Tech feature: The work of Wheel Energy
Taking the mystery out of tyre testing and development
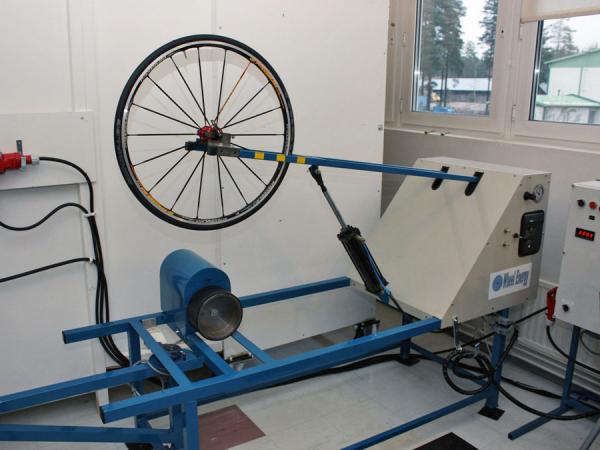
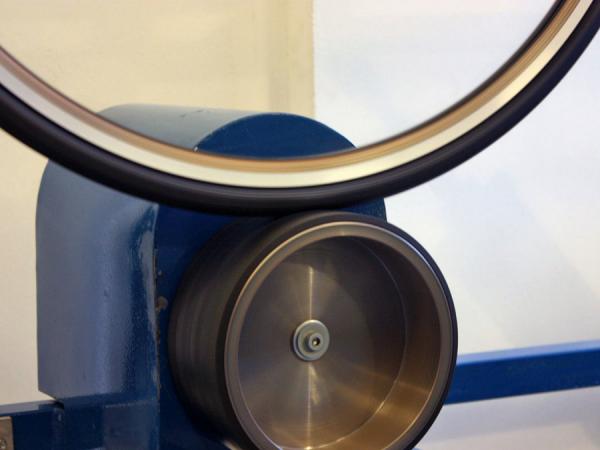
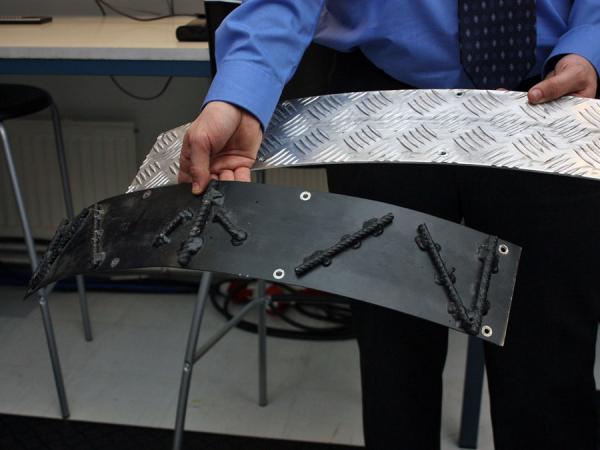
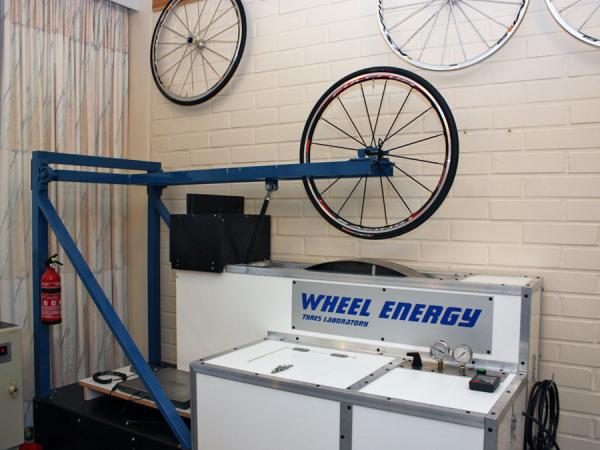
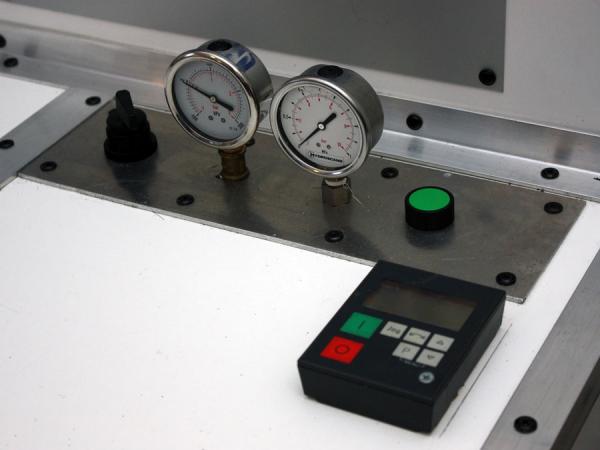
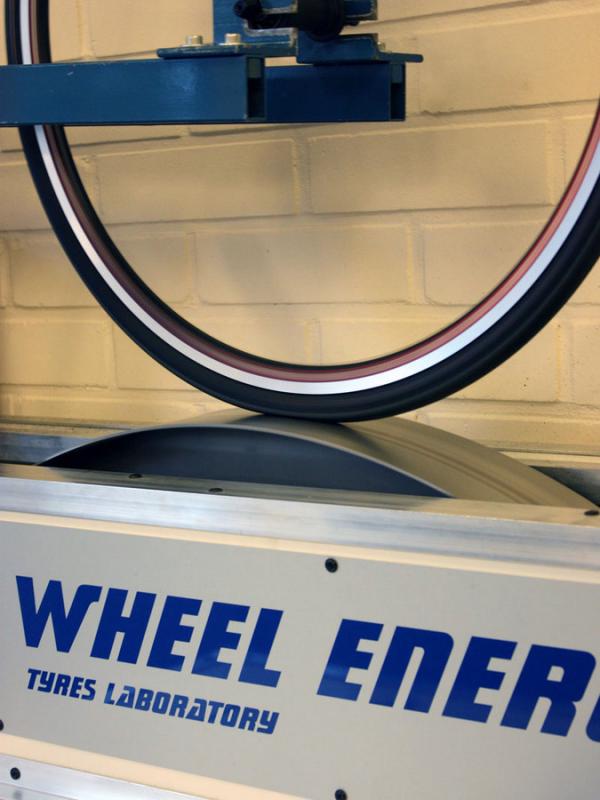
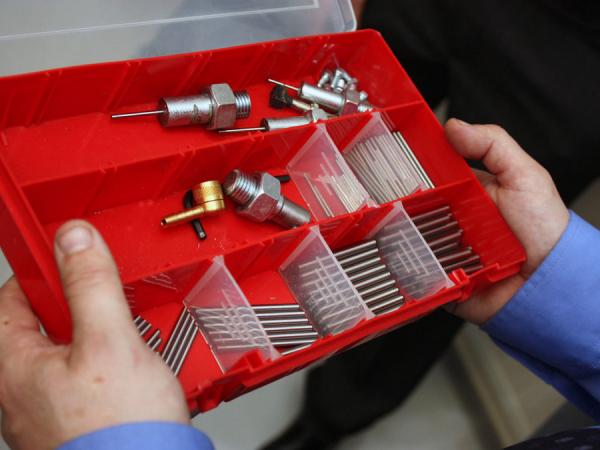
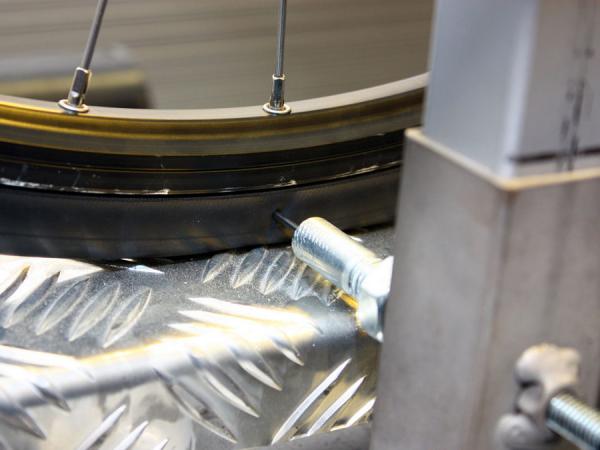
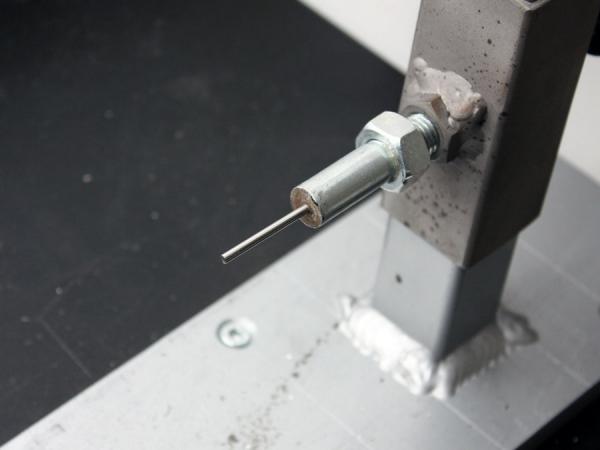
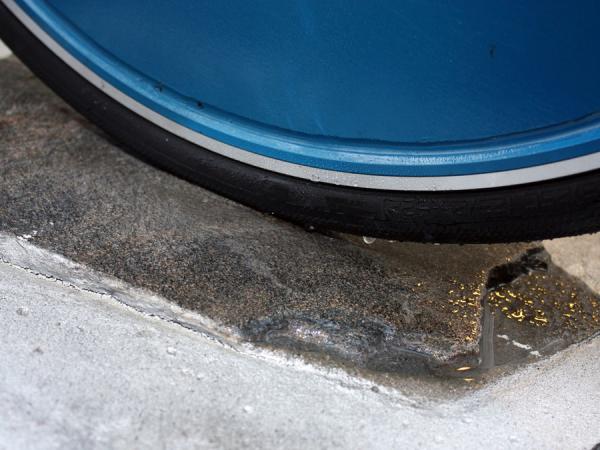
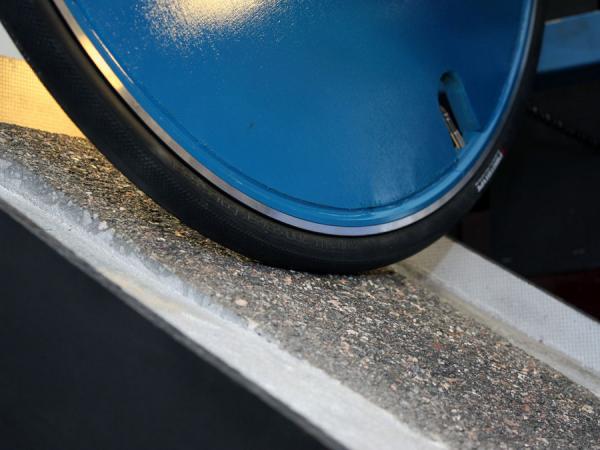

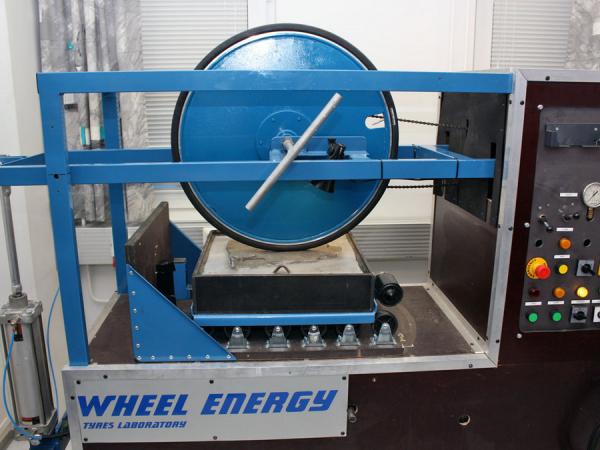
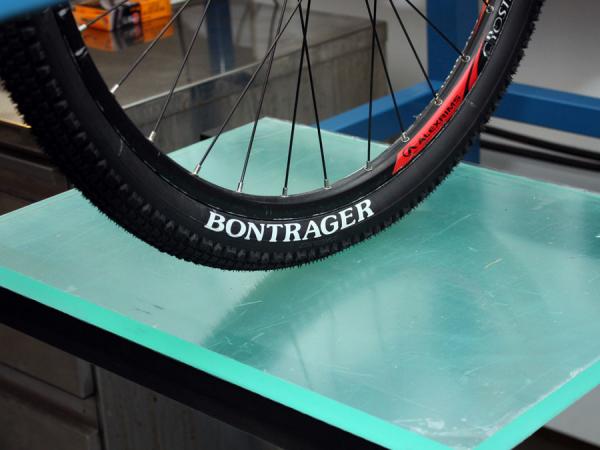
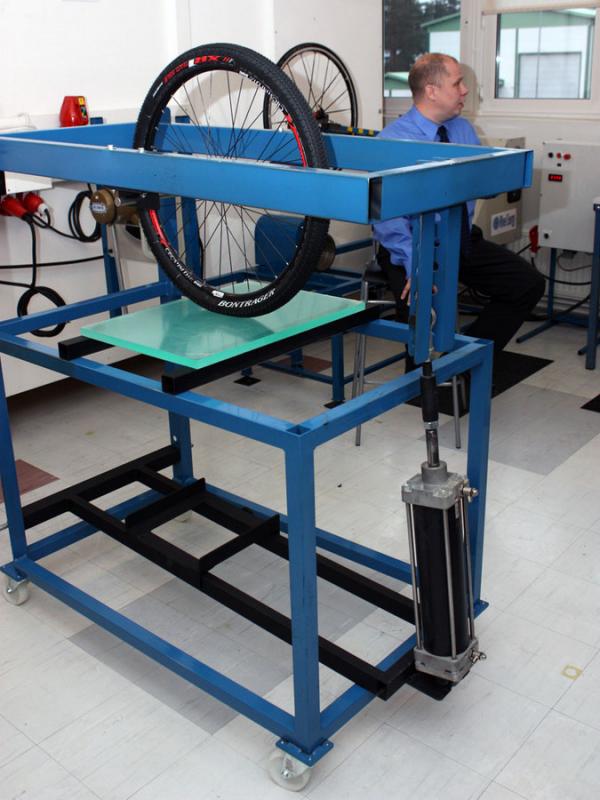
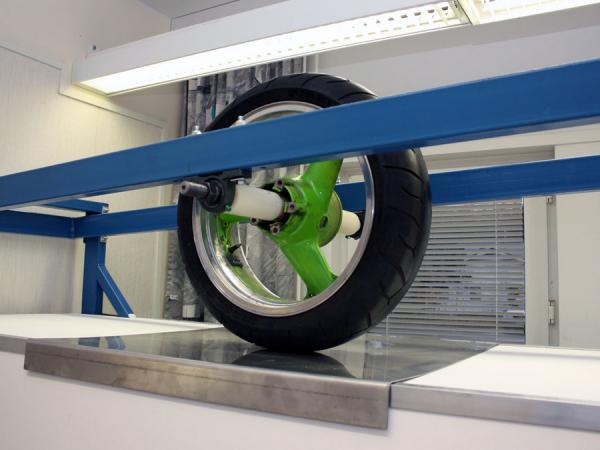
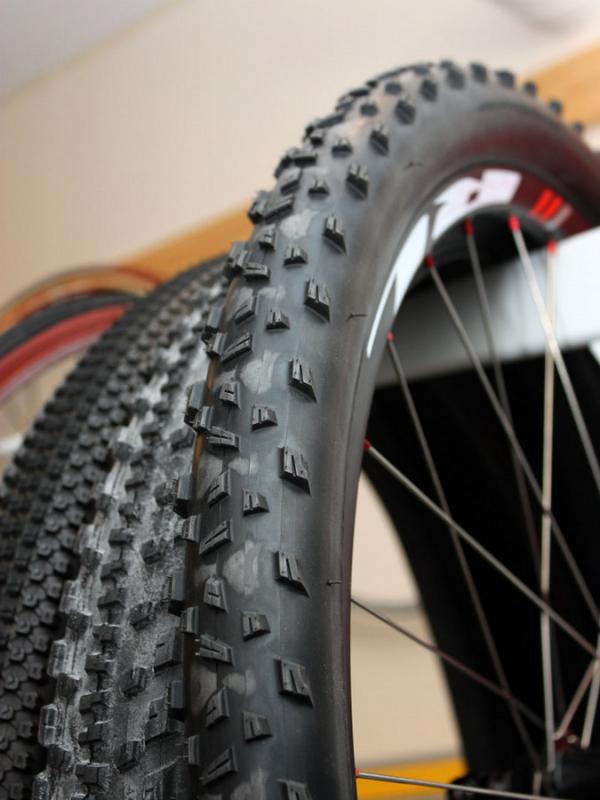
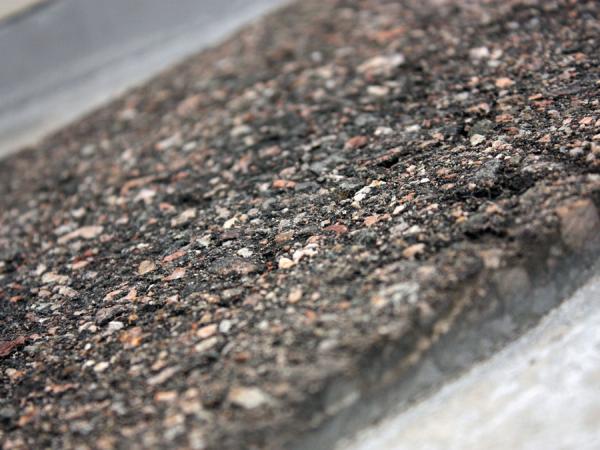
Tucked inside a small industrial complex in Nastola, Finland, is the nondescript grey building of independent third-party tyre testing facility Wheel Energy.
Using a battery of custom purpose-built machines, founders Petri Hankiola, Veijo Pulkkanen, and Marko Savolainen are addressing some of the common questions surrounding bicycle tyres and they're coming up with some interesting answers that no longer have to rely on word of mouth, tradition, or intuition for their veracity.
Take these conclusions for example:
Wider tyres roll faster than narrower ones: Many riders have argued for years that narrower tyres – especially on the road – are faster and more efficient than wider ones when in fact, the opposite is true. According to Wheel Energy, the key to reducing rolling resistance is minimising the energy lost to casing deformation, not minimising how much tread is in contact with the ground.
All other factors being equal, wider casings exhibit less casing 'bulge' as a percentage of their cross-section and also have a shorter section of deflected sidewall. How big a difference are we talking about here? For an equivalent make and model of tyre, Wheel Energy claims the 25mm-wide size will measure five percent lower rolling resistance on average – the supposed average limit of human detection – than the more common 23mm-wide one.
Unless you're a pure climber and solely focused on weight, the takeaway message here is that you'll go generally faster on wider rubber even if it's slightly heavier.
Larger diameter wheels roll faster than smaller ones: Yep, 'tis now been confirmed in the lab – 29ers roll faster than 26ers. Wheel Energy says the effect here is similar to that of tyre width in that larger-diameter tyres exhibit less casing deflection and thus, less energy loss.
Get The Leadout Newsletter
The latest race content, interviews, features, reviews and expert buying guides, direct to your inbox!
In the case of 29ers, there's the additional factor of 29er's lower angle of attack for anything other than a perfectly smooth ground surface. The longer effective lever requires less energy to overcome whatever tyre bulge exists at the contact patch so more forward momentum is maintained.
In addition, Wheel Energy's analyses of tyre contact patch have confirmed that 29" tyres don't have a bigger footprint than otherwise identical 26" ones. While the total area is the same, the shape of the patch is longer and narrower on 29ers, though.
Higher thread counts aren't always better: According to Wheel Energy, higher thread count casings are generally lighter and suppler than tyres with lower thread counts since they absorb less rubber during the vulcanisation process (non-vulcanised tyres such as most high-end tubulars exhibit their own characteristics).
However, they also suffer from decreased puncture resistance since the individual cords are thinner and easier to cut. Interestingly, Wheel Energy claims medium-count casings (around 60tpi) may offer the best all-around performance for everyday use. As compared to 120tpi casings, they can actually roll faster and are much more resistant to cuts while often carrying just a slight weight penalty.
If cut resistance is highest of your list of priorities, 30tpi tyres are apparently the way to go but you can also expect them to be heavy and slow rolling.
Puncture-resistant belts work but they're not created equal: Nylon, aramid, and other belts placed under the tread do help ward off flats but there are benefits and trade-offs to the various materials.
Tougher ones like aramid are durable and highly cut- and puncture-resistant but their stiff nature also sucks up a lot of energy, thus contributing to rolling resistance. More flexible ones like nylon aren't as bulletproof but offer a better compromise if you still want to retain good performance.
Tread pattern matters, even on the road: The importance of tread pattern is no surprise to the off-road world but common wisdom often says it's a non-factor on pavement where slick treads presumably would deliver the greatest surface contact with the ground and thus, the best grip. However, asphalt is far from a perfect – or even consistent – material. In those cases, certain tread designs can provide some measureable mechanical adhesion with the ground.
Inner tubes matter: Think there's no point in that expensive lightweight tube? Think again if you're trying to go faster. According to Wheel Energy's data, latex tubes roll ten percent faster than common 0.6mm-thick butyl tubes though today's ultra-thin butyl models come admirably close. Just in case you're wondering, the claimed limit of human detection for rolling resistance is about five percent.
How they do it
Wheel Energy's constantly evolving collection of testing machines are no miracles of design innovation or elegance but the fact that they exist at all is noteworthy in that as far as we're aware, it's the only independent test facility of its type in the world.
Currently, there are dedicated stations for rolling resistance, crown and sidewall puncture resistance, friction, and contact patch characterisation with additional apparatuses being designed and built as necessary. Each machine is fully custom-designed, built with computer-controlled hydraulic loading and fitted with industrial load cells for precise and accurate measurements.
Rolling resistance tests are conducted on large-diameter drums with various types of surface treatments, friction tests are done with a wide range of ground types (asphalt, concrete, etc.), and puncture tests can be performed using interchangeable tip sizes and radii. Conditions are kept constant throughout to foster repeatability.