BMC Racing Team: Behind the scenes at the service course
Cyclingnews visits team of Evans, Phinney, Hincapie and King
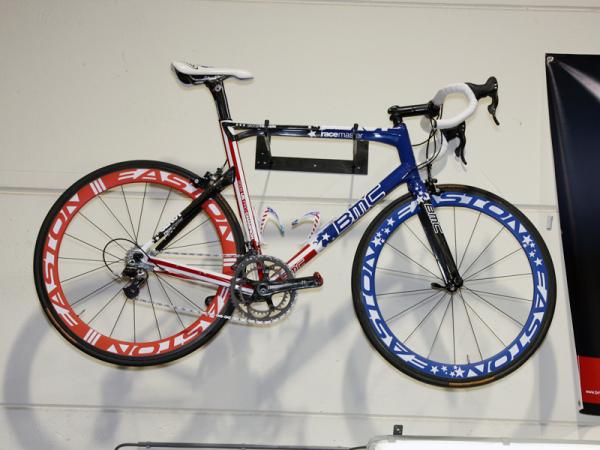
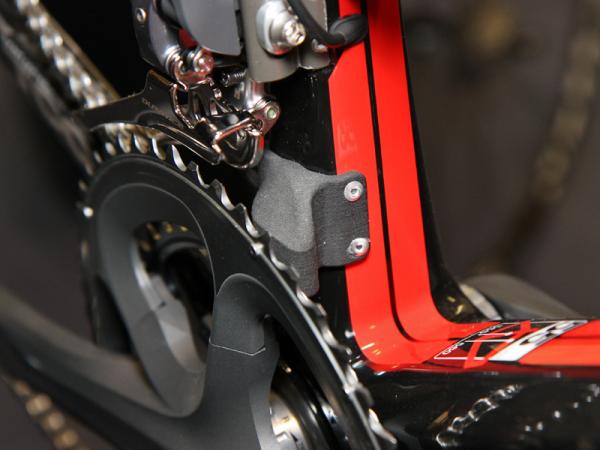
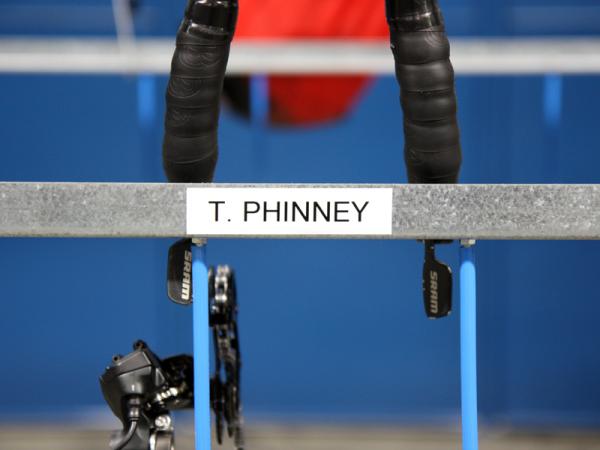
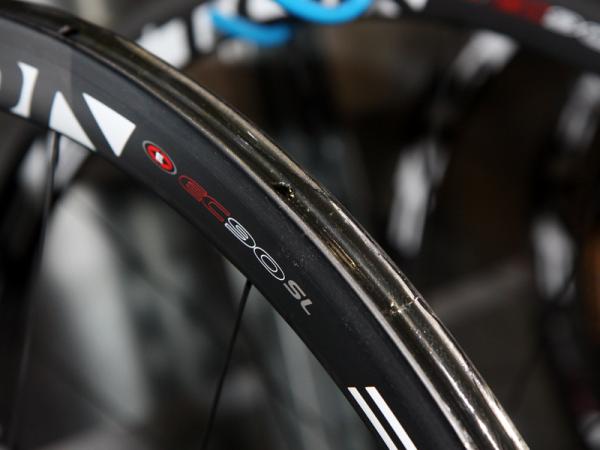
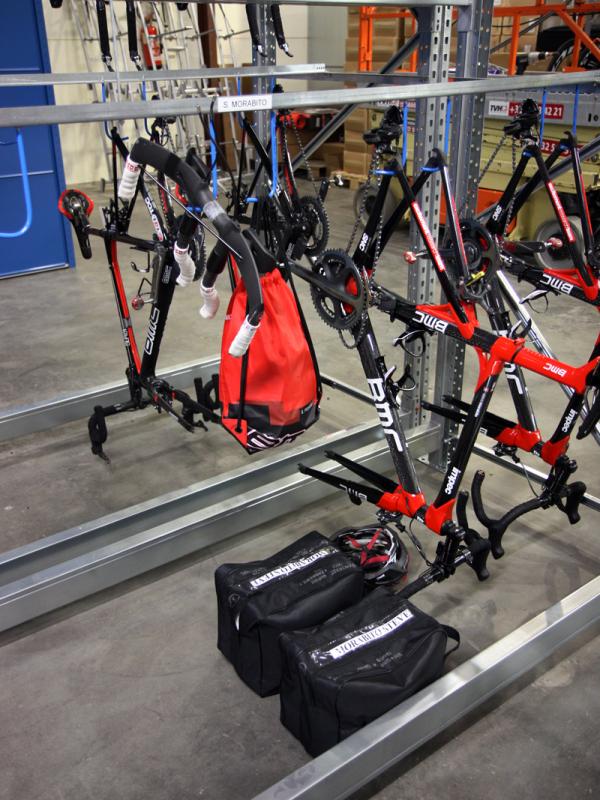
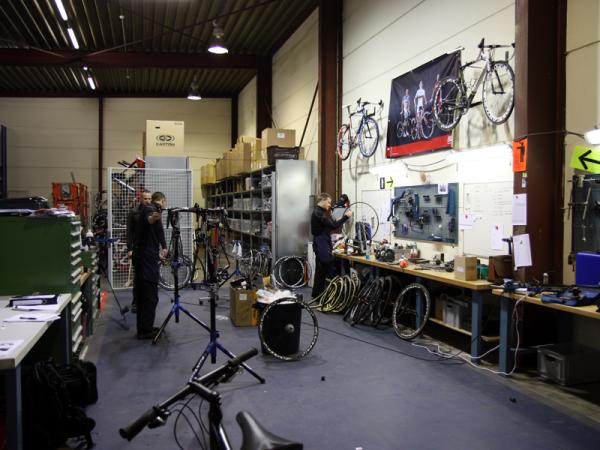
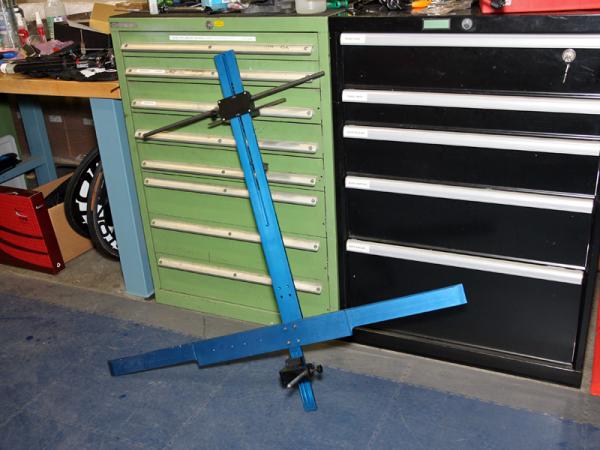
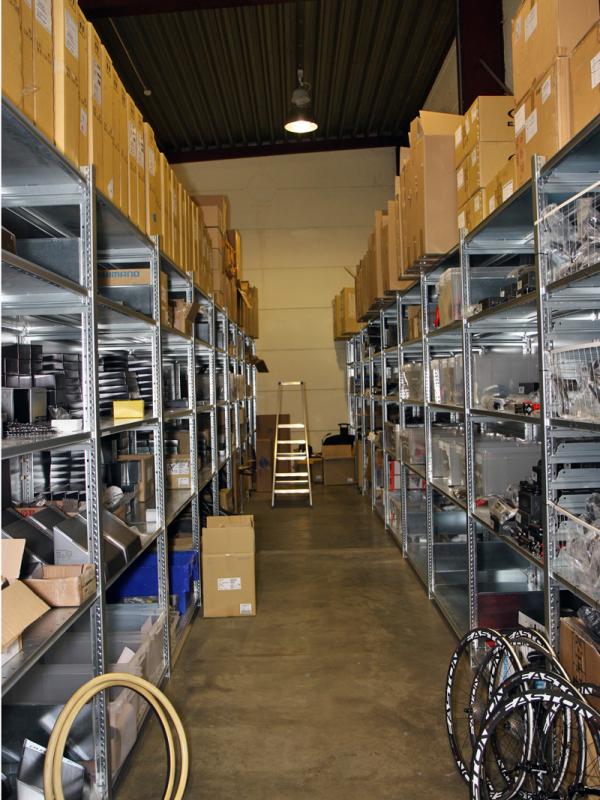
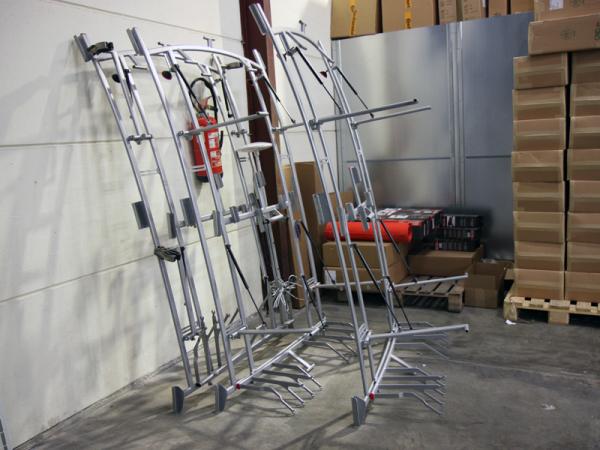
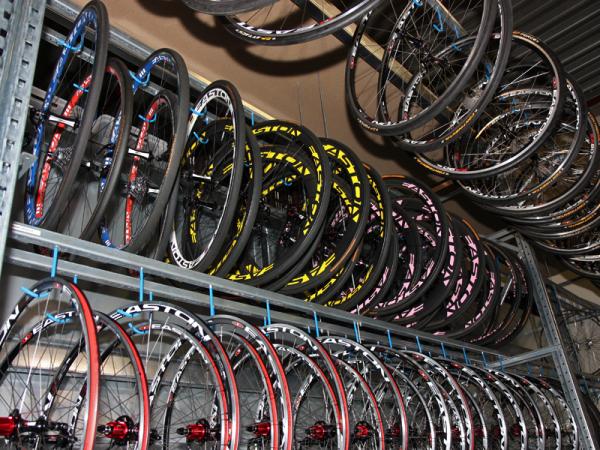
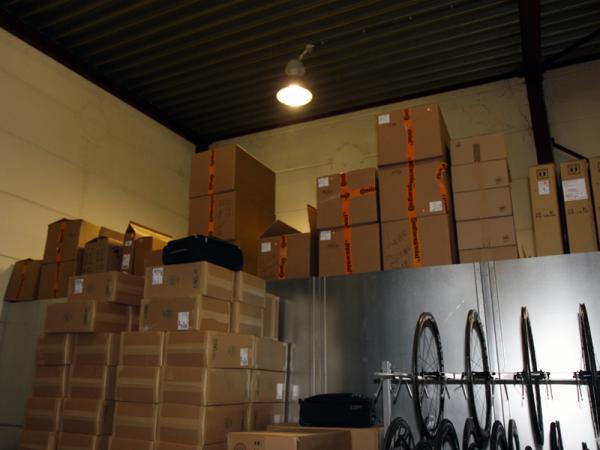
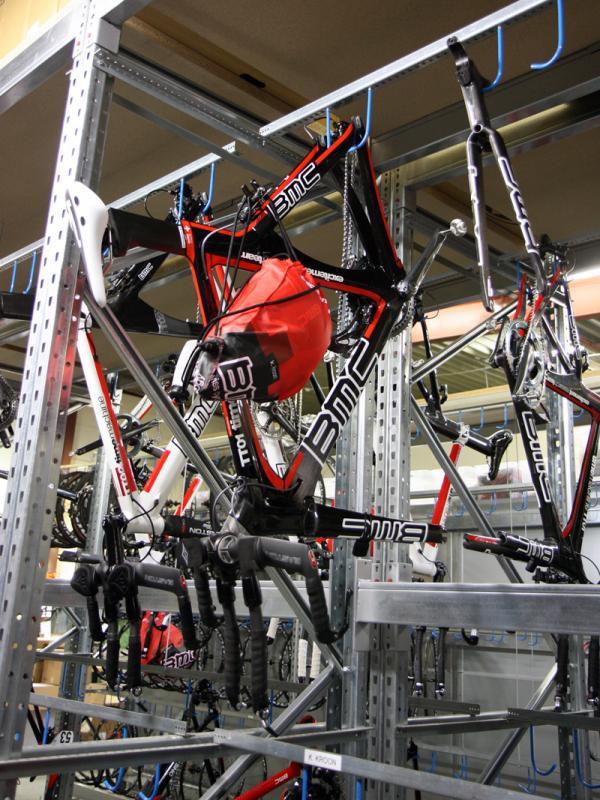
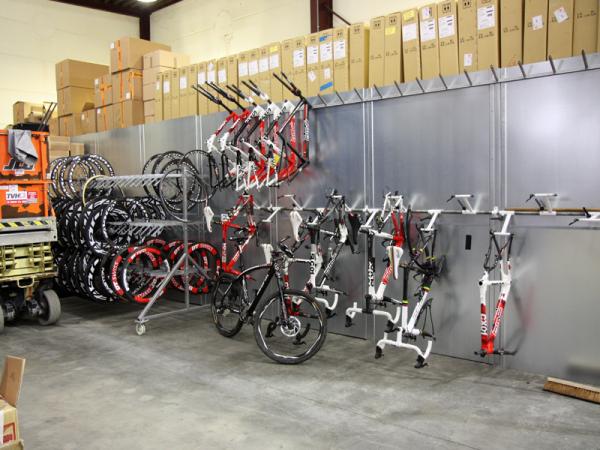
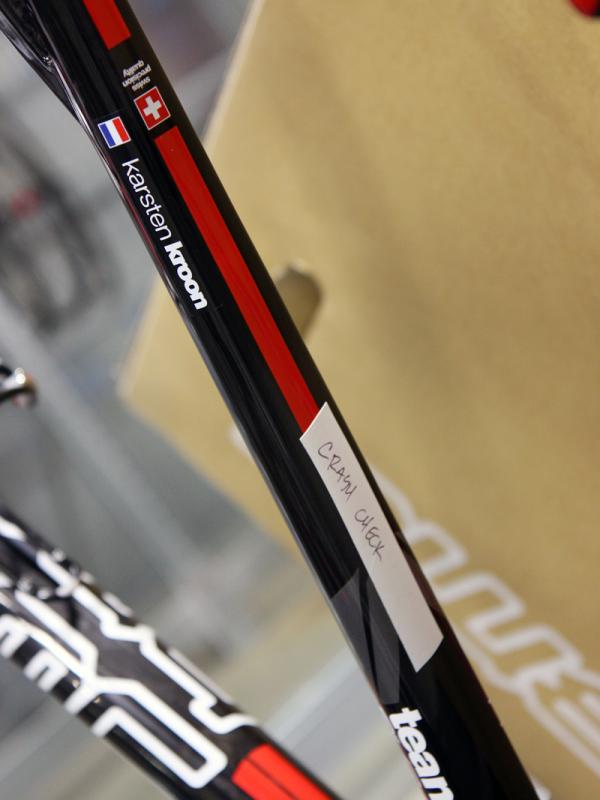
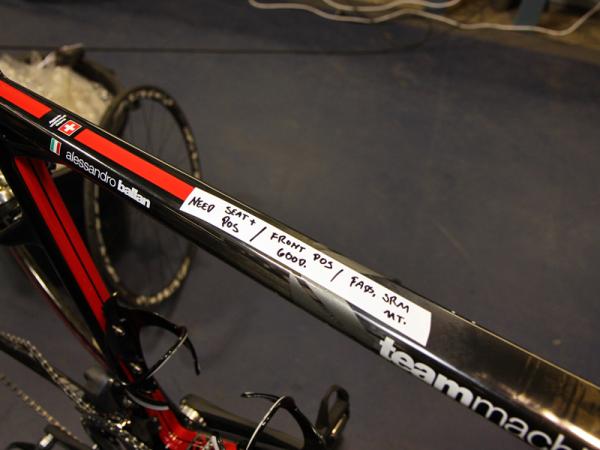
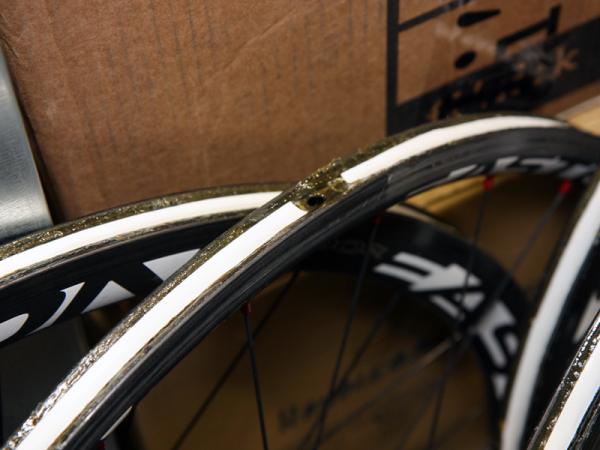
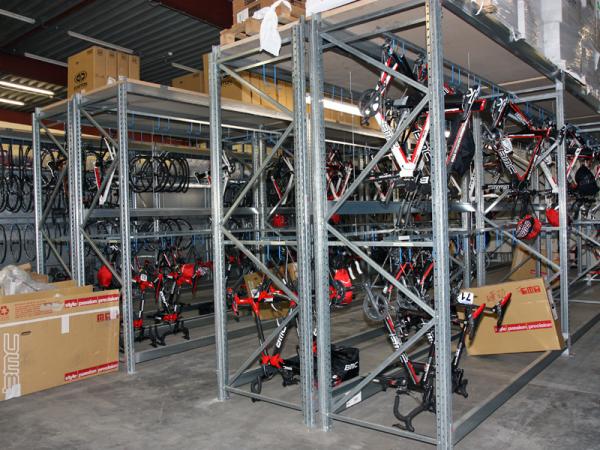
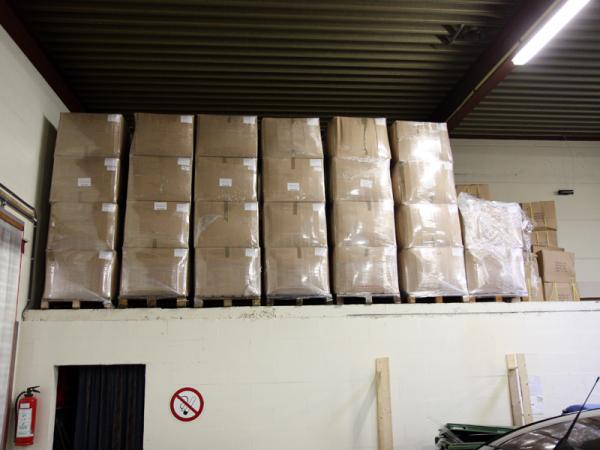
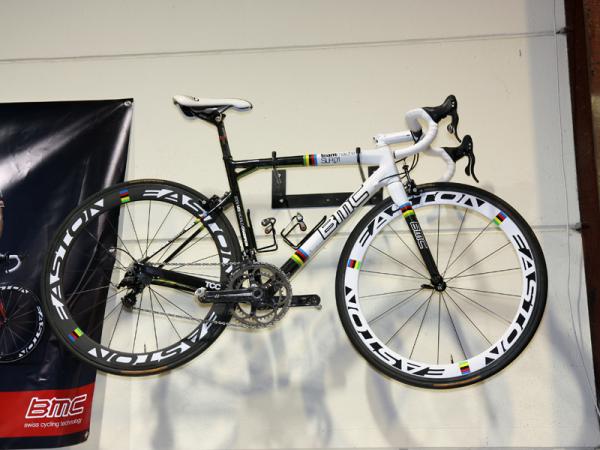
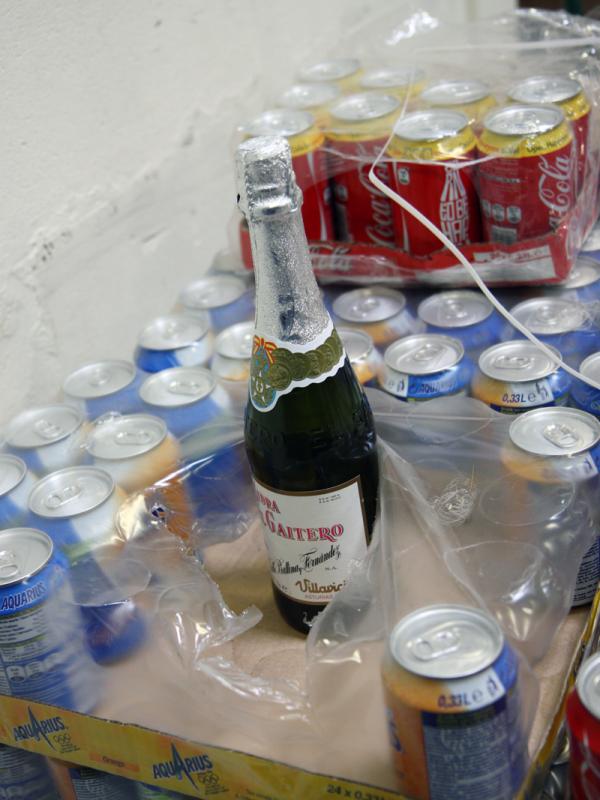
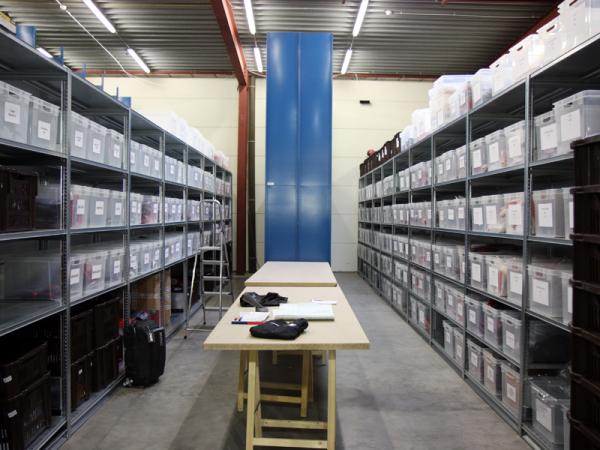
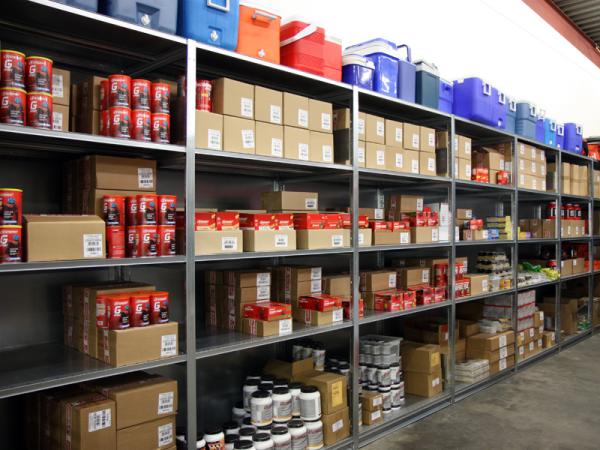
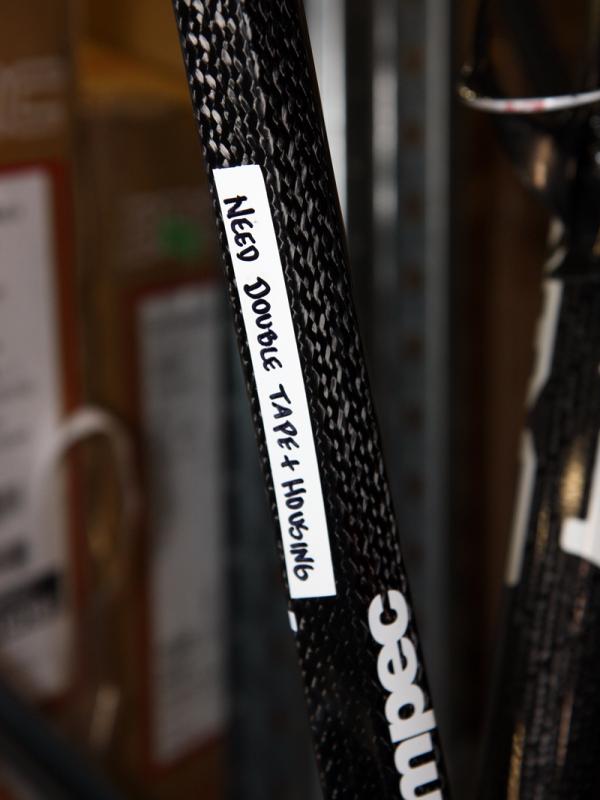
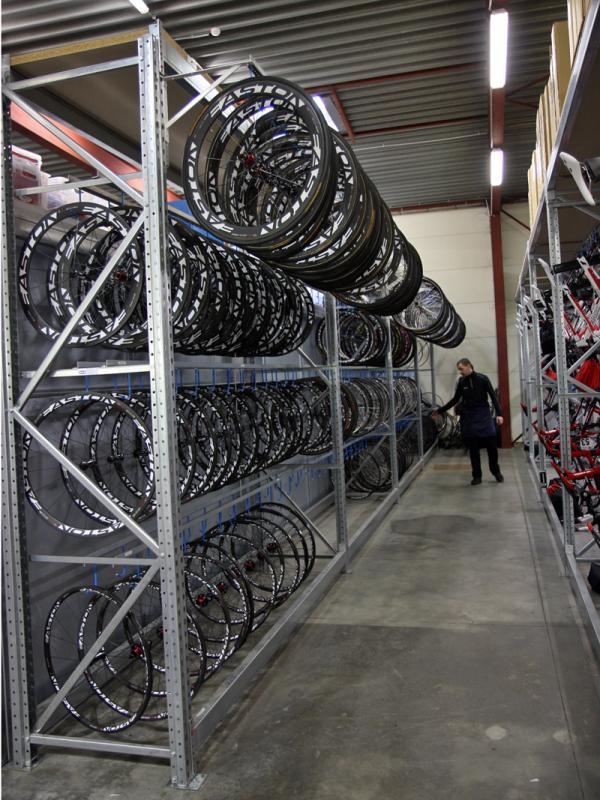
BMC once based their European mechanical operations literally out of a team truck, which enjoyed a semi-permanent home at a hotel parking lot in Izegem, Belgium. But that all changed in November 2009, when the team moved into a proper 930sq m (10,000sq ft) service course in nearby Nazareth – the base of operations for such standouts as Cadel Evans, George Hincapie, Alessandro Ballan, and newly signed rising star Taylor Phinney.
The front of the facility is occupied by a variety of offices but the rear two-thirds is where mechanics tend to the team's enormous stock of bikes and other equipment – and they now have the luxury of being able to load all of the gear onto the team trucks indoors. Naturally, there's also a sizeable work area with six service areas, countless rows of storage racks, and of course, lots of bikes.
How many exactly? Even BMC chief mechanic Ian Sherburne isn't sure off the top of his head but a quick bit of math suggests a staggering figure. At minimum, each of the team's 27 riders gets a race bike, a home bike, and both training and racing time trial bikes. Add in spares and the count rises to about five or six bikes apiece.
The unique demands of the cobbled Belgian classics inflates that number even further with each participant getting – again, at minimum – one specially modified machine with slightly longer stays and fork blades plus scalloped inner chainstay edges to gain more tire clearance. Top contenders such as Hincapie were outfitted with three. Finally, there are also other special bikes for various world and national titles, and for riders leading jersey competitions at the grand tours.
And then there are all of the wheels and tires. Even for Paris-Roubaix, BMC riders are almost exclusively on carbon tubulars this season and at any given moment, team mechanics have to have enough stock on hand to outfit concurrent race schedules with virtually any possible combination of Easton's three depth options.
The team have to purchase additional rear disc wheels for time trials – these typically come from Zipp since Easton don't currently offer a disc – and again, remember that riders' home bikes are generally fitted with clinchers, adding yet another model to the team inventory. All of those bikes are stored without wheels on massive multi-tier racks organized by rider.
Equipment that will be reused is one thing but consumables are another entirely. Endless boxes of Continental tubular tires reside up on a high platform back in the service area, the team keep a constant supply of soft goods – including both race and casual clothing – on hand for each rider, and there's enough energy food and drink to feed a veritable army.
Get The Leadout Newsletter
The latest race content, interviews, features, reviews and expert buying guides, direct to your inbox!
Also, mostly gone are the days when soigneurs had to spend hours washing and drying bottles after each race. As do many other top teams, BMC instead hand used bottles out to eager fans at the end of the day and start each race day with new ones. According to team general manager Jim Ochowicz, BMC will go through a staggering 18,000 bottles per season.
Sherburne manages everything with a giant spreadsheet that's color-coded depending on what's required. "Green means it's built, red means it needs to be built immediately, orange means like in the next week, and yellow means this guy might need it in August kind of thing," he said. Thankfully, Sherburne has help, with the team adding Jurgen Landrie to the payroll late last summer as a full-time service course mechanic.
"He's a wheel and tire guy, glues tubulars for the Gent six-day guys," Sherburne told us. "He's in his element when a stack of tubulars comes in. He really likes it. He helped us out last year part-time. He'll still go to some races, maybe 50 days throughout the season, but his primary responsibility is overseeing all of the equipment itself, inventory, checking stuff in and out."
As for Sherburne, he says he still puts in plenty of days on the road but his role has evolved with less hands-on and on-site mechanical work as the team has grown – and he's even moved to Belgium full-time. "I spend a fair amount of time here in the service course," he said. "As the team has gotten bigger, more of my job is administrative and email and spreadsheets so I'll probably be on the road 65 percent of what I used to be. It's like a ship in port – even when it's docked, it's still a full-time job, even in between races."
"Officially, Jurgen is our only full-time service course mechanic but Nick [Vandecauter], another one of our mechanics, lives just about 10km away so he's here fairly regularly. Although as we've gotten bigger and better supported, we're trying to make it so race mechanics come in the day before a trip, they leave the day after, and then go home for a week or four days or whatever it is, and then they come in and pack the truck and check everything and they split. Jurgen and I maintain this place on a day-to-day basis."
If nothing else, visiting BMC's service course offers a reminder that while the riders get the glory, there's a sizeable machine standing in support and cycling is truly a team sport. While the statistics surrounding the equipment are already impressive enough, consider one more: BMC employ nearly two staffers for every rider on the team and save for Sherburne, not one of their names begins with an "I".