Behind the scenes at Trek HQ - Gallery
America’s last large-scale domestic bicycle manufacturer
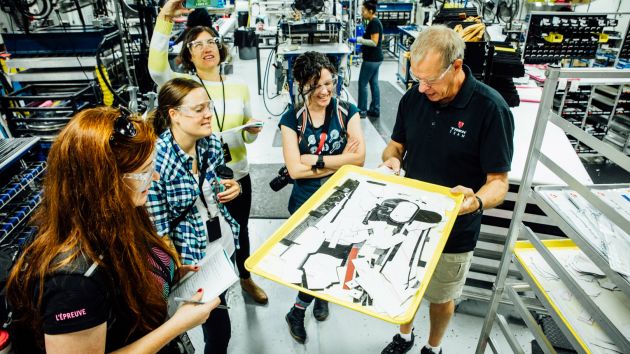
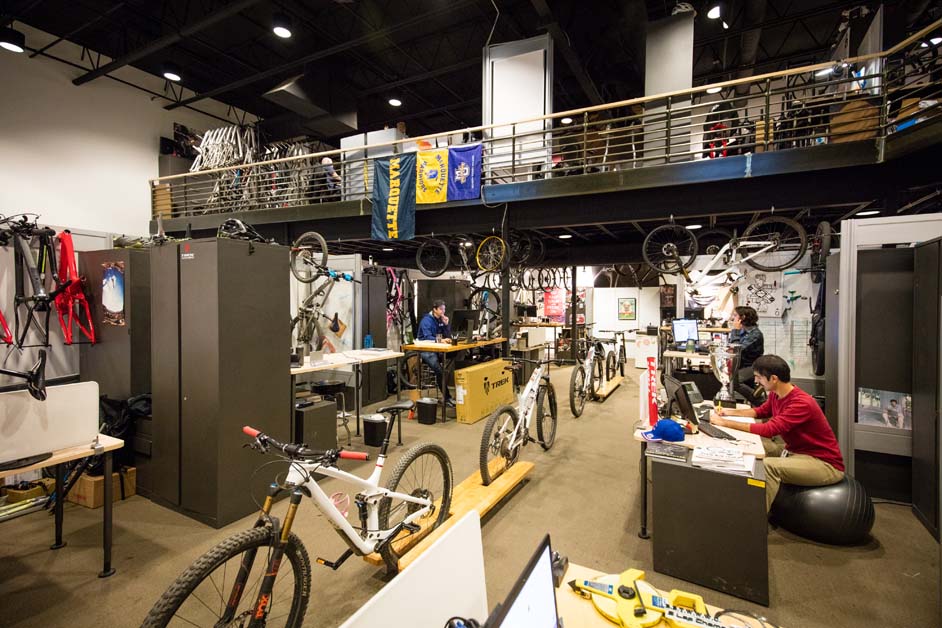
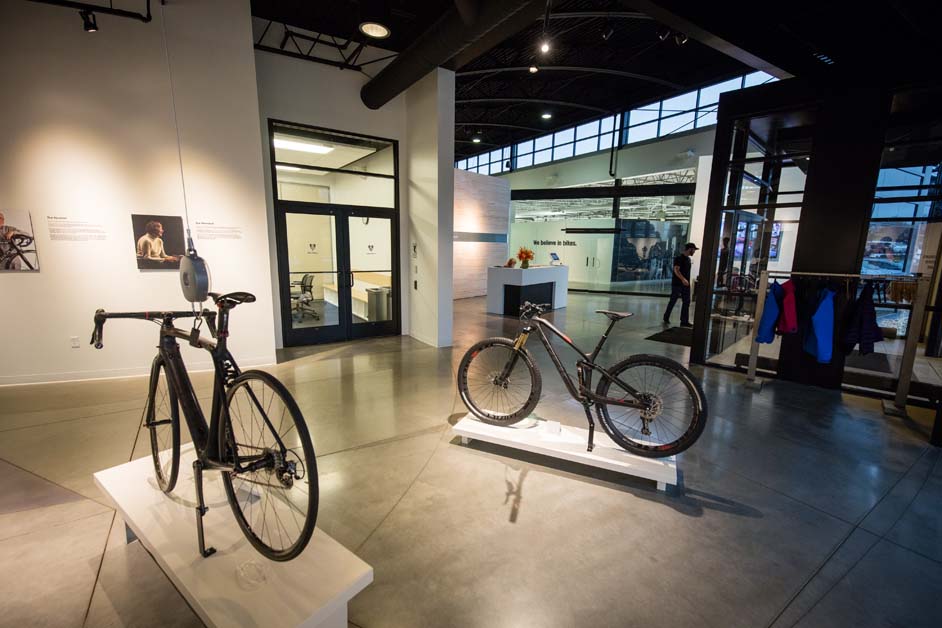
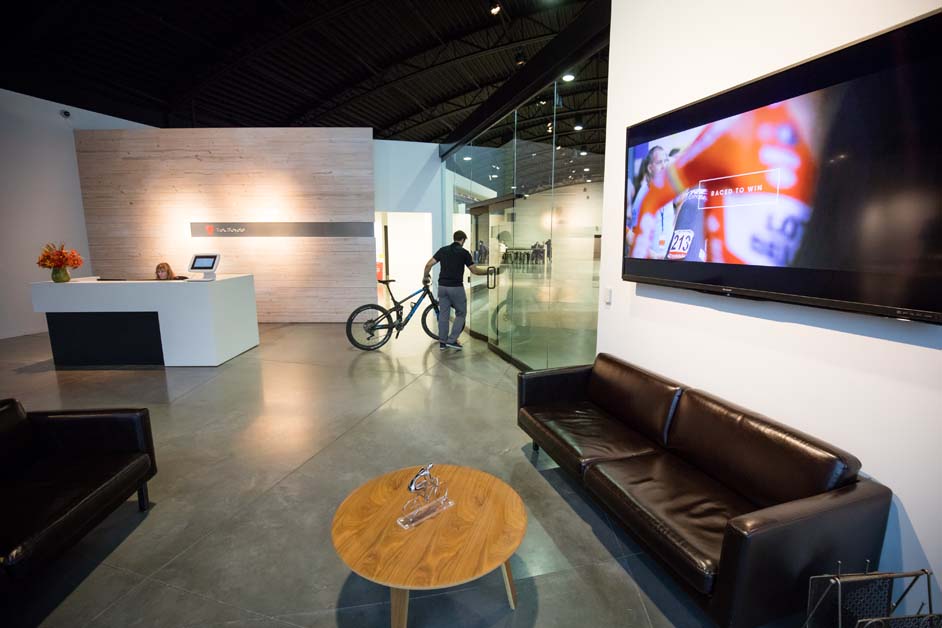
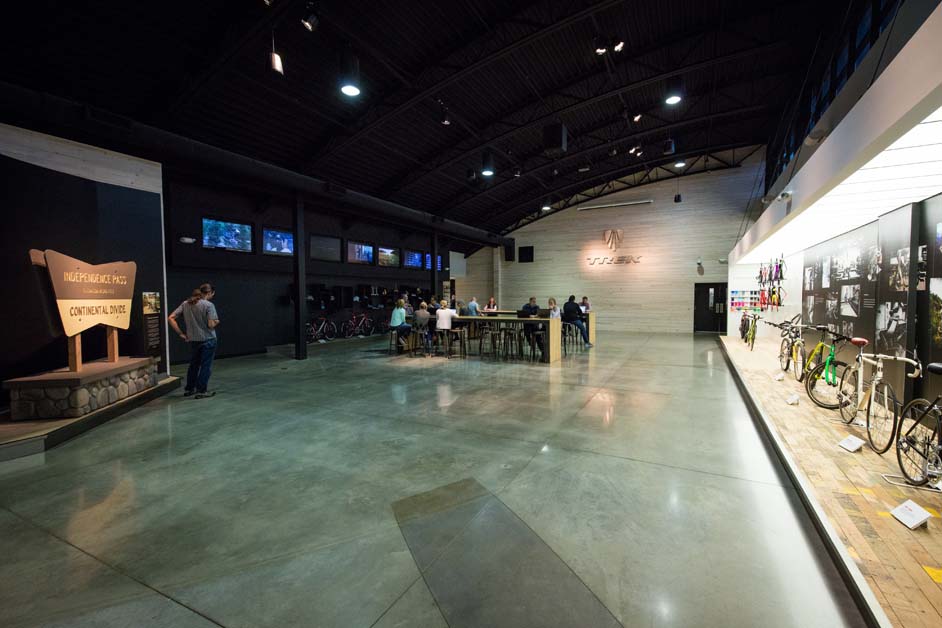
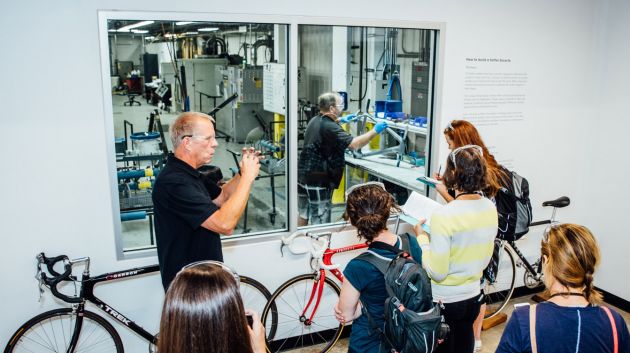
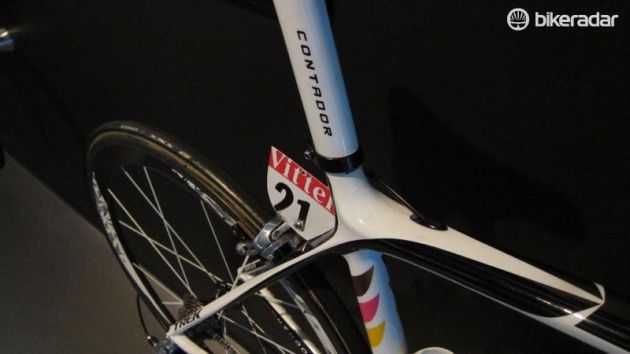
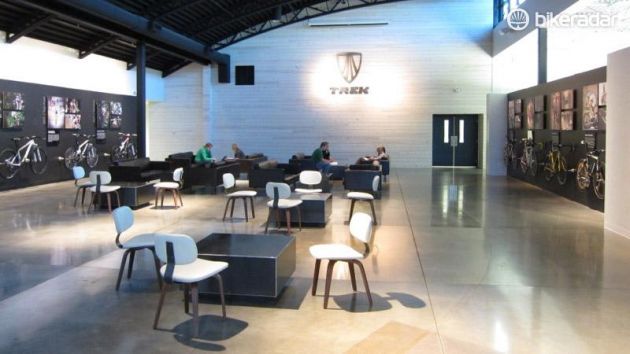
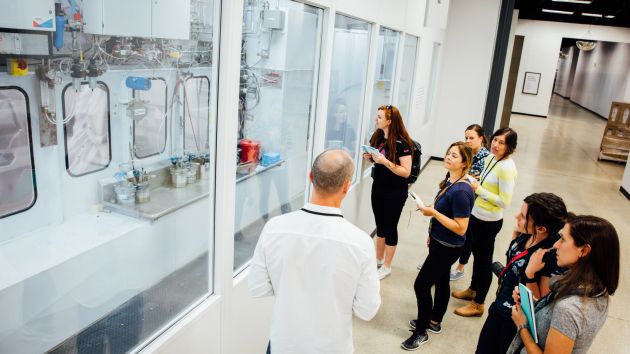
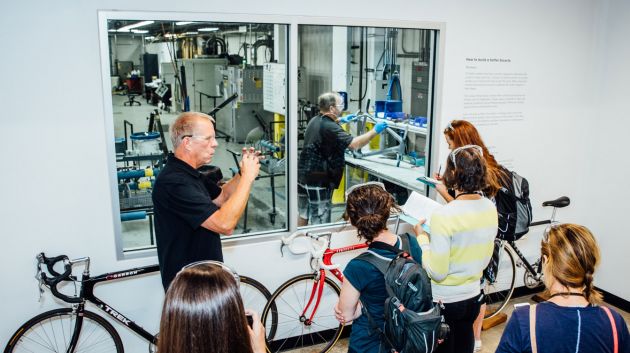
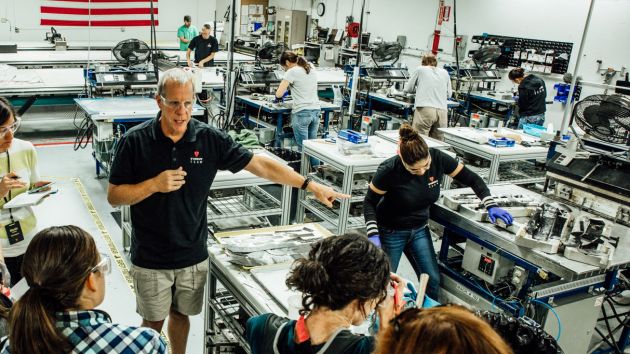
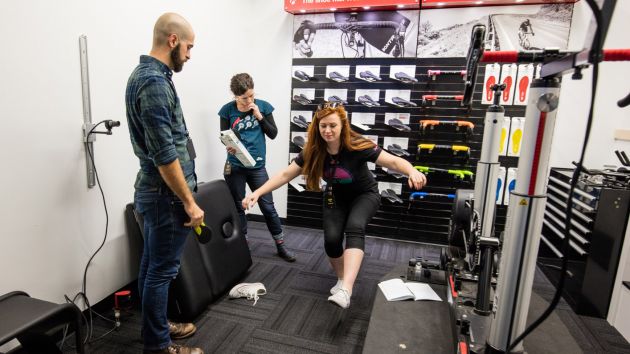
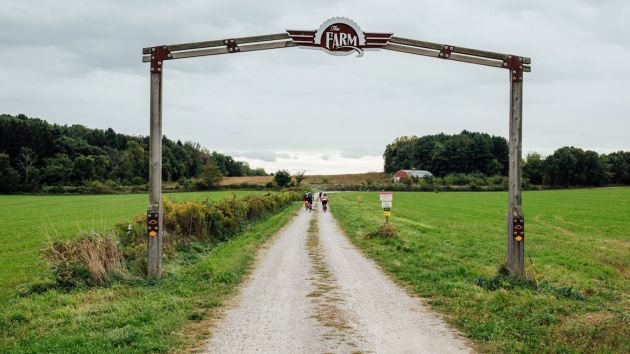
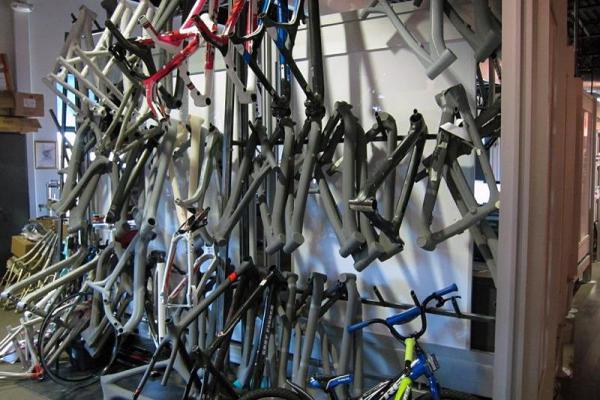
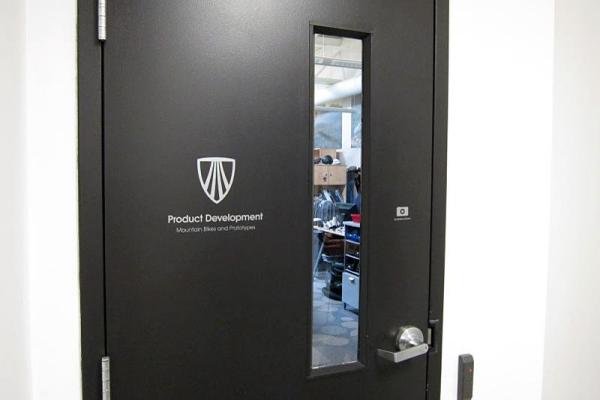
This article originally appeared on BikeRadar
Trek Bicycle Corporation’s headquarters in Waterloo, Wisconsin is an impressive place to visit. The 205,000 sq ft facility houses 900 employees and is one of the only large-scale bicycle manufacturing factories left in the US. On the walls hang bikes and images that span the breadth of Trek's rich history, and in the offices and work spaces the bikes of the future are being developed.
Comprising various offices, testing labs, training spaces, a gym, bike fit facilities, workshops and manufacturing areas — not to mention its very own private mountain bike trail network — the Trek HQ has pretty much everything covered. It's huge. But walk through the corridors and you get the sense that despite its size and standing, it's a company that takes as much care and consideration with its employees as it does the bikes it creates. Staff bikes line long corridors, and regular gym and fitness classes are timed to allow everyone to join in.
For more on this subject
- 2017 WorldTour team guide
- Fabian Cancellara's Tour de France Trek Madone
- Jack Bobridge's Project One Trek Madone
- Alice Barnes' stunning Trek Madone at the Aviva Women's Tour
- Trek's new range of road bikes for 2017
- Fabian Cancellara's Trek Domane for the 2016 Classics
- Bauke Mollema track testing on the Trek Speed Concept
The employee roster breaks down roughly 50/50 when comparing white to blue collar workers, illustrating that Trek's domestic production is more than a token effort. The 400-or-so-strong white collar workforce makes up the vast majority of Trek’s engineering, product management, graphic, marketing and business support staff. However, Trek also maintains a three-person suspension development lab in Southern California, run by Jose Gonzales.
Why buck the trend and manufacture in the US? Trek says that while it's admittedly costly, having the connectivity and communication between the engineering and manufacturing departments is an important element of the company's success and development. Designers, developers and engineers can talk to each other face to face.
There's also a significant female presence in the workforce, and while not quite a 50/50 gender split, there's good representation of women working at every level of the company, from the workshop floor to engineering and design, management and beyond.
Get The Leadout Newsletter
The latest race content, interviews, features, reviews and expert buying guides, direct to your inbox!
While there's plenty to see, there are also areas that are hush-hush, and understandably so. Much as we'd love to have nosed around the prototype lab, for example, it was no go.
Home of the high-end carbon frame
At the heart of its Wisconsin headquarters is Trek's carbon manufacturing. All of the Madone 9 Series road bikes — 16 models, if you include framesets — are made in Waterloo, along with other top-tier models including Speed Concept 9 Series time trial bikes and Top Fuel, Fuel EX 9.9, Remedy 9.9 and Superfly 100 full-suspension rigs. The rest of Trek's bikes are made in Asia, where most of the bike industry sources its manufacturing.
Each part of the frame is checked manually and assembled by hand
Sheets of impossibly light carbon-weave arrive frozen to avoid damage or warping and are machine cut. The patterns are created by computer programs that translate 3D designs into 2D patterns, and once the carbon is CNC machine cut to size it's hand-placed into moulds. Trek favours a single unit production line, where all the constituent parts of a frame are assembled at the start of the process: one barcoded tray has a jigsaw of carbon sheets that will go through the manufacturing process to emerge at the other end of a bike, making it possible to track an individual frame from start to finish.
Trek opts to make its bikes in pieces, rather than the monocoque or one-piece construction that is industry standard. This allows for greater quality control, Trek claims, done by visual and manual inspection of each part before they are bonded together using a structural epoxy adhesive.
Once moulded into shape, the various parts are bonded together — again by hand. What's amazing to see is how much work, both human and robotic, goes into creating just one bike.
Add a little colour
The Wisconsin HQ is also the home of Project One, which allows customers to pick custom graphics and paint packages, in addition to the sizing and spec of their new bike. All Project One bikes worldwide are painted in the Wisconsin facility; decals and templates are painstakingly applied by hand on site, with various layers of paint and varnish applied by hand, or with the help of high-tech robots.
The robotic painting room is full of high-tech and efficient machinery
The robots are something to behold, and allow an incredibly efficient painting system that takes just 100cc of paint to cover a bike, reducing both wastage and weight — the vapour coating system means, Trek claims, a final weight of 5g on average for paint and finish.
More complicated paint jobs are done by hand in one of four paint booths, each with a downward airflow that prevents micro droplets of colour contaminating other bikes.
Racing forward
What do Rachel Atherton, the Drop women's cycling team, Fabian Cancellara, Tracy Moseley, Brook McDonald and Emily Batty have in common? They're all Trek sponsored athletes and part of Trek Factory Racing, which covers road, triathlon and mountain biking.
Racing is an expensive thing to support, but there are tangible benefits, according to Trek. Having its own teams means having access to riders at the top of their game, pushing riding to the limits and as a result able to help feed into the design process. It also, of course, means that Trek's products are seen at the most prestigious events and under some of the best riders.
Back to school
Trek also runs what it calls its Trek University: training facilities for retailers and mechanics covering maintenance, product training, essential shop management skills and bike fitting.
The Wisconsin HQ has a Precision Fit studio, with three fit bays, a motion capture device and a number of fit cycles to train retailers and bike fitters in the Trek Precision Fit system. There's also a training facility, the School of Certified Service, which has room for up to 20 people and offers a range of courses from technician training to operations and management.
Trek also offers a number of scholarships to support female mechanics to acquire and develop their skills and progress through the industry.
Testing the limit
Compliance is a word that gets thrown around a lot with a bike's performance, but in the world of manufacturing it also refers to international safety standards. Trek has its own testing facility, putting each part of the bike through a brutal program of stresses and strains to ensure the bikes are safe and fit for purpose.
But the testing facility is also about pushing the limits of what's possible and seeing what can be done better. Being based on one site means that designers, engineers and researchers from various departments can work together more easily, and create some interesting and — at first sight — slightly out there things.
One great example is the giant treadmill that sits in the middle of the testing facility with a rider harness that dangles from the ceiling. Designers from Trek wanted to develop a way of testing how bikes respond to uneven terrain, but with as few variables as possible. The result is a treadmill, adapted from one commercially available, with an uneven slatted surface. It's big enough for a rider and bicycle, the speed and incline can be controlled, and the slats can be changed to simulate different types of terrain.
The Farm
A visit to Trek HQ isn't complete without a side visit to The Farm, Trek's very own private trail centre. Imagine creatively designed trails snaking through woodland, complete with drops, jumps, North Shore (man-made) features and more. The only downsides are the aggressive mosquitos.
The Farm, Trek's very own trail centre
Aoife loves a bike-based adventure, whether it’s out in the mountains on her MTB or exploring new places by road or gravel. She’s tested a LOT of bikes and kit, and is passionate about making cycling accessible for everyone. After all, it’s much more fun with friends, right?
Bikes currently owned: Juliana Maverick, Liv Devote