A look inside Shimano's shrouded wheel factory
If you were to wander into Shimano's Malaysian wheel operation, you'd be greeted by the usual...

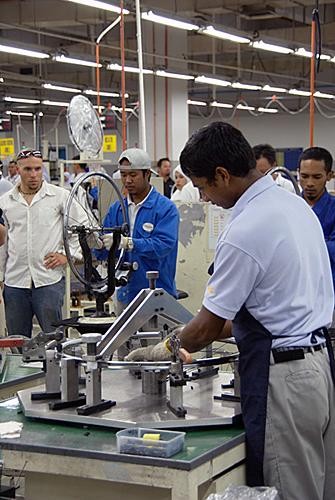
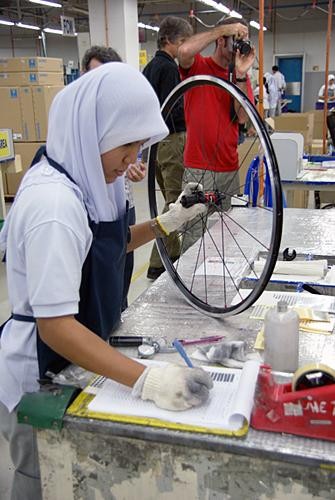
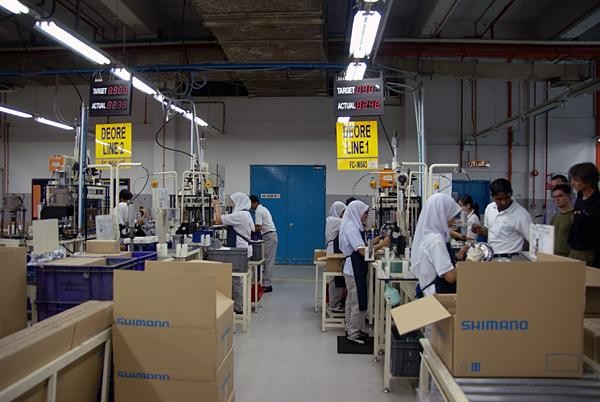
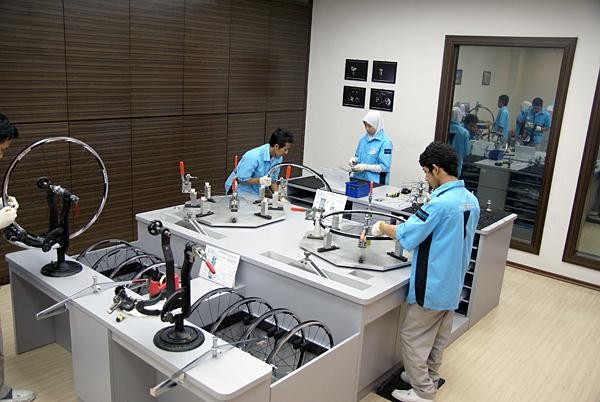
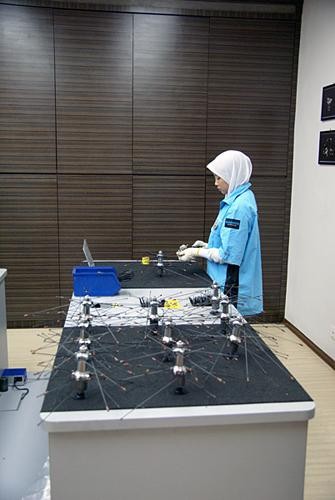
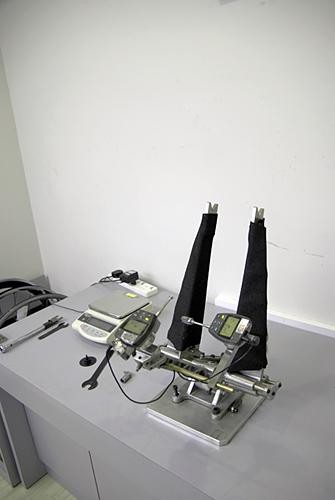
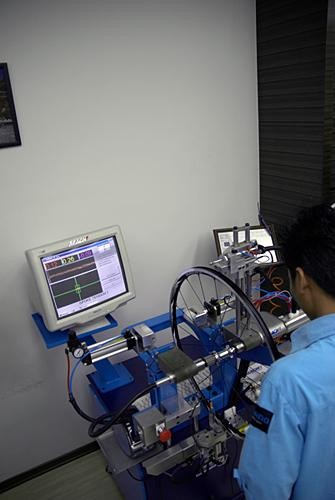
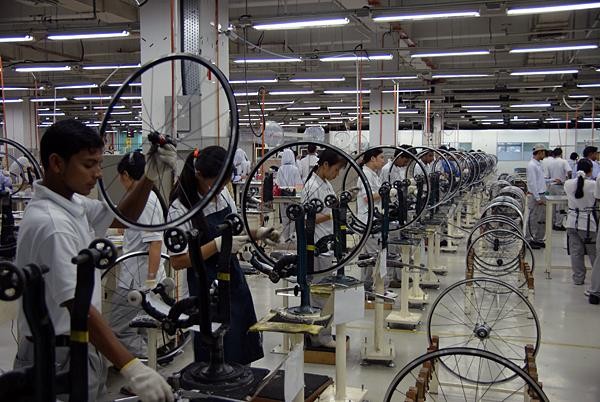
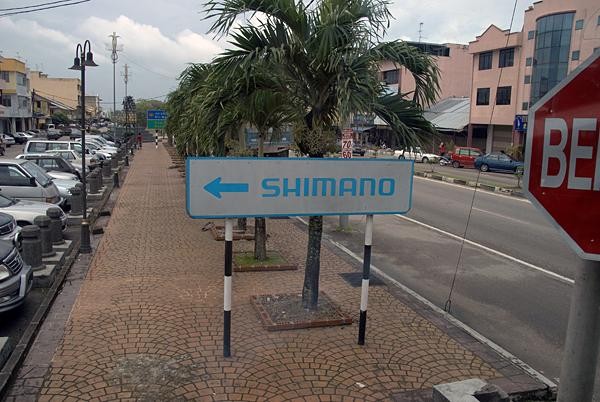
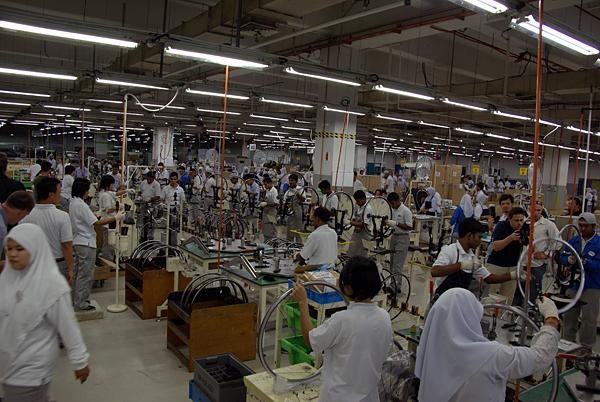
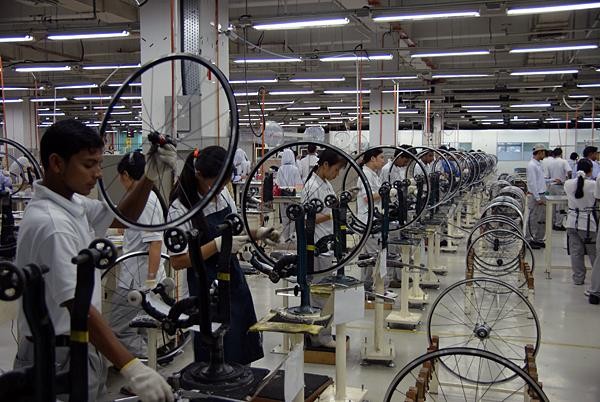

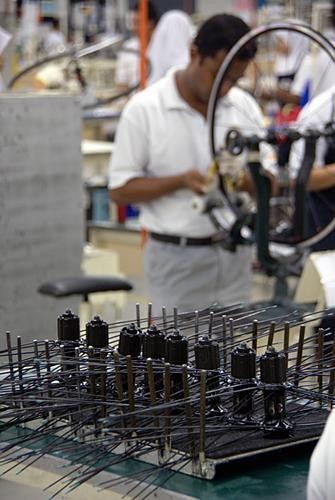
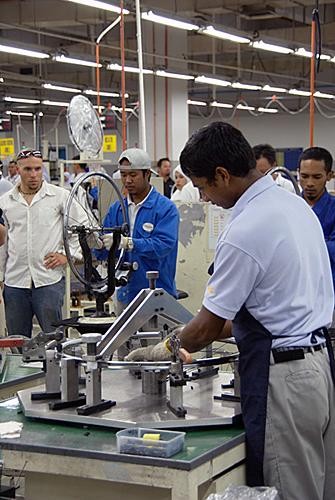
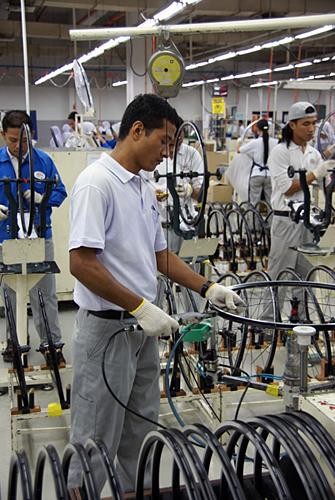
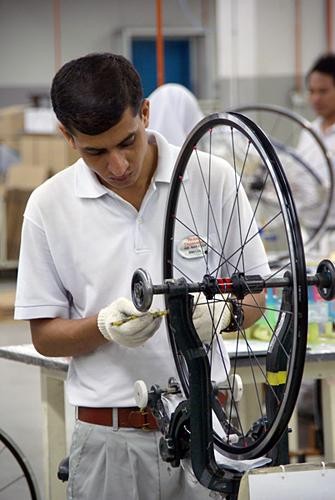
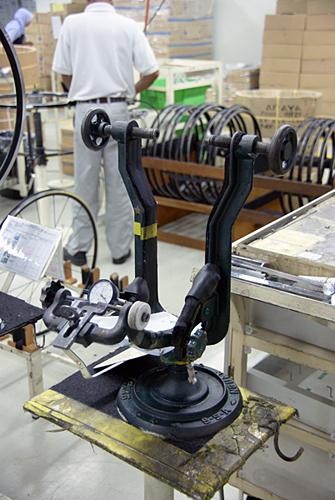
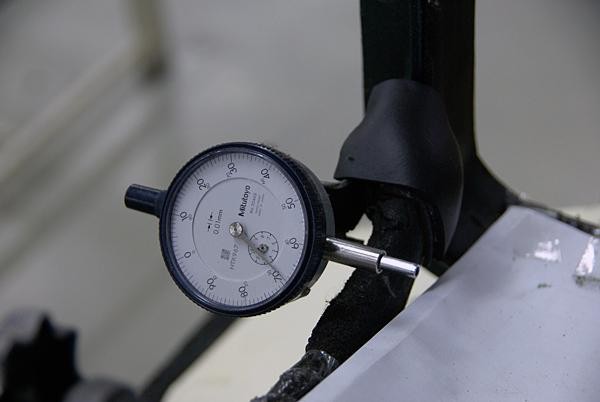
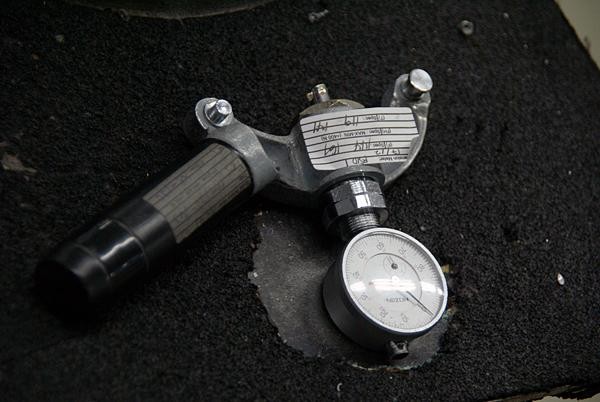
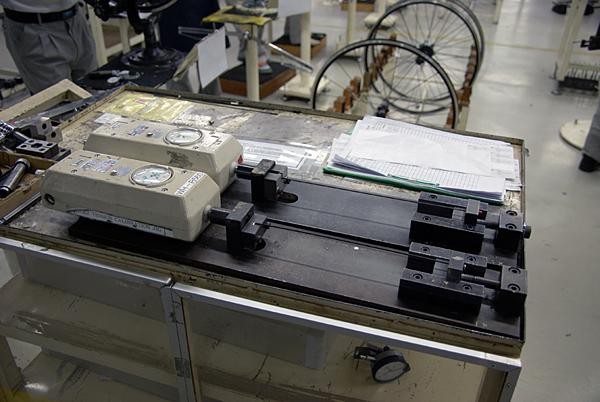
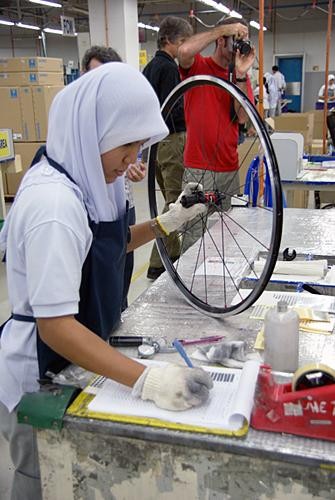
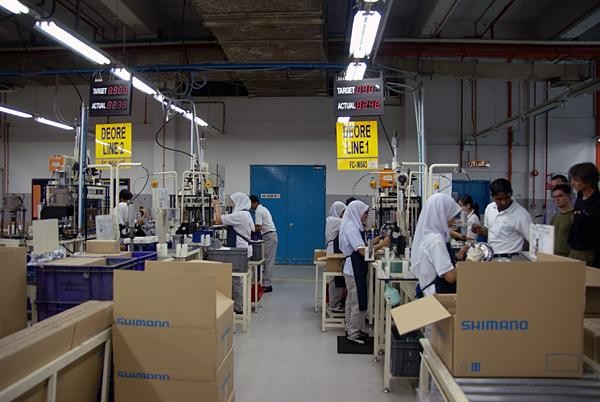

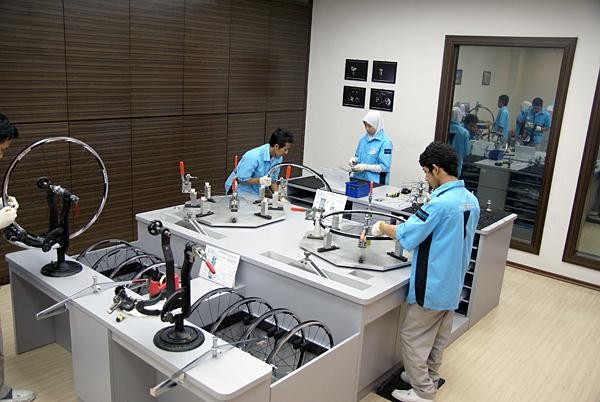
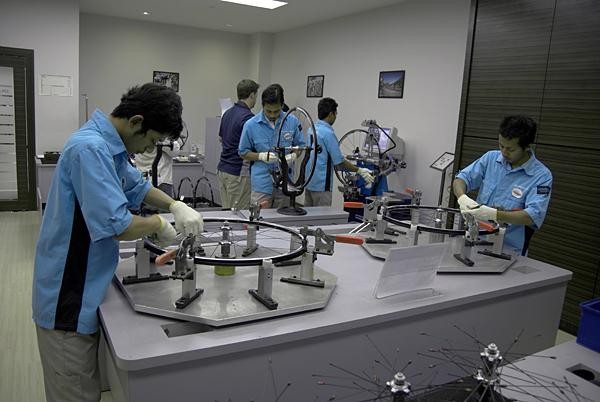
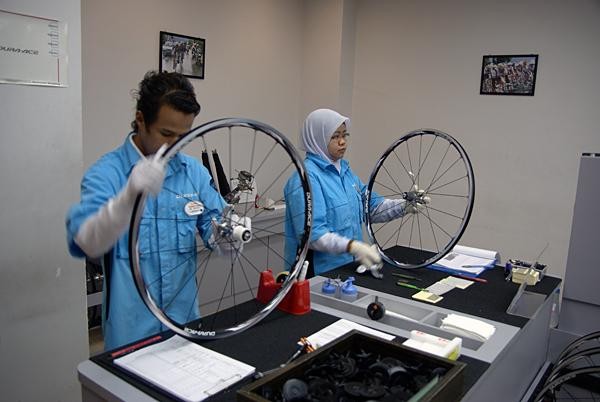
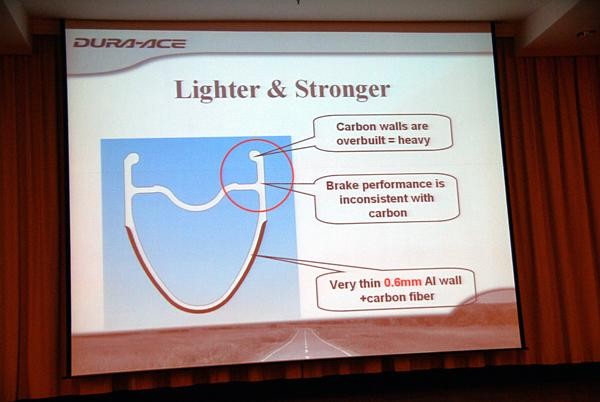
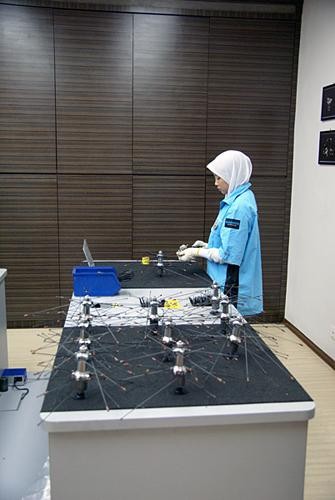

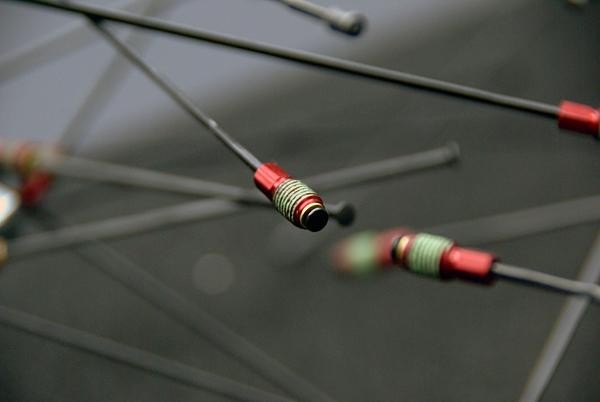
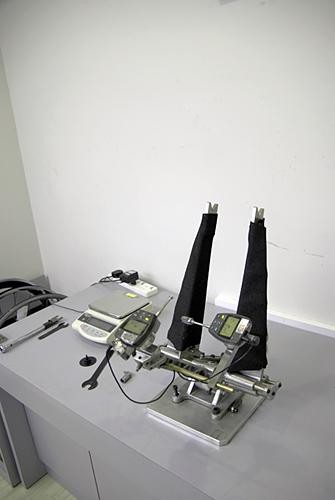
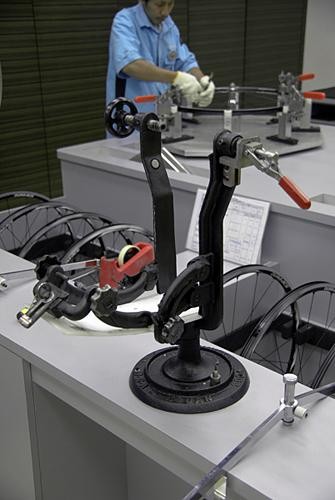
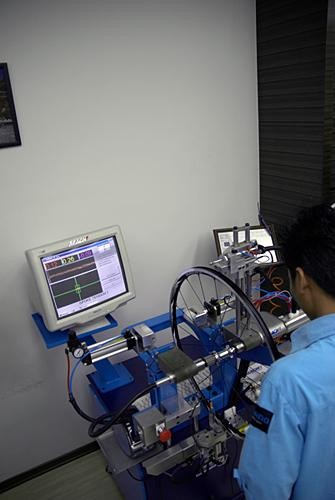
Tech Feature: Shimano wheel factory visit, January 8, 2008
Shimano has taken the status of its wheel line from 'somewhat questionable newcomer' to today's comprehensive array of top-of-the-line ProTour-quality models in just a few short years. Shimano opens up the doors of its wheel factory in Malaysia to outsiders for the first time, and Cyclingnews Tech Editor James Huang heads across the Pacific to snoop around.
If you were to wander into Shimano's Malaysian wheel operation, you'd be greeted by the usual cacophony of factory machinery. All of the company's road wheelsets (and many, if not all, of the mountain bike ones) are built here amidst the whoosh of compressed air lines, the banging of presses, the buzzing of drills, the whirring of CNC mills. The second thing that strikes you is the sheer size of the operation. Shimano won't say exactly how many wheels it produces or sells, but considering that the 12,000 square meters of pre-preg carbon fiber that is kept on hand at any given time period exclusively for use in wheels lasts but a single week and you can at least get an idea. Once you remind yourself that only a handful of Shimano's wheel uses carbon fiber at all, the scale of things really begins to set in.
As one would expect from Shimano, sound engineering principles and an unyielding dedication to quality assurance are pervasive throughout the surroundings. Everything is done with exacting precision and care, and a QC check is done after everyprocess. Yet in spite of the overwhelming mechanical theme of the environment, one also can't help but notice the underlying and ubiquitous presence of human hands everywhere you look, and they're not just manning the machines.
Each and every wheel is fully handbuilt all the way from initial lacing to final true and tension. Vertical and lateral runout for each serialized wheel is individually recorded, which also means that each one can be traced back to a particular builder, date, and material batch. This yields obvious dividends for Shimano's enviable quality targets (the non-conformance rate is said to be less than 0.03%), but it also plays a less obvious role that is no less important. According to Shimano, the 'feel' of human hands simply can't be matched by a machine when it comes to the black art of wheel building. Moreover, attaching a name to each wheel instills a sense of pride and personal accountability. Hear, hear.
"The pursuit of the perfect ride"
Perhaps nowhere is this human aspect more evident than in the man responsible for Shimano's wheel program, 'Mr. Wheel' himself, Shinpei Okajima. Okajima began his tenure at Shimano back in 1976 (he confesses that Shimano is the only company he has ever worked for) and his achievements include helping to develop indexed shifting, Shimano's first carbon shoe outsole, as well as SPD and SPD-SL footwear and pedals. Somewhat surprisingly for Shimano, though, he holds no formal engineering degree yet is in charge of the company's Action Sports Division, which handles wheels in addition to other key product lines.
Get The Leadout Newsletter
The latest race content, interviews, features, reviews and expert buying guides, direct to your inbox!
Regardless, he's clearly well qualified at least as far as bikes are concerned. Okajima is a seven-time Japanese national cycling champion (primarily on the track if we understood correctly) and as evidenced by the well-worn glove tan and trim physique, likely spends more time pedaling on pavement than most of the people who use the products his division develops. "All my ideas come from my riding," he says. "I wake up at 5 o'clock and ride two to three hours before going to work." On a side note, Okajima is also an avid snowboarder (and yes, he uses Clicker step-in bindings, which are still developed and available in Japan).
Ironically, Okajima's lack of a formal engineering background has probably benefited Shimano in its wheel development. For a company that is so decidedly objective and engineering-centric in everything it does, his measure of a good wheel is markedly subjective and unscientific. In his opinion, and as most of us would likely attest, the true measure of a good wheel is not the numbers it produces on a bench test but rather how it feels on the road.
We've all ridden ultralight wheels that feel spindly, seemingly heavy wheels that still manage to feel fantastically lithe, and wheels that just feel superb for reasons which no one seems to be able to put a definitive finger on. Okajima readily acknowledges that it has been difficult to determine exactly what measurable parameters contribute most to a wheel's overall performance but insists that a balance of all of the key players is crucial: dependability, stiffness, compliance, torsional and lateral rigidity, light weight, aerodynamics, and even price and style all factor in.
Cream of the crop
Among a sea of ultralight competition, Shimano's top-end Dura-Ace wheel models have occasionally suffered from criticism that they just weren't light enough. Indeed, one of those performance metrics that Okajima does focus on is rigidity. As a result, some of those added grams come from an unwillingness to sacrifice stiffness to satisfy the weight weenies or compromise on durability, and we'll agree based on our evaluation of the WH-7801-SL wheels last year.
Even with a little extra mass here and there, the Dura-Ace line is still far from lacking in technology and has racked up plenty of race wins (11 UCI Pro Tour victories and 42 Grand Tour stage wins if you go by Shimano's tally). Shimano continues to forge ahead with the scandium-enhanced rim on its updated Road Tubeless-compatible model, and its recently introduced WH-7850-C24 Carbon Clincher melds an incredibly thin-walled (just 0.55mm in some areas) aluminum extrusion with a carbon fiber reinforcement. According to Shimano, the resulting 380g 24mm-deep clincher rim is superior to an all-carbon version in that the braking is more predictable and the sidewalls don't need to be overbuilt to handle high pressure, especially when hot. The complete wheelset boasts a claimed weight of just 1380g.
Whether or not you agree with Shimano's bold assertion about the WH-7850-C24 rim, that labor-intensive theme returns when it comes to the rim's construction. There are four pre-cut pieces of carbon fiber over each of the spoke holes (26 layers of fiber in total), and each of those pieces is applied and trimmed by hand in a climate-controlled 'clean room'. No coffee to be found here, folks.
Naturally, each Dura-Ace wheel is handbuilt as well, but in a wholly separate area of the facility reserved for Shimano's most experienced and talented builders. Much as Dura-Ace represents the pinnacle of the Shimano wheel line, the prestige of being a Dura-Ace wheel builder is a highly sought-after position within the ranks: the room more closely resembles a showroom than a factory, it's pleasingly quiet, and unlike the main wheel building area, it's also air conditioned.
What's next?
Shimano representatives did take the time to show us a new model that's currently in the midst of development, but if we told you what it was… well, we'd just have to kill you. However, we will say that the more astute readers will probably be able to figure it out on their own without too much trouble as it represents a natural progression in the lineup. Either way, let's just say that we're awfully excited about it.