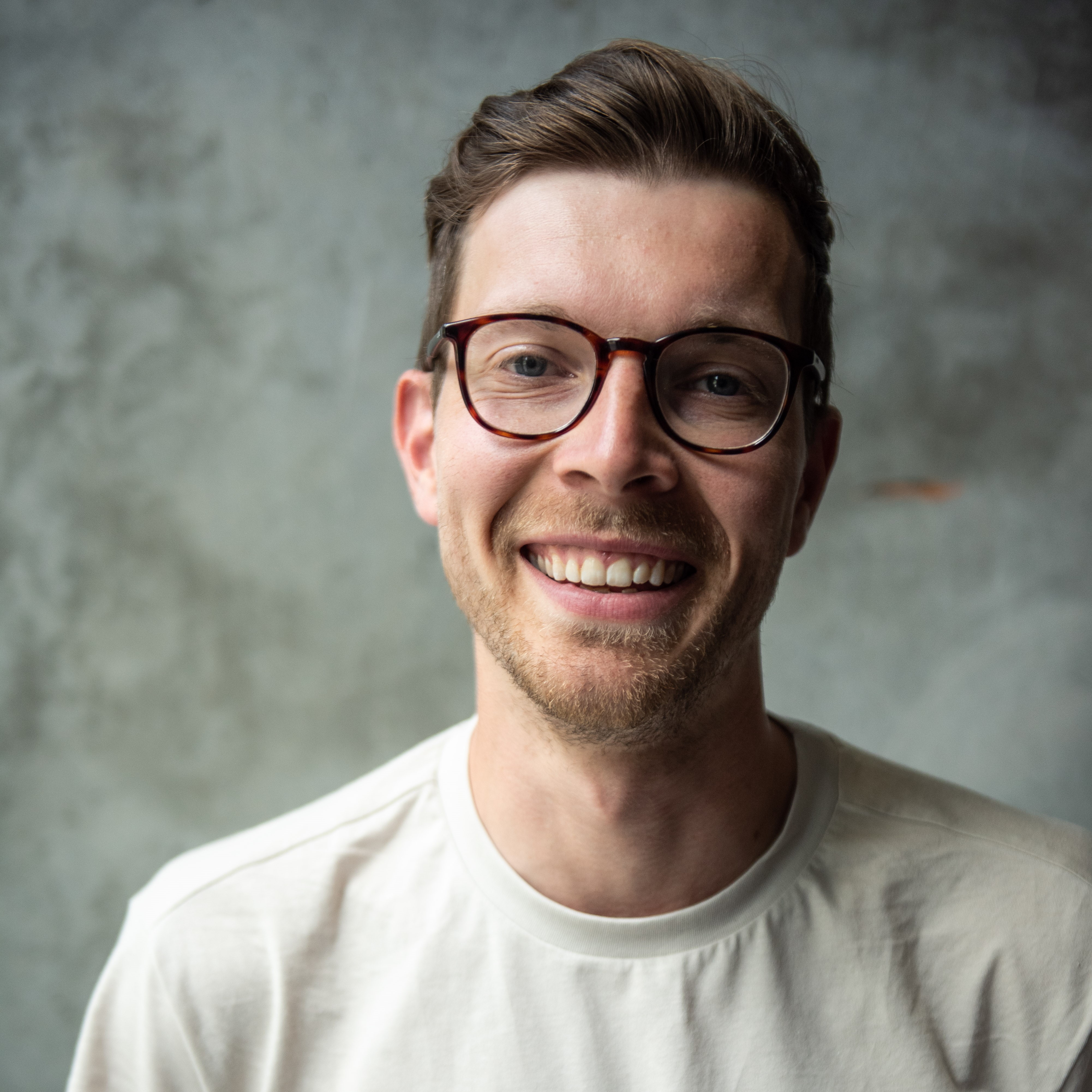
Josh is Associate Editor of Cyclingnews – leading our content on the best bikes, kit and the latest breaking tech stories from the pro peloton. He has been with us since the summer of 2019 and throughout that time he's covered everything from buyer's guides and deals to the latest tech news and reviews.
On the bike, Josh has been riding and racing for over 15 years. He started out racing cross country in his teens back when 26-inch wheels and triple chainsets were still mainstream, but he found favour in road racing in his early 20s, racing at a local and national level for Somerset-based Team Tor 2000. These days he rides indoors for convenience and fitness, and outdoors for fun on road, gravel, 'cross and cross-country bikes, the latter usually with his two dogs in tow.